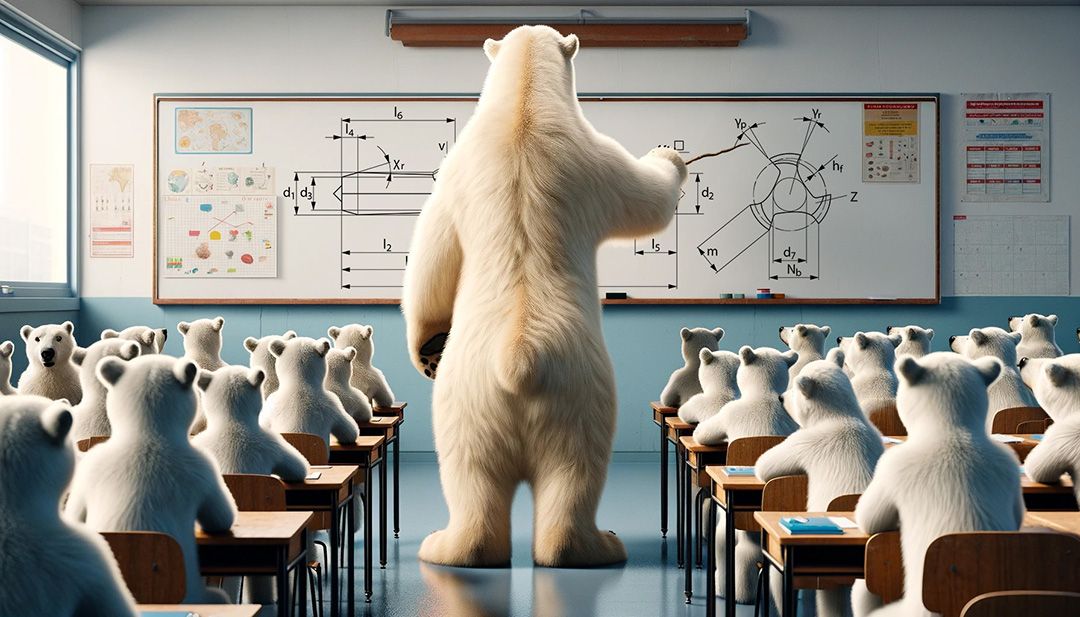
Ensure the correct rake angle on the screw tap
Thread cutting unfortunately has the reputation of being somewhat complicated. Perfect results are said to be hard to achieve, and the screw tap is prone to breaking. Does this sound familiar to you? If so, it might be time to get more familiar with the geometry of a screw tap. Most problems can be easily avoided when you know what causes them.
Today, we start with the rake angle on the tap, sometimes also called cutting angle. The rake angle is one of the most important angles in thread cutting, and as the name suggests, it mainly influences chip formation. And chip formation is ultimately one of the decisive factors for the success of thread cutting. In this post, we'll reveal how the right rake angle can prevent chip problems and how you can leverage your knowledge of the helix angle for better results.
What is the helix angle, anyway?
Before we can explore the consequences of choosing the rake angle for thread cutting, let's first look at some basics. It gets a bit technical, but stick with it – the better you understand, the easier the work will be later!
Where is the rake angle on the screw tap?
The first question to clarify is where the rake angle is located. The rake angle is the angle between the chip surface and the so-called tool reference plane; this is the plane in taps defined by the axis of rotation and the cutting point, which we want to consider.
And now, let's make it clear. Imagine our tap in a top view, preferably somewhere halfway along the thread length. Now, find the exact center and draw a straight line from there to the outermost tip of one of the cutting edges. The angle between this imaginary line and the chip surface is the rake angle.
The rake angle is of great importance for chip evacuation
The rake angle on the tap determines how the chip is formed, how it looks, and how well it can be evacuated. The size of the rake angle is crucial for this. The rake angle can be positive, negative, or even at 0, but in thread cutting, it is usually in the positive range. In simple terms, the rake angle determines how blunt or sharp a cutting edge is – with all the resulting consequences.
The rake angle directly influences the cutting performance of the screw tap
The rake angle appears in some formulas used to calculate central forces during thread cutting. Primarily, the cutting force. This is the force required for the deformation and separation of chips and for overcoming friction. It is directly related to the size of the rake angle. The larger the rake angle, the smaller the cutting force. The same applies to the cutting force. Thus, the rake angle also affects the cutting performance of the screw tap.
What impact does the rake angle have on thread cutting?
Let's examine what exactly the rake angle causes in thread cutting. Because both a small and a large rake angle have advantages and disadvantages that must be carefully weighed against each other. There is no perfect rake angle, only the best compromise for a specific cutting case.
Large rake angles ensure consistent chip formation and reduce cutting force. The cutting edge becomes sharper but is also more vulnerable to damage. A smaller rake angle increases cutting force and also generates more friction, which can lead to a decreasing surface quality on the workpiece and also increases wear. However, cutting edges with a small rake angle are more stable and produce shorter chips, which can be a desired effect depending on the application.
This is the rake angle your screw tap should have
Now you probably want to know what rake angle your tap should have. This primarily depends on the material you are working with. Generally, the rule is: the harder to machine a material, the smaller the rake angle should be. Conversely, for soft materials, the rake angle can be much larger. For brittle brass, for example, a rake angle of under 6° is suitable, while soft aluminum can be machined with rake angles of over 18°. To provide more overview, materials with similar properties are grouped together and marked with different colors. The exact rake angles vary depending on the intended application and may also vary slightly depending on the manufacturer.
The good news for you is that renowned manufacturers like BAER invest time in thinking about the rake angle for you. That's why there are so many different screw taps! When making a purchase, ensure that your screw tap is suitable for the material you want to work with – then the rake angle is likely to be correct. And if for some reason it's not, rake angles can be corrected afterwards by grinding.
Caution, risk of confusion: rake angle, side rake angle, or a completely different angle?
Unfortunately, the rake angle is not the only important angle on the screw tap. There's also the side rake angle. Due to the similarity in names, confusion can easily arise. The side rake angle is often referred to as the spiral angle because it is formed by the helix of spiral flutes.
Closer to the rake angle are the wedge angle and relief angle. Together, these three angles always add up to 90°. The clearance angle is somewhat the counterpart to the rake angle on the other side of the cutting edge, which is defined by the wedge angle.
Want to ensure that the rake angle on your screw tap is perfect for your cutting case? Then find high-quality tools with precisely calculated cutting geometry in the BAER online shop. Take a look!