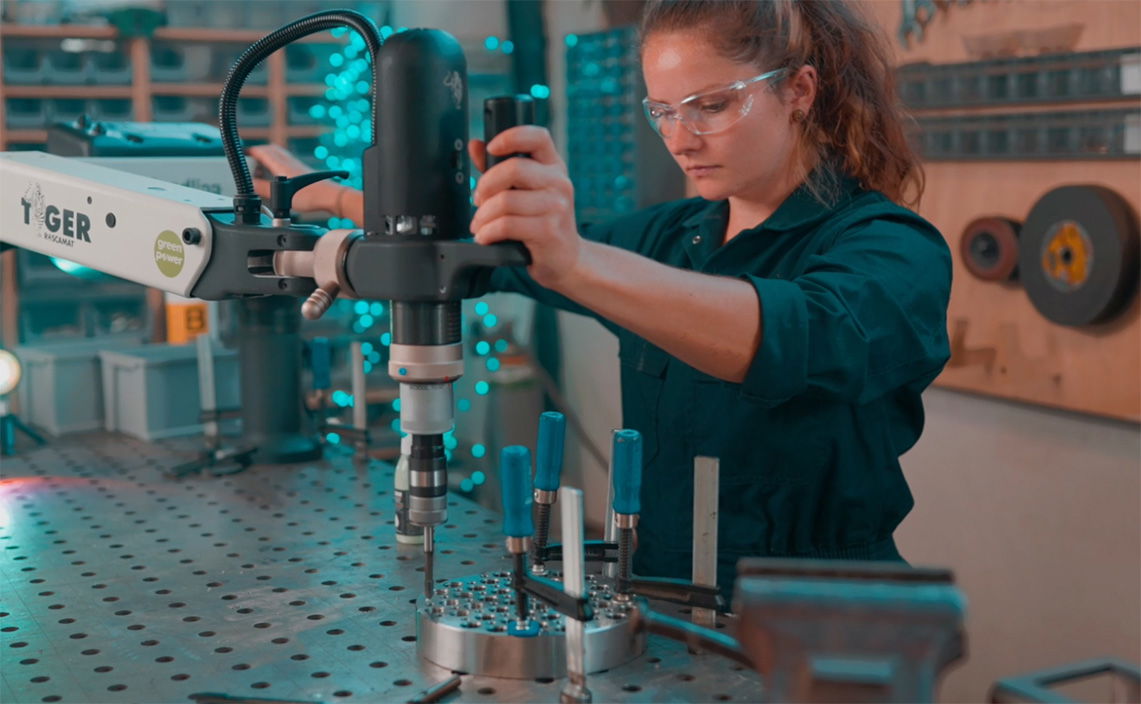
Cutting threads - avoid mistakes & work safely
Thread cutting may be a challenging task, but with a little knowledge and plenty of care, even beginners can venture into this technique. The care is in your hands, but when it comes to the necessary background knowledge, the BAER team is always here to assist you. So, read on for a compact summary of everything you need to know about thread cutting.
These tools are needed for thread cutting
To cut an internal thread, you'll need a set of tools. You might already have some of them at home, but it's best to source the rest from a reputable manufacturer with good reviews.
You should have the following tools ready:
- Twist drill bits
- Countersinks
- Screw taps
- Suitable Operating tool or a drilling machine
The three steps to cut a thread
Cutting a thread is accomplished in just three steps. It takes a bit longer if you intend to cut the thread manually. More on that in a moment.
1. Pre-drill the core hole with a twist drill bit.
2. Chamfer the core hole with a countersink.
3. Create the internal thread with the screw tap.
What to pay special attention to when cutting a thread
Sounded pretty straightforward so far? Of course, there are a few additional things to consider.
Thread cutting by hand or machine?
The first and most important decision is: Do you want to cut the thread by hand or machine? For manual thread cutting, you'll need a set of special hand taps, consisting of two or three tools. The internal thread is then cut in multiple passes. For manual thread cutting, you'll also need an adjustable tap wrench or a tool holder with ratchet as an operating tool.
If you want to use a stationary drilling machine (or possibly a hand drilling machine) to cut a thread, then you should use a machine tap. It will complete the tapping in a single pass. Of course, you'll need a suitable drilling machine for this.
Ensure the correct core hole diameter
Cutting a thread always starts with drilling the core hole. The diameter must be an exact fit since the receiving bore is not enlarged during thread cutting. The correct diameter can be calculated easily, at least for thread standards with a flank angle of 60°. This covers the metric coarse and fine threads, the most commonly used standards in Europe. The formula for most of your projects is: Thread diameter (D) - Pitch (P) = Core hole diameter (Dk).
If you're not a fan of calculations, we have good news – you can easily read these values from a table!
Use the appropriate tool
Manual and machine aren't the only attributes to consider when choosing a tool for cutting a thread. Screw taps also differ in their geometry and material composition. The cutting edge shape is particularly important, determining whether tapping in blind or through holes is possible, how deep the thread can be, and the materials you can work on. Some materials require tools with special coatings and specific materials. Read the product descriptions carefully!
Don't forget the lubricant
A significant amount of friction energy is generated during thread cutting. This can quickly become a problem, causing damage or deformation to the thread and the tool. You can prevent this by using a good Lubricant – especially when tapping with a machine, as high speeds generate more friction. Pay attention to a high-quality product and don't be too thrifty with its application.
Set up your stationary drilling machine correctly
This step is only necessary if you opt for machine thread cutting, but it's crucial! Relevant settings include cutting speed, RPM, and feed, which can be calculated as follows:
- Cutting speed vc [m/min] = (Outer diameter * π * RPM) / 1000
- RPM n [1/min] = (Cutting speed in m/min * 1000) / (Outer diameter * π)
- Feed programming [mm/min] = RPM * Pitch
On many smaller pillar and bench drilling machines, you'll manually control the feed using a wheel or lever. In this case, you must work meticulously to avoid issues during thread cutting.
Common errors in thread cutting and how to avoid them
As a long-time screw tap manufacturer, we know exactly where issues tend to arise repeatedly. Therefore, we'd like to point out the most common problems reported by customers and identify potential sources of error. This way, you can avoid difficulties before they occur.
The thread doesn't have the right dimensions
While thread cutting may have worked, upon testing, you find that the thread is too large? This could have various causes. Check whether you used the correct tapping tool. Is it the right size, suitable for the material, and not damaged or worn? The core hole may also have an incorrect size, or it may have been compromised due to angular or positional errors.
The thread surface becomes rough
If you notice that the surface of your thread isn't smooth, it's often related to the lubricant. Did you use enough cutting paste when cutting the thread or perhaps forgot to use it entirely? Another cause could be using the wrong tool. Rough thread surfaces during thread cutting also frequently occur when the cutting speed was too high or when chip problems arose.
The tool breaks or gets damaged
It's especially frustrating if the tool breaks during thread cutting. Not only is the screw tap no longer salvageable, but it can also be very challenging to remove the fragments from the thread. To prevent this, always ensure smooth chip removal. A too small or skewed core hole can be the cause of this problem. In the case of blind holes, there's always a risk if the thread tap hits the bottom of the hole.
Still have questions about "thread cutting"? Feel free to contact the BAER customer service. In our online shop, you'll find everything you need for thread cutting – from screw taps and twist drill bits to adjustable tap wrenches.