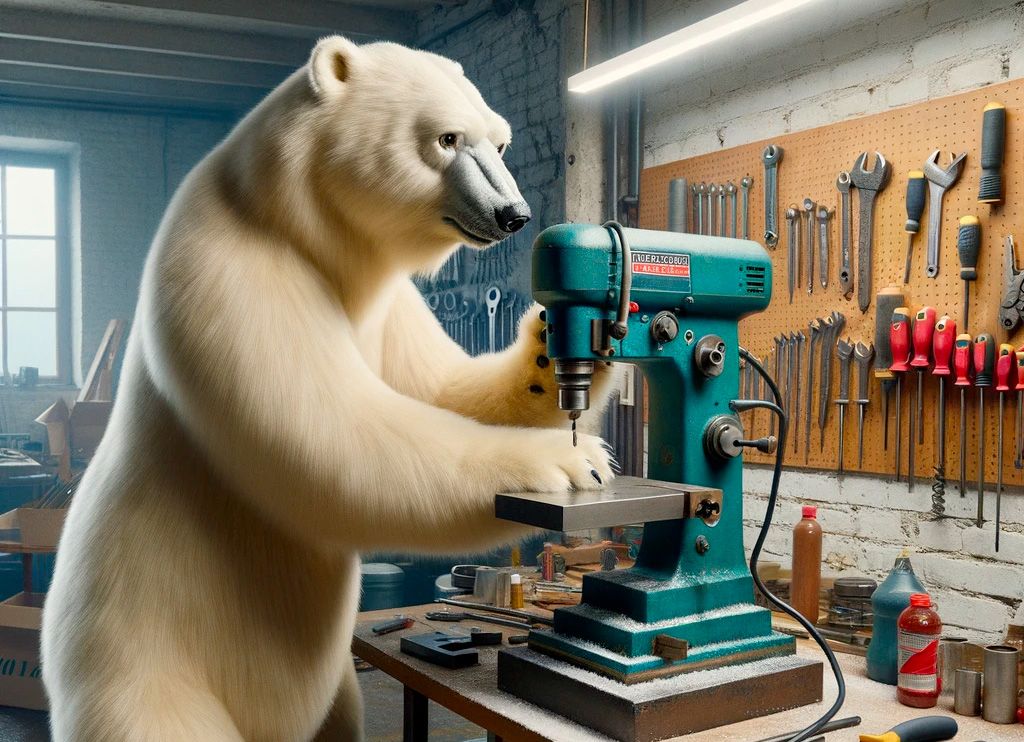
Core hole dimensions for screw taps: everything you need to know
If you are interested in thread tapping, you've probably already noticed that the first step is always the core hole drilling . This is where the hole is made, into which the thread will be cut later. This step is crucial and cannot be skipped! Just as important is the correct core hole size for screw taps. If it's too large or too small, then the thread won't work as desired. But don't worry, with us, you'll learn everything you need to know about the core hole size for screw taps. We debunk misconceptions, explain the simple drill formula for thread cutting, and for those of you who aren't fond of calculations, we have a solution ready.
Why core hole drilling at all?
The term screw tap might give some users the wrong impression that this tool itself drills the core hole into the metal. And there are indeed tools that can do that. These so-called combined taps combine tap and twist drill bit and can therefore be used without pre-drilling. However, this is an exception. As a general rule, the screw tap only cuts the thread; another tool is responsible for drilling.
This other tool is typically a conventional twist drill bit. Only for tapered threads is a reamer used to prepare a core hole in the required shape. However, most threads are cylindrical, requiring a parallel core hole, and for that, a drill bit is the simplest and best choice. You just have to use the right size. And this raises the question: how to calculate the correct drill for the thread?
Drill formulas for thread cutting
As manufacturers of taps, we often hear from our customers that incorrect formulas for core hole sizes are still circulating on internet forums and DIY plattforms. This results in miscut threads, broken drill bits, and a lot of frustration and disappointment in professional and hobby work. We find this sad and unnecessary, as determining the correct core hole sizes for screw taps is really not rocket science – at least for metric or other thread standards with a 60° flank angle.
A note on the flank angle
As you will soon see, the calculation formulas vary based on the flank angle of a thread. This is because there is a direct relationship between flank angle and thread diameter. The flank angle describes the angle between the thread teeth. This means the smaller the flank angle, the higher the thread peaks. This reduces the core hole size for the tap. You could say, with higher thread peaks, more material removal shifts to the scope of the tap.
Calculating core hole sizes for screw taps with a 60° flank angle
Many of the common thread standards have a flank angle of 60°. For all these threads, the core hole sizes for thread cutters can be determined using the same, simple formula. These threads include, among others:
- The metric standard thread M
- The metric fine thread MF
- The American coarse thread UNC
- The American fine thread UNF
To calculate the core hole sizes for screw taps with a 60° flank angle, we need the nominal thread diameter (D) and the pitch (P).
The formula is:
Thread diameter (D) – Pitch (P) = Core hole diameter (Dk)
Let's look at some examples:
The metric standard thread M 10 x 1.5 has a diameter D = 10 mm and a pitch P = 1.5 mm. Using the formula D - P, we subtract the pitch from the diameter. We get a core hole size for the screw tap of Dk = 8.5 mm.
Similarly, for the metric fine thread M 10 x 1.0. 10 mm diameter minus 1 mm pitch results in a 9 mm core hole diameter for the tap.
It's a bit more complicated for the American standards since the thread designation indicates the number of threads per inch rather than the pitch. You must therefore look up or calculate the pitch. Thankfully, it's not too complicated, as long as you know that 1 inch equals 25.4 mm.
Let's take the example UNF 1/2" x 20. The diameter D is 1/2", i.e., half an inch or 12.7 mm. Furthermore, we know that there are 20 threads per 1 inch (or 25.4 mm). So, we divide 25.4 mm by 20 to get the pitch P = 1.27 mm. Now we can apply our formula with the found values.
D – P = Dk
12.7 mm – 1.27 mm = 11.43 mm
Rounded up, this results in a core hole diameter of 11.5 mm.
Calculating the core hole size for screw taps for other flank angles
That sounded simpler than you might have thought, right? Well, unfortunately, not all threads have a 60° flank angle. For instance, all British Whitworth thread types like BSW, BSF, and BSP have a flank angle of 55°. The Rd-round thread only has a 30° flank angle, and on the other end of the spectrum, the PG-steel armored pipe thread comes in at a hefty 80°. For all these threads, the formulas for calculating the core hole sizes for taps are considerably more complex. And the more complicated the formula, the higher the risk of miscalculations. So, in these cases, you might want to rely on other sources to determine the appropriate size. Check out our tip at the end of this post!
Core hole sizes for thread formers
In addition to screw taps, there are also forming taps or roll taps. These produce internal threads not by removing material but by deformation. Even with this variant, you need to drill a core hole beforehand. Compared to thread tapping, the diameter here is slightly larger.
The formula for core hole sizes with forming taps is:
D – (0.5 x P) + 0.05 = Dk
Our Tip: Core hole size tables
If you generally don't like doing calculations or often work with thread standards that don't have a 60° flank angle, there's a simple solution. The calculations for all core hole sizes for taps have already been done by others before you – and the results have been summarized in handy tables. So, you can easily look up the measurements! Where? One option is in the online store of the tap manufacturer BAER with the table for thread cutter core hole sizes. Moreover, on our product pages, we've also linked the respective suitable table for you!