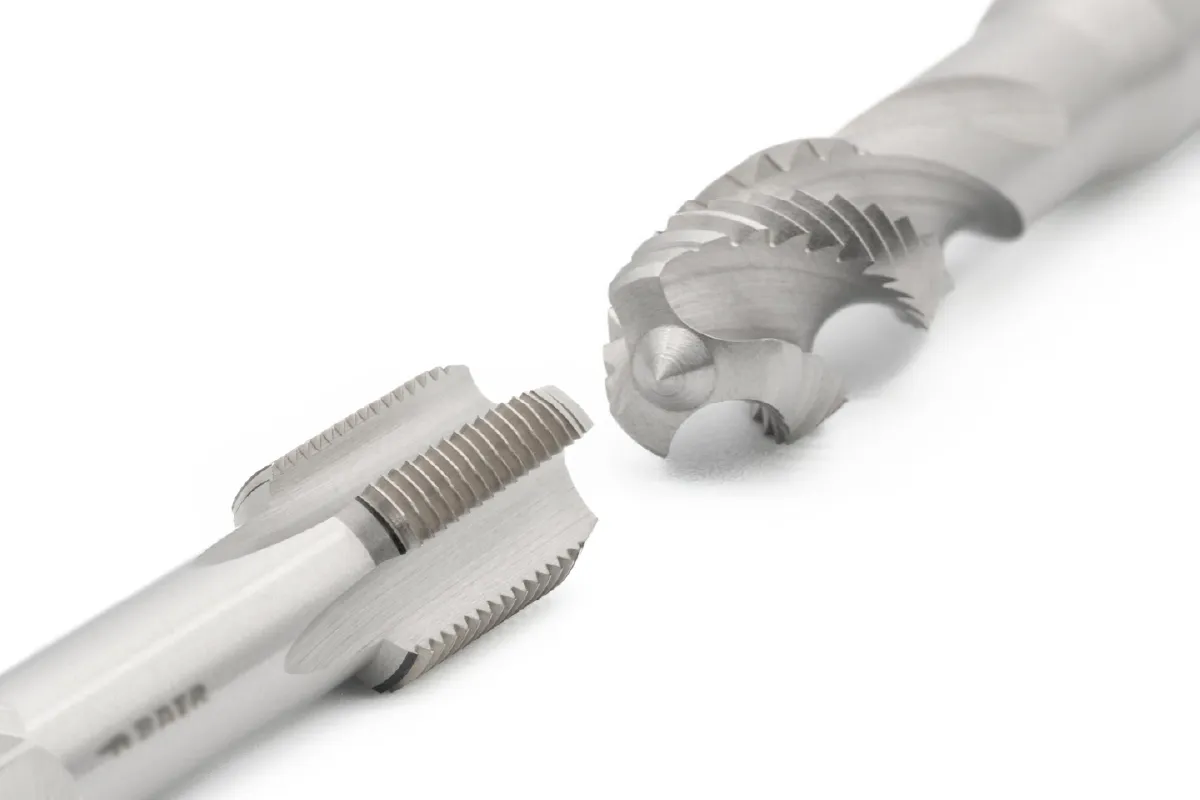
Hand Taps vs. Machine Taps: Threading Tools in Detail
To cut a thread, you need a tap – that much is clear. But which one should you use? And are there actually other options? Today we're taking a deep dive into the world of threading tools, their special features, similarities, and differences, and we'll clarify which tool is best suited for which threading application.
Hand Taps: Precision by Hand
Hand tap sets are your best choice when you want to work without machines, are dealing with easily machinable materials, and have a bit of patience. Hand taps give you great mobility, but they are not the fastest option.
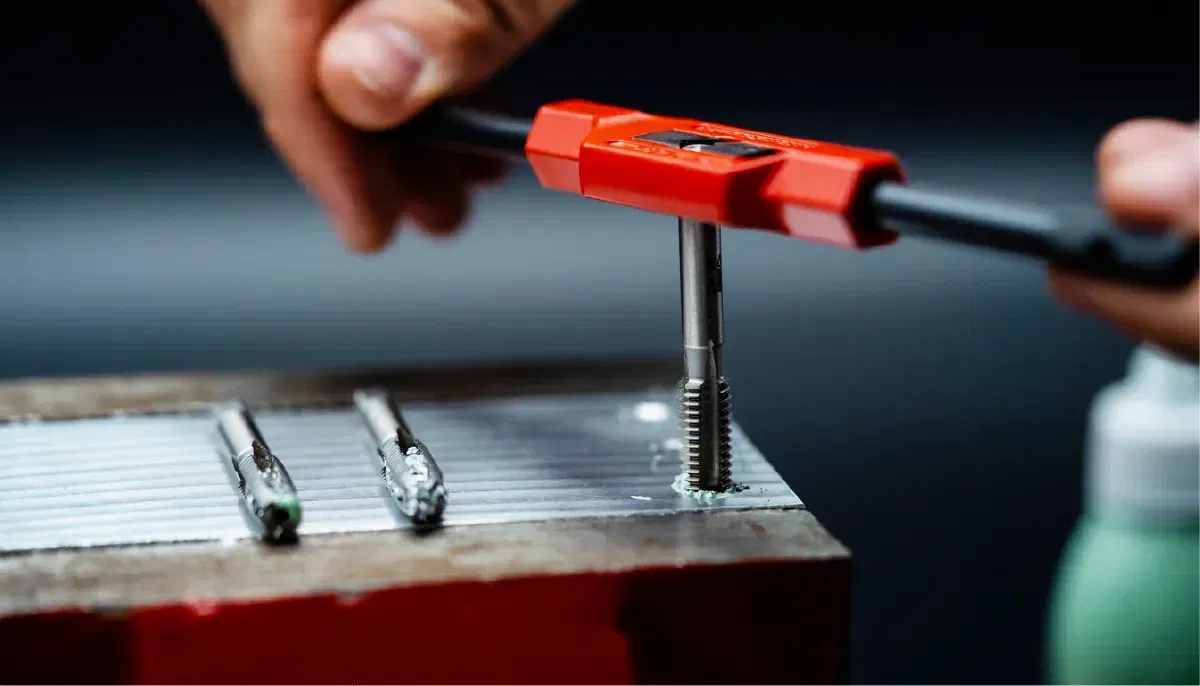
Because you're working without machine assistance, the required cutting force is distributed across three taps: pre-tap, intermediate tap, and finish tap. Fine thread sets usually omit the intermediate tap.
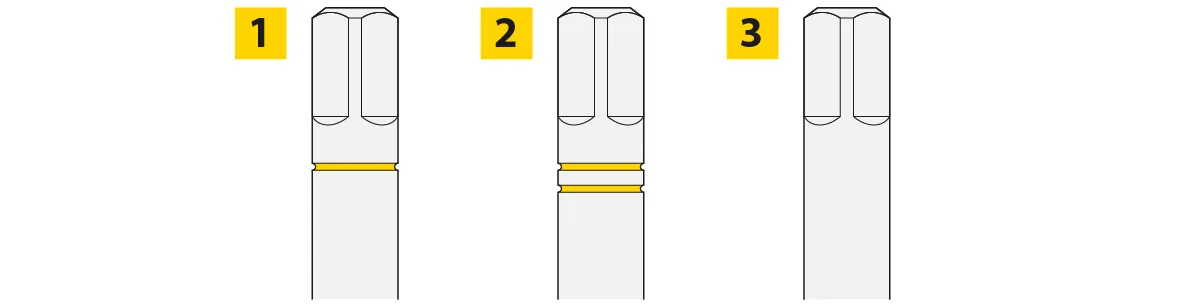
Hand taps require a holding tool like a ratchet or tap wrench. The tool is clamped in and off you go – slowly and carefully. To create a proper internal thread, you must always keep the tap aligned perfectly straight.
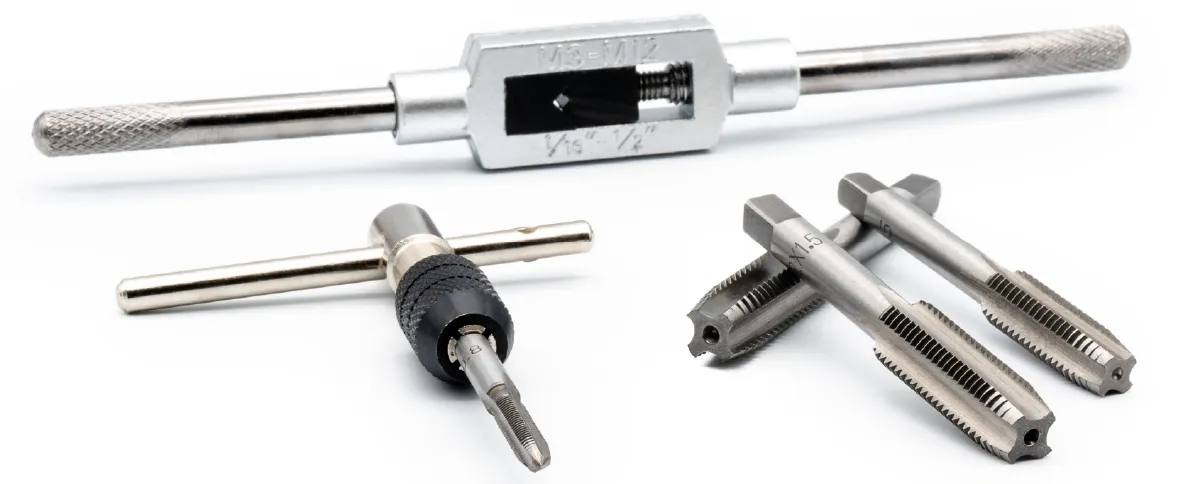
Machine Taps: Versatile for All Threading Applications
Too slow and meditative for your taste? Then machine taps might be more up your alley. Things move quickly here, and you only need one tool to cut the thread in a single operation. Perfect for series production. Machine taps are driven by stationary drills, tapping machines, or CNC machines – whatever you happen to have in your workshop.
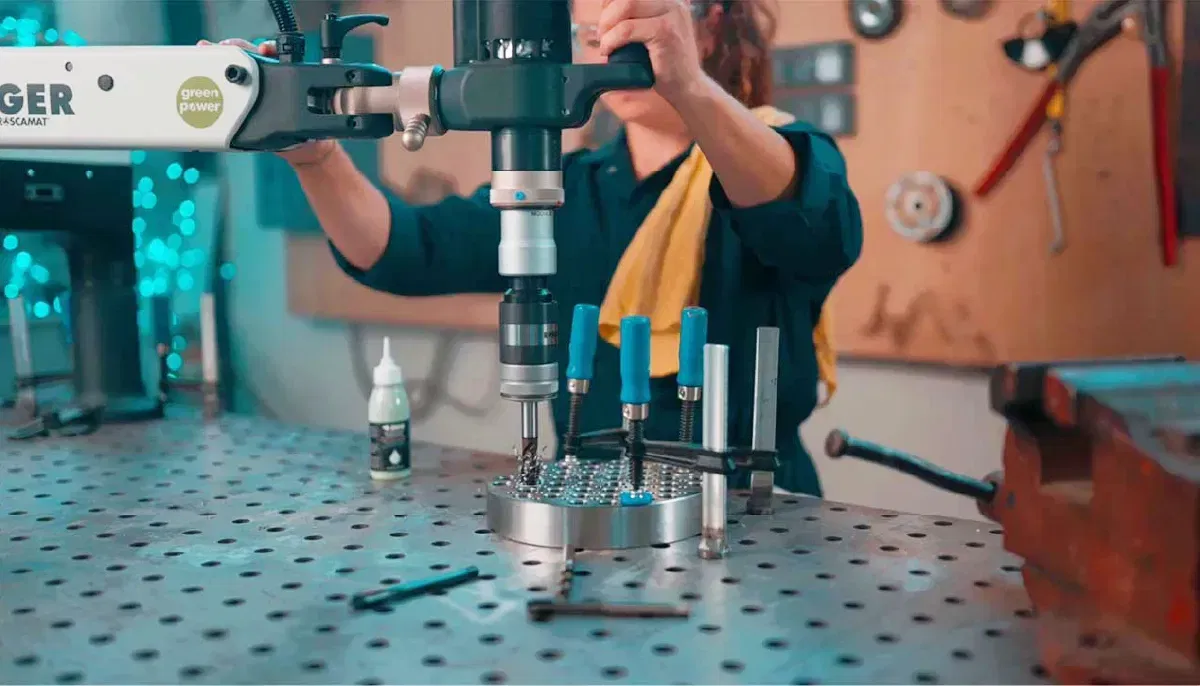
Machine taps come in countless variants for every thread type and material. They can be categorized by various features: different flute shapes, chamfers with or without point cut, matching thread profiles – the list of specializations is long.
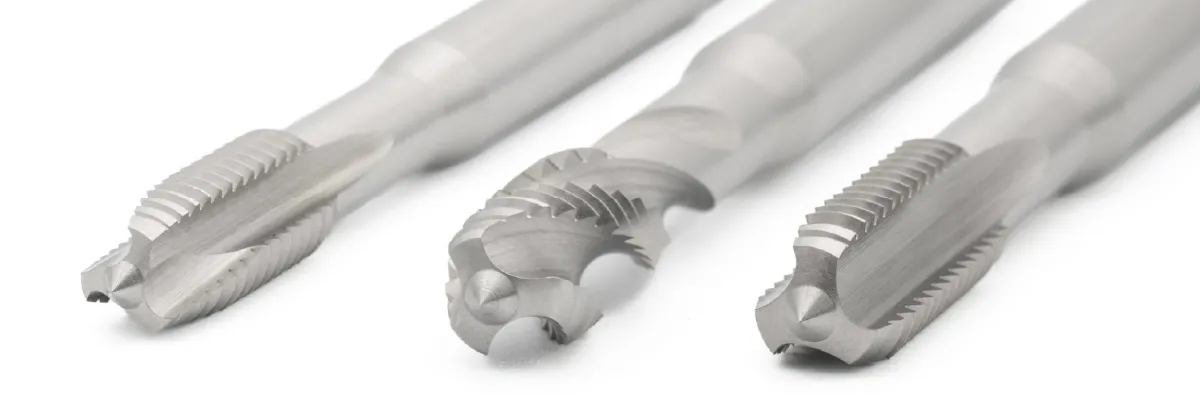
This product diversity has its reasons. Steel has different properties than brass, blind holes present different challenges than through holes, and of course, DIN standards must be followed.

One-Cut Taps: Efficient and Flexible by Hand or Machine
If you're undecided, take a closer look at the one-cut tap. It works both manually and with machines. When used by hand, it's fast and efficient because it produces the thread in just one cut – hence the name. It can also be flexibly used in a machine when cutting many threads in succession.
As with any all-rounder, there are compromises. The one-cut tap is best suited for general applications in well-machinable materials. For specialized cases or recurring problems, it’s best to look for a dedicated specialist among machine taps.
Dies: A Useful Addition to Taps
Internal threads are one thing – but what about external threads? To produce those, you’ll need a die. Again, you can choose whether to work by hand or with a machine.
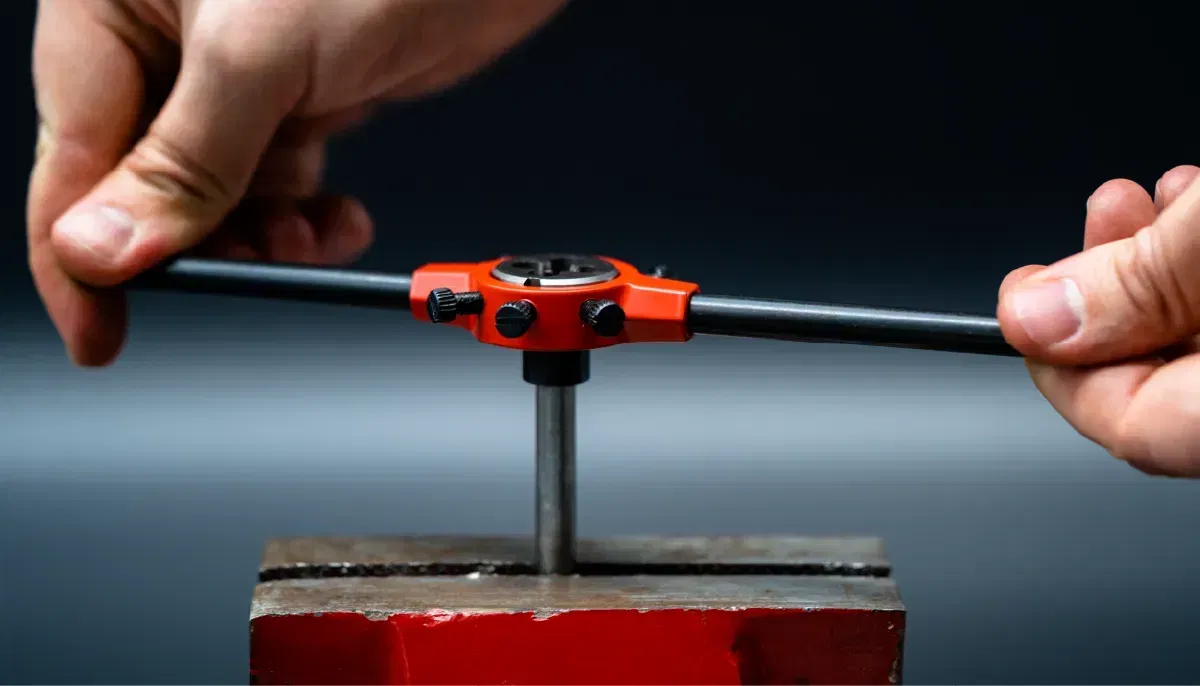
For manual use, you'll need a die holder and ideally a die guide, because correct tool alignment is once again crucial. Besides round dies, there are also hexagonal dies that can be used with a standard open-end wrench. They are especially useful for re-threading or for work in hard-to-reach areas.
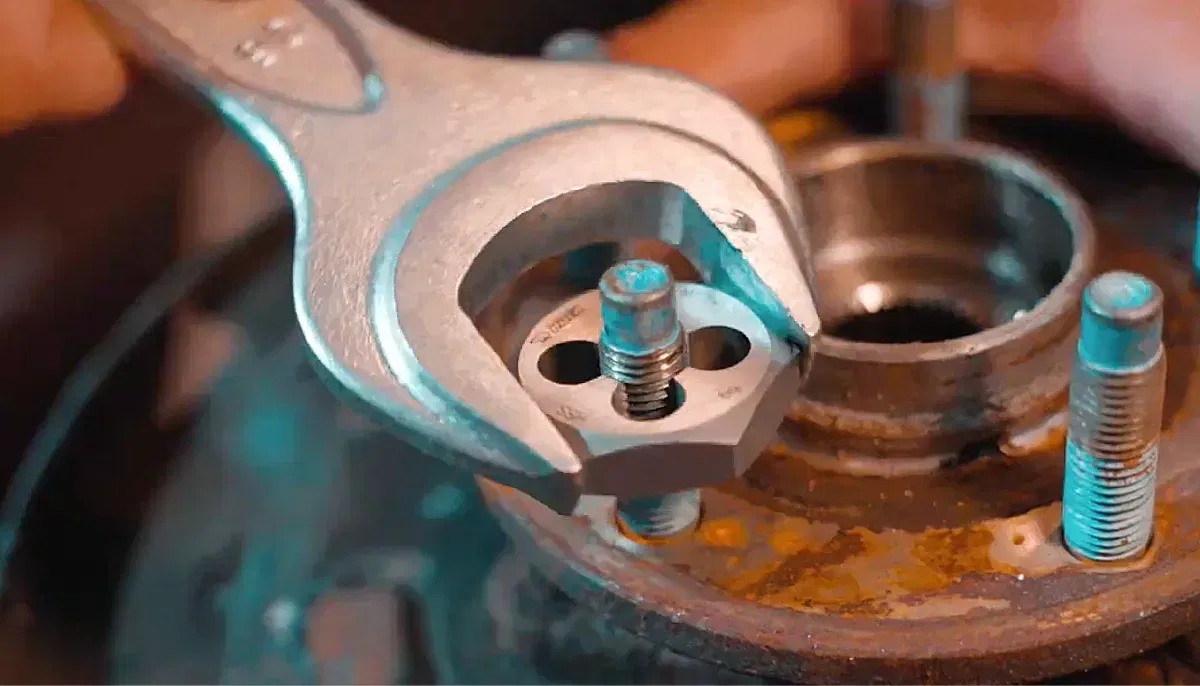
For machine use, you can use the same dies as for manual threading. You’ll just need a suitable die holder for your machine.
If You Want Chipless Threading: Thread Formers
Taps aren’t the only tools for creating threads. Very similar is the thread former. The difference is that thread forming is not a cutting process. No material is removed; instead, the thread is formed by displacing the material.
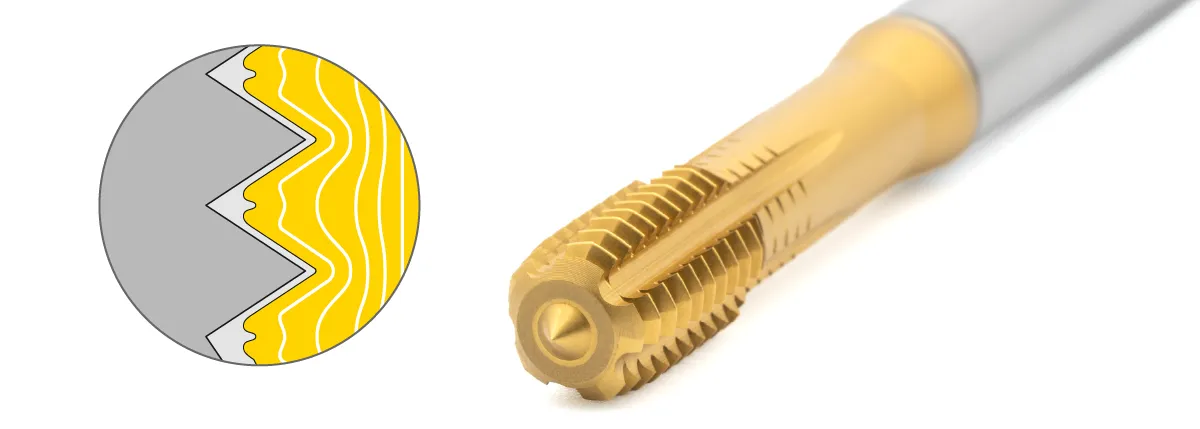
The advantage of this method is that no chips are produced that could clog the thread and cause problems. Since the material fibers remain intact, a high-quality surface finish is also achieved. However, thread formers are not suitable for all materials and are very limited for manual use.
Twist Drills: Essential Helpers for Tapping
Whether you're using taps or thread formers, there’s one preparation step you can't skip: the core hole drilling. And for that, a high-quality twist drill is indispensable. So twist drills can certainly be counted among the group of threading tools.
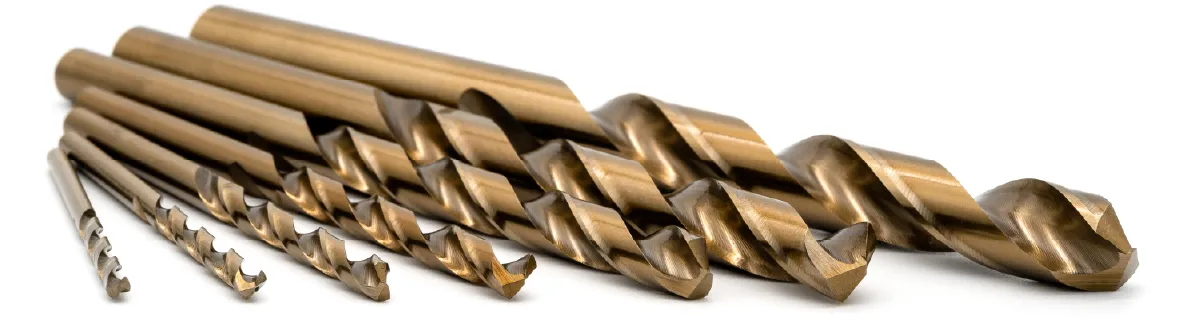
When drilling, the diameter is key. Only when the core hole diameter is correct can a proper thread be cut. Threading sets make things easier by including matching twist drills. Otherwise, you can rely on tables or the simple formula Thread Diameter (D) – Pitch (P) = Core Hole Diameter (Dk) for threads with a 60° flank angle.
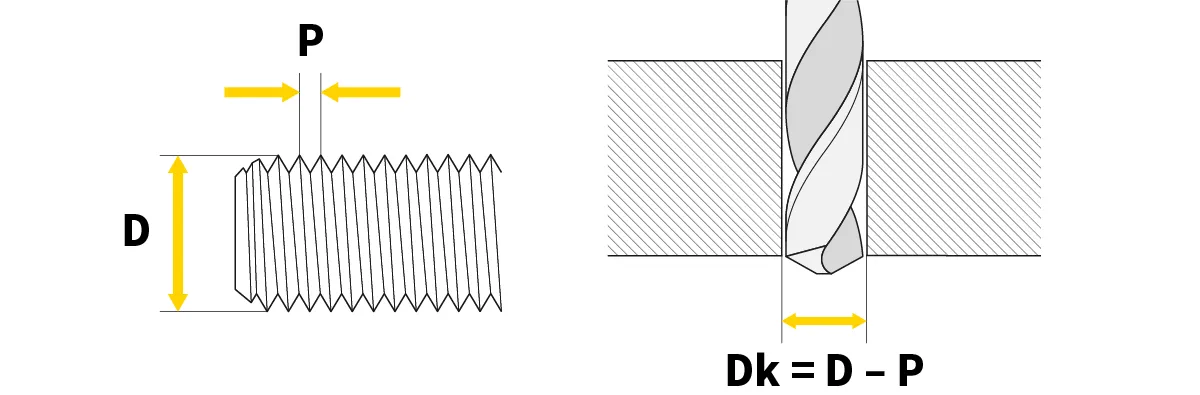
Of course, the twist drill must also be suited to the material you’re working with, just like the tap. If you're working with stainless steel or other challenging materials, choose a drill specifically designed for that.
More than Just Taps: Milling, Rolling, and More
Several additional methods can be used for thread production. So technically, thread mills and thread rolling tools are also considered threading tools. However, these specialized tools require the right machinery and a specialized working environment that’s rarely found in home workshops or small craft spaces.
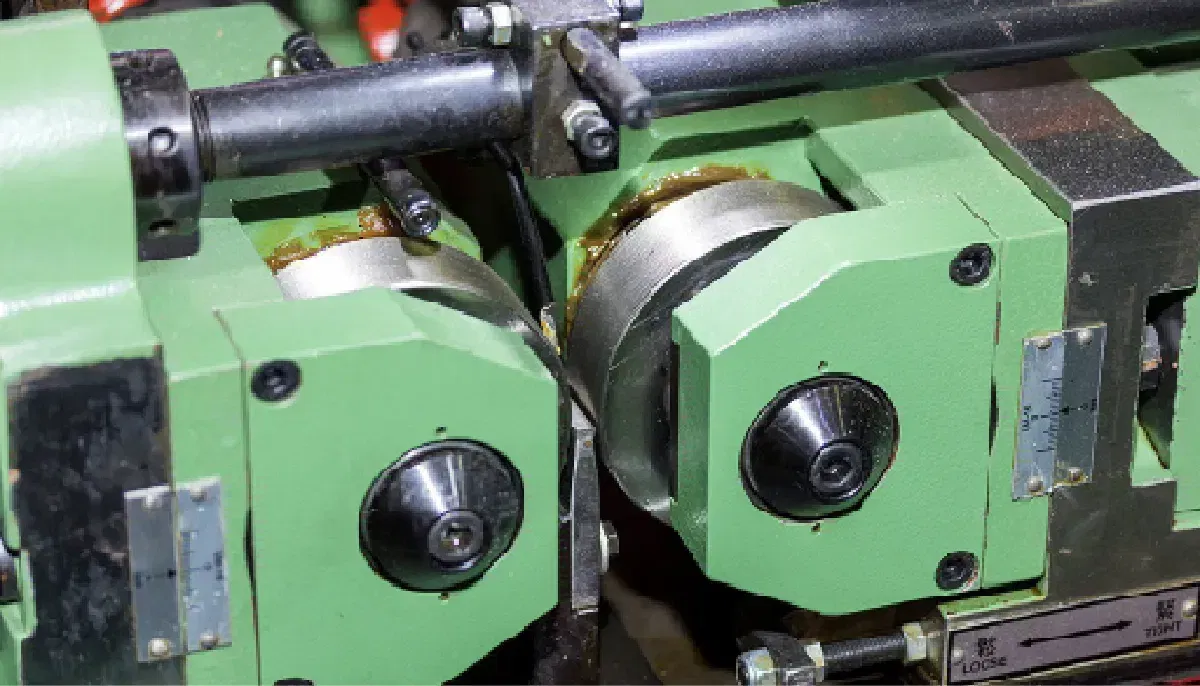
Whether it’s taps, thread formers, dies, or twist drills – at BAER, you’ll find everything you need for your threading needs. Our extensive selection is sure to include the right addition for your project. See for yourself and visit our online shop! If you have any questions or need assistance, our customer service team is available by phone or via our contact form at any time.