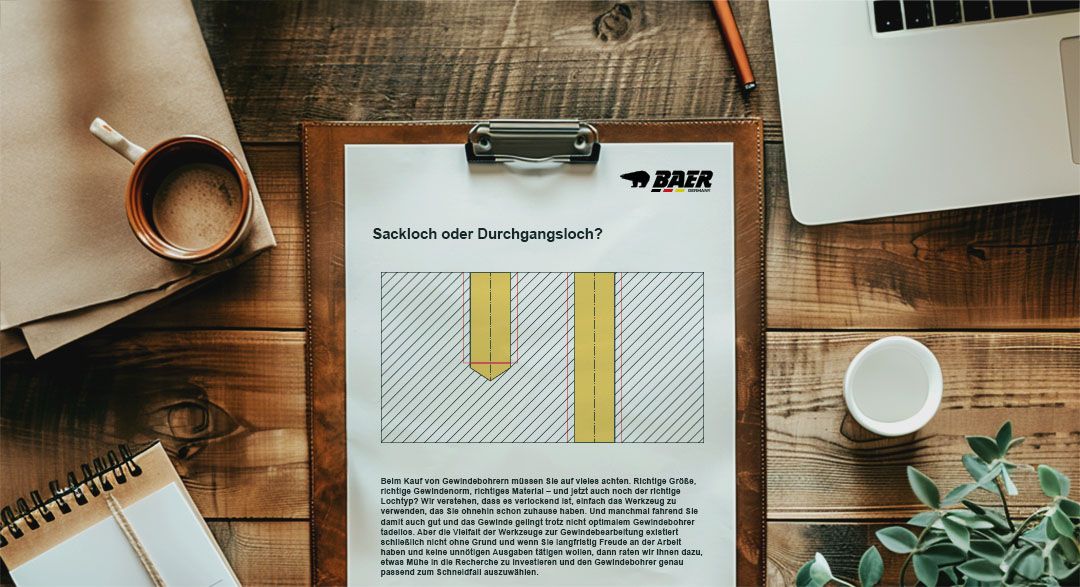
Blind hole or through hole?
When purchasing screw taps, there are many factors to consider. The right size, the correct thread standard, the appropriate material – and now, the right hole type? We understand that it's tempting to use the tool you already have at home. Sometimes, it works well, and the thread turns out perfectly despite not using the optimal screw tap. However, the variety of threading tools exists for a reason. If you want long-term satisfaction in your work and avoid unnecessary expenses, we recommend investing some effort in research to select the screw tap that precisely matches the cutting situation.
As always, we are here to assist you. This brings us back to the topic of holes. The difference between a blind hole and a through hole is quickly explained, and choosing the right screw tap for each won't be a mystery anymore. You will see that it makes sense to use different tools for blind holes and through holes. Let's find out what they are and how to identify them.
What is the difference between blind hole and through hole?
When you think about it, there are only two possibilities for drilling. Either you drill completely through the workpiece, or you drill only a portion into the material. And that's the difference between a through hole and a blind hole. The latter is often referred to as a pilot hole, precisely because the hole has a purpose.
There are many reasons to use a blind hole or a through hole, from construction considerations to aesthetic arguments. In any case, threading through a through hole is somewhat easier. However, this doesn't mean blind holes are particularly difficult to work on. You just need to know which screw tap you need.
How screw taps for blind holes and through holes differ
Two main points play a role in choosing the right screw tap for a blind hole: chip removal and thread depth. To address these issues, screw tap for blind holes and through holes differ in the flutes and the chamfer. Let's take a closer look.
Screw taps for blind holes and through holes have different flutes
When threading, the question always arises, where to direct the chips? They can't stay in the hole because they would cause problems. The through hole has an opening through which removed chips can fall out, reducing chip-related issues. In a blind hole, however, chips would accumulate at the bottom of the hole. Therefore, they need to be directed upward against the cutting direction. This is achieved by right-twisted spiral flutes. Like a small screw conveyor, they push the chips upward, elegantly solving the chip problem. Screw tap for through holes, on the other hand, usually have straight flutes. The drawback of spiral flutes is the so-called corkscrew effect, which, under excessive pressure, can lead to thread misalignment. Therefore, some attention is required.
The chamfer geometry varies between screw taps for blind holes and through holes
Every screw tap has a chamfer. This refers to a specific number of thread turns at the tool's tip that perform the majority of the cutting work. However, these initial thread turns are not fully formed and only reach the nominal diameter towards the end of the chamfer. This isn't a problem for a through hole because you can continue turning the screw tap until the entire chamfer emerges at the bottom. This ensures that the thread is fully formed over the entire length. In a blind hole, there is usually no space to turn the screw tap significantly deeper than the intended thread length. Therefore, the chamfer must be as short as possible so that the part of the thread at the hole's bottom, where the thread turns are not fully formed, remains minimal. Hence, the number of turns in the chamfer differs between screw tap for through holes and blind holes. While screw tap for through holes may have 4 to 5 or even more turns in the chamfer, blind hole tap drills usually have only 2 to 3 turns.
Are screw taps for blind holes and through holes interchangeable?
The question arises: if blind holes pose greater demands on the drilling type, wouldn't it be more sensible to use blind hole screw taps for both scenarios? Indeed, interchangeability in this direction is much higher than the reverse. While you can often achieve good results with a blind hole screw tap in a through hole, using a through hole tap in a blind hole almost always leads to problems. Nevertheless, in most cases, it is not advisable to completely switch to blind hole screw taps. More precisely, it would not be very cost-effective.
As we've seen, the chamfer on a blind hole screw tap is much shorter. The force required to cut a thread is the same for both blind holes and through holes. The shorter the chamfer, the higher the load acting on an individual thread turn. This means that blind hole screw taps wear out much faster, resulting in shorter tool life compared to screw tap for through holes. Therefore, it would not be very sustainable to use blind hole taps for cutting situations where a through hole tap is also suitable. Invest in tools that perfectly match your application, and benefit from longer tool life for all your screw taps.
Convinced? You can find high-quality screw taps for blind holes and through holes in our BAER online shop. Take a look!