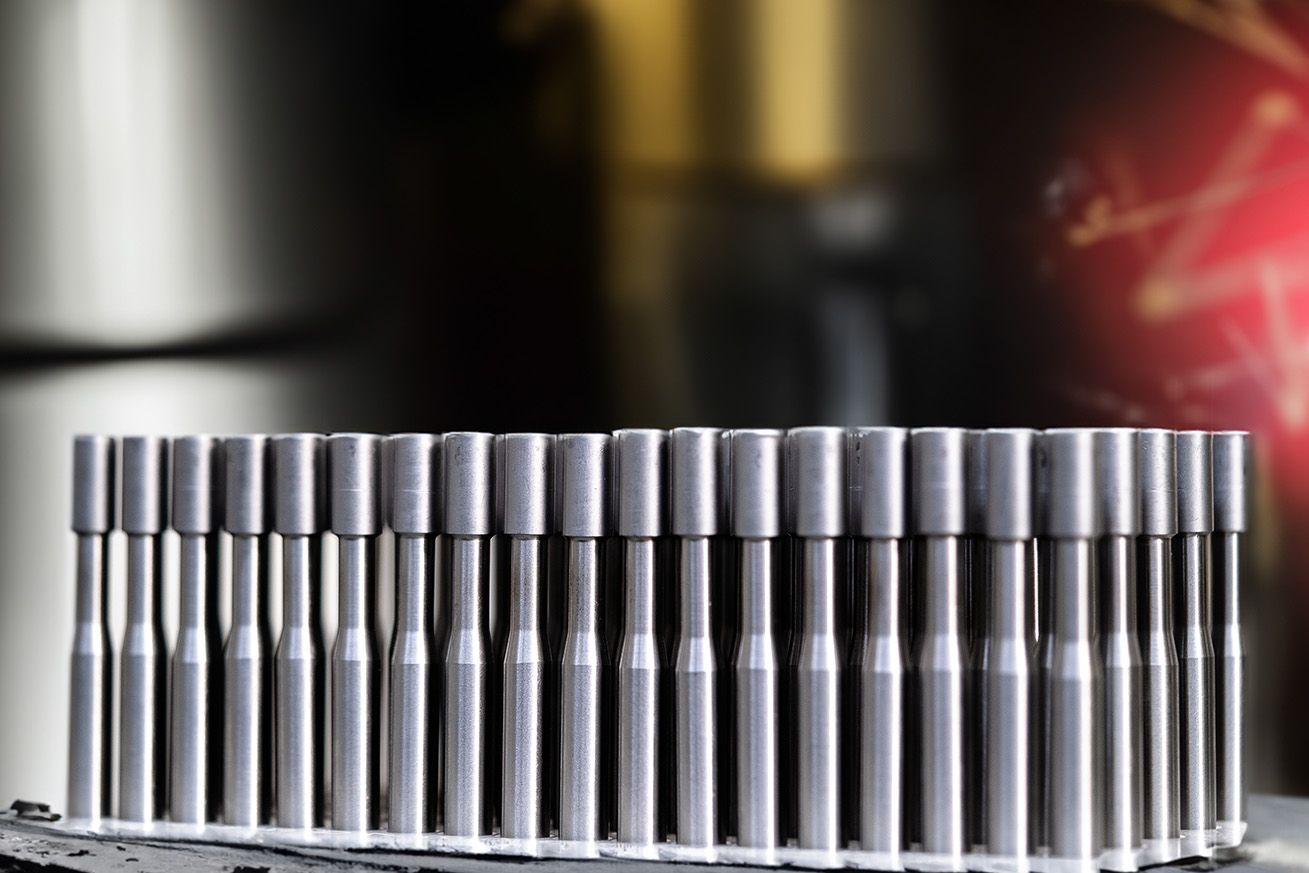
HSS & Co. - Basic materials for taps
Every tap and die you hold was once a glowing lump of steel. If you've never thought about it, it's time you did. Because what happens to the screw tap before it ends up in your toolbox has a significant impact on the quality and smooth operation of your work.
You realize the importance of the steel from which screw taps are made when a subpar tool breaks on you. To make informed purchasing decisions in the future, let's explore the primary material for drills, taps, and step drills: HSS or High-Speed Steel. We'll delve into its properties, variations in manufacturing, and how these differences are reflected in the naming of tools.
What properties should the steel have from which screw taps are made?
Before we dive in, let's consider the demands made on steel from which taps are crafted.
Essentially, these can be narrowed down to three main points:
- Resistance to deformation
- Break resistance
- Wear behavior
Screw taps are precision tools that can be exposed to extreme strains. They shouldn't permanently deform under stress, but rather retain their original geometry. They also need to be tough enough to resist breaking under pressure. Lastly, taps should exhibit good wear behavior, minimizing signs of wear and tear.
Not All Steel is Created Equal: HSS & Beyond
In everyday language, we often use the term "steel" without specifying its type. This generalization overlooks the plethora of classes, groups, and varieties under this broad category. All steel shares a carbon-iron alloy base. Beyond this, numerous factors, such as its precise composition, purity, manufacturing process, and many more, create a vast array of steels. The steel from which high-quality taps are made belongs to the category of High-Speed Steels (HSS), which itself has many variants. Let's explore the differences among HSS types.
Alloying
The type and concentration of alloying elements greatly influence the properties of High-Speed Steel. Each element introduces advantages and disadvantages that need careful consideration. This balancing act is particularly evident with cobalt. While cobalt alloying significantly increases HSS's heat resistance, it also increases the risk of breakage.
The most common alloy types for High-Speed Steels include:
- Base alloy: Standard HSS with typical resistance to temperature and wear.
- Vanadium-alloyed: Offers increased wear resistance.
- Cobalt-alloyed: Produces greater hardness and heat resistance.
- Vanadium-cobalt alloyed: Provides increased wear resistance and heat resistance but decreased toughness.
- Reduced tungsten, increased vanadium: Very wear-resistant but with less heat resistance.
Manufacturing Process
There are two primary methods for producing HSS. The more commonly used method is melting metallurgical production. Here, the steel is melted, mixed with desired alloying elements, and then cast into bars. This is followed by several processing steps aimed at evenly distributing the components and enhancing the steel's purity. The material is then rolled and forged.
The powder metallurgical production of HSS is less common. In this method, molten steel is atomized and subsequently hot isostatically pressed. This allows for higher alloying concentrations and results in a particularly homogeneous composition of HSS.
High-Speed Steel also undergoes a heat treatment, which imparts the needed heat resistance and strength. The HSS is first heated, cooled, and then reheated in a process called tempering.
Further Processing
After initial production, there are various ways to treat HSS to achieve additional desired properties. These include mechanical modifications such as grinding, surface treatments like nitriding, or coatings.
High-Speed Steel (HSS): The material from which drills are made
Now that we have an understanding of what constitutes HSS, we can appreciate that it provides high temperature resistance, facilitates rapid cutting speeds, and offers solid break resistance. Within the broad category of High-Speed Steels, there are many variants distinguishable by specific codes. Let's explore some of the most common ones.
HSS
HSS stands for High-Speed Steel. This is simply the standard form without any special alloying elements or treatments. It's an all-rounder material, ideal for general applications without extreme demands.
HSSE
HSSE denotes a screw tap made from HSS with an extra alloy, often cobalt. HSSE taps are especially hard, with good heat resistance. However, this comes at the expense of a higher risk of breaking.
HSSE-V3
The V3 suffix indicates an added vanadium content along with cobalt. Vanadium increases hardness and reduces wear but is rarely used in concentrations exceeding 3% as it can create challenges during manufacturing.
HSSG
The G in HSSG doesn't refer to an alloying element but to the manufacturing process. It denotes “ground.” HSSG taps are manufactured through grinding processes, making them particularly precise. Grinding also enhances tool life and chip evacuation.
HSSE-PM
The PM stands for powder metallurgy, a production method discussed earlier. Screw taps made from this type of HSS exhibit exceptional wear resistance, heat resistance, and pressure resistance. They are also tough and easy to grind. Their smooth surface after grinding reduces friction when the tap cuts threads.
So, Which HSS Steel is the Best for Taps?
If you've come this far, you might be wondering which steel is truly the best. Generally, always ensure that HSS is used and not some inferior tool steel. Within the HSS category, no single variant stands out as the absolute best. Instead, each type is "the best" for its specific application. So, always choose based on your requirements.