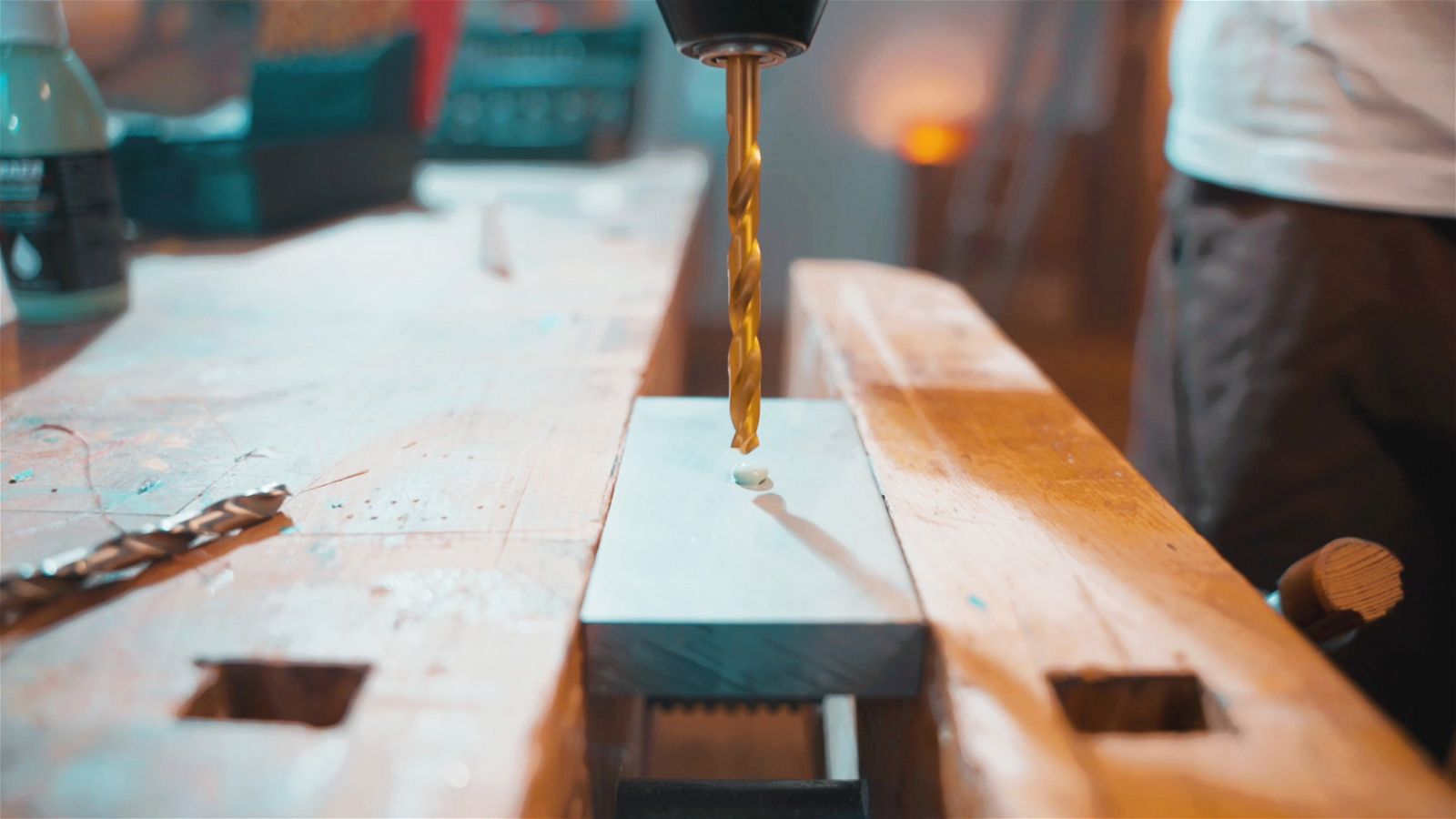
Drilling the core hole: It all depends on the right dimensions
No threads without a core hole, you probably know that. This essential step in thread creation might sound a bit complicated for beginners. After all, drilling can't be that hard, can it? Yes and no. While drilling a core hole generates a standard borehole, as you often do in your workshop, there are a few points to consider that can make or break the success of thread cutting. But don't worry, that's what we're here for. We'll explain why drilling a core hole is important and what you need to do to ensure the drilling is successful. Then you'll have no trouble drilling a core hole into which you can subsequently cut the perfect thread.
Why Is Drilling a Core Hole Important?
The "screw tap" doesn't drill a hole; instead, it removes material from the wall of a borehole with sharp cutting edges. You must create this borehole beforehand. Drilling a core hole is, therefore, a mandatory step without which thread tapping won't work. Each tool has its specific purpose, after all.
What Tool Do You Need to Drill a Core Hole?
This raises the question of the appropriate tool for drilling a core hole. Here's some good news: for drilling a core hole, you can usually use a standard twist drill bit — at least when creating a cylindrical hole. For tapered threads, you'd need a reamer, but we'll address that another time.
Of course, when choosing the right twist drill bit for drilling a core hole, you should consider a few points. Ensure that the drill bit is suitable for the material you've selected for drilling a core hole. If you're drilling a core hole with a handheld machine, it's best to center-punch the spot beforehand to avoid slipping. Drilling the core hole is most straightforward and clean with a stationary drilling machine.
Common Issues When Drilling a Core Hole
When drilling a core hole, errors and undesirable results frequently occur. The causes can be numerous. Insufficient coolant or incorrect values for cutting speed and feed can lead to excessive wear on the twist drill bit or result in incorrect borehole dimensions. Vibrations or an uneven surface during core hole drilling can often be attributed to unstable workpiece clamping or excessive runout error.
However, the most significant source of errors is the use of an incorrect drill size. This can result in the thread not having the desired dimensions. The worse case scenario is when the tap gets stuck or breaks. You should try to avoid this situation, as it renders your tool useless and can cause substantial damage to the workpiece. If you can't remove the broken tap gently, the entire component may become scrap. Paying attention to the correct dimensions is, therefore, crucial for the success of your work. Let's see how to approach this.
The Right Dimensions for Drilling a Core Hole
Due to the high potential for damage, the topic of "pre-drill diameter when drilling a core hole" can seem intimidating at first. When researching online, you often come across conflicting information. However, drilling a core hole is not that complicated, at least for threads with a 60° flank angle. So, let's address this case first.
Drilling a Core Hole for Threads with a 60° Flank Angle
For threads with a 60° flank angle, you can calculate the dimensions for drilling the core hole with a straightforward formula. This group includes metric standard thread M and metric fine thread MF, both of which are widely used in Germany and Europe. So, there's a good chance your project involves one of these threads. Other widely used thread standards with a 60° flank angle are American coarse thread UNC and American fine thread UNF.
The formula for calculating the dimensions when drilling the core hole is as follows:
Thread diameter (D) – Pitch (P) = Core hole diameter (Dk)
For a metric standard thread M 10 x 1.5, the calculation is 10 mm – 1.5 mm = 8.5 mm. So, when drilling the core hole, you should work with a core hole diameter of 8.5 mm.
Drilling a Core Hole for Threads with Different Flank Angles
Unfortunately, not every thread has a 60° flank angle. All British thread standards, for instance, have a 55° flank angle. The formulas for these threads are considerably more complex. We, therefore, advise against attempting to calculate the values for drilling a core hole yourself in these cases. Even small errors can have significant consequences, and deviations during core hole drilling are often associated with costly repercussions. So, how can you obtain the correct information when drilling a core hole?
Dimension Tables for Drilling a Core Hole
Others have done the complex calculations for you! You can conveniently look up the results in dimension tables for drilling a core hole according to the type of thread you want to use. This way, you'll avoid calculation errors, and you'll save time too.
By the way, dimension tables for drilling a core hole are also available for the metric ISO thread! If you're not a fan of calculations, you can easily look up the correct values for drilling a core hole even for threads with a 60° flank angle. We won't tell anyone!
You can find dimension tables for drilling a core hole in many places on the internet. For example, in the BAER online shop! For each product, we, as a screw tap manufacturer provide you with detailed information and reliable values for drilling a core hole. You can also find the appropriate twist drill bits with us. Take a look!