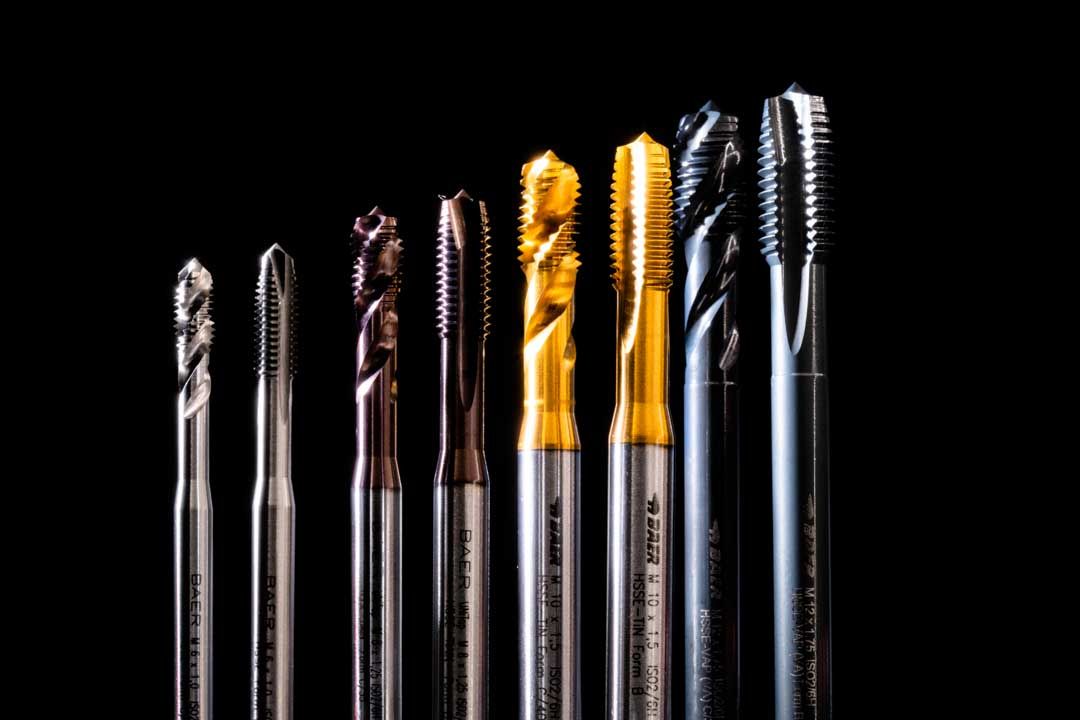
Coating of screw taps: What you should know
The base material is particularly important for the screw tap, directly influencing its quality and durability. However, your interest shouldn't stop here, as the surrounding processes also have significant effects on the tool's characteristics and overall quality. After all, the surface is the part of the screw tap most exposed to wear and corrosion. Therefore, most screw taps undergo a surface treatment or receive a surface coating before being sold.
Surface treatments and coatings offer a pleny benefits. For one, they increase the resilience against wear or environmental influences, leading to an extended lifespan for the taps. Moreover, they improve the surface quality and allow higher cutting speeds. Additionally, some advantages are specifically tied to individual treatment or coating properties, enabling the tap's use in special materials.
Currently, there are numerous variations and combinations of screw tap coatings. Additionally, many customer-specific coatings for taps can be inquired from the screw tap manufacturer BAER. We aim to bring some clarity to the colorful world of tap coatings.
The most common surface treatments
In a surface treatment, no material is applied to the screw tap; instead, the material properties of the substance are altered. There are several methods to achieve such modifications. We introduce some methods frequently applied to screw taps below.
Nitriding
Nitriding exposes the screw tap to a nitrogen-releasing atmosphere. With additional heat, a new surface layer forms. This coating on the screw tap has a significantly higher surface hardness, improved wear resistance, and better sliding properties than the initial product. This surface treatment is especially suitable for highly wear-inducing materials, such as cast iron, steels with higher perlite content, titanium alloys, AISi alloys with a high Si content (> 10 %), Bakelite, and other thermosets.
Vaporizing
Vaporizing is a steam treatment that triggers a chemical reaction on the tap's surface. This process creates a crystalline iron oxide layer, reducing the sliding resistance and also decreasing direct friction between the screw tap and workpiece. Moreover, lubricants adhere better to vaporized surfaces. All these factors prevent the emergence of buildup edges and cold welding. However, vaporizing is only suitable for iron materials.
Calduring
Calduring combines the two processes of nitriding and vaporizing, allowing for dual benefits. This treatment is particularly beneficial for working with materials that are both tough and wear-inducing.
Hard chromium plating
Hard chromium plating produces a hard chrome layer through electrolytic deposition. This enhances the sliding properties and also reduces the surface roughness. Hard chromium plating is used when machining materials with low strength, mainly copper and Cu alloys. However, the machining temperature must stay below 250°C, as only then the advantages are fully utilized.
The most common screw tap coatings
For tap and cutting die coatings, they often represent the most ecologically and economically advantageous variant for improving surface properties. There are many methods for applying coatings. However, for tap and cutting die coatings, the PVD method is primarily used. Let's first take a closer look at this method before diving into the main coatings for taps and cutting dies.
The PVD process for surface coating
PVD stands for physical vapour deposition. It's a vacuum-based coating process in which the coating material is first turned into a gaseous state. In this form, it then encounters the threading tool and condenses there, forming the desired coating on the tap.
TiN (Titanium Nitride)
A screw tap coated with titanium nitride is identified by its gold-yellow color. The screw tap coating offers a micro-hardness of 2,200 HV and a temperature resistance of up to 600°C. The TiN coating is a general-purpose coating, mainly used for soft to tough-hard steels, cast iron, and many non-ferrous metals. Tools with TiN coating can also be recoated up to five times.
TiCN (Titanium Carbonitride)
The titanium carbonitride layer is very hard and tough, showcasing its strengths primarily under high mechanical stress. It has a micro-hardness of 3,000 HV with a temperature resistance of up to 400°C. A TiCN-coated screw tap is gray-violet. Classic applications for this coating are high-strength steels and abrasive materials. Additionally, TiCN has a high resistance to impact stress, making it ideal for interrupted cuts. Its only weakness is its low heat resistance, so adequate cooling is crucial with TiCN-coated taps.
TiAIN (Titanium Aluminum Nitride)
The TiAIN tap coating is black-violet with a micro-hardness of 3,300 HV and a temperature resistance of up to 800°C. The high chemical stability and heat resistance make this coating particularly suitable for applications with high temperature stress and limited cooling options. This makes it ideal for high cutting speeds of over 60 m/min and for abrasive and hard-to-machine materials. Screw taps coated with TiAIN can also be recoated up to five times.
Other coatings
In addition to these three standard coatings, numerous variations exist for a wide range of applications. The red-violet, multilayer X. TREME tap coating combines the properties of TiN, TiCN, and TiAIN. The combo layer of TiAIN combined with a soft material glide layer is ideal for dry machining. The silver-gray CrN (Chromium Nitride) coating has very high thermal stability and corrosion resistance.
If you're still unsure about the right surface treatment or coating for your project, don't hesitate to ask us! At the BAER customer service office, dedicated employees are eager to assist in realizing your plans. All mentioned variants are available in our online shop, or we can quickly produce coated taps from BaerCoil based on your specifications.