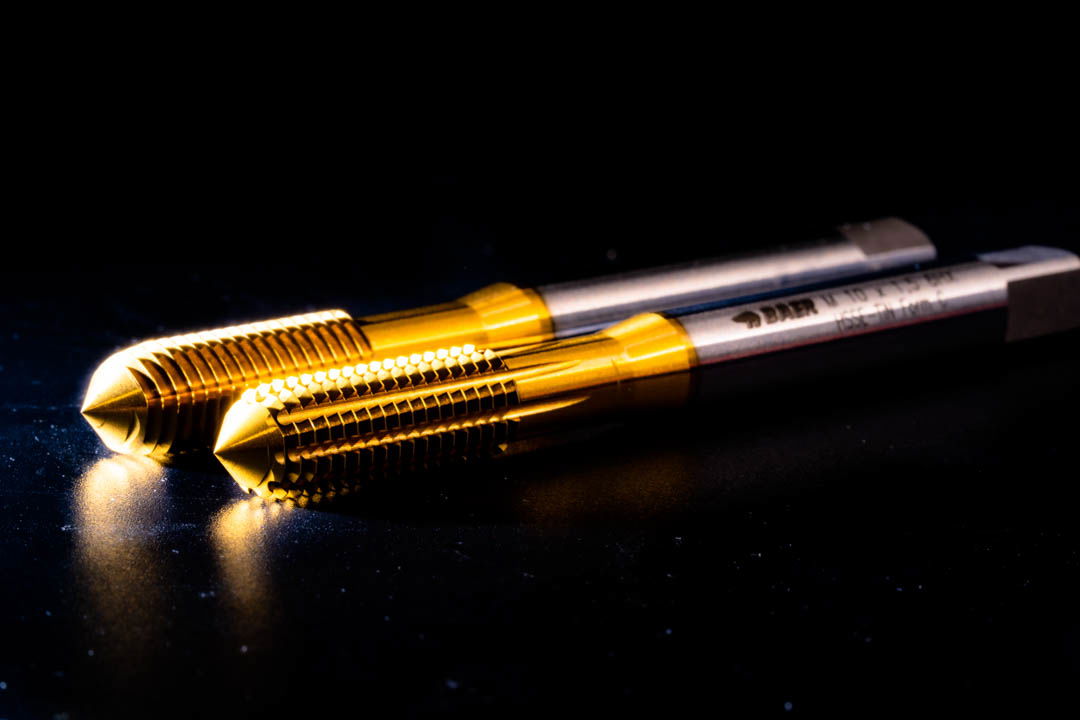
Thread forming: Producing threads without chip removal
If you want to produce a thread, you'll first face the decision of which method to use. Tapping is not the only procedure, even if in many cases it's the best choice. You also have the option to mill, roll, turn – or form a thread. In this blog post, we want to delve deeper into the last method. To make an informed decision, you should understand the distinct characteristics of each threading method, where they can be applied, and their pros and cons.
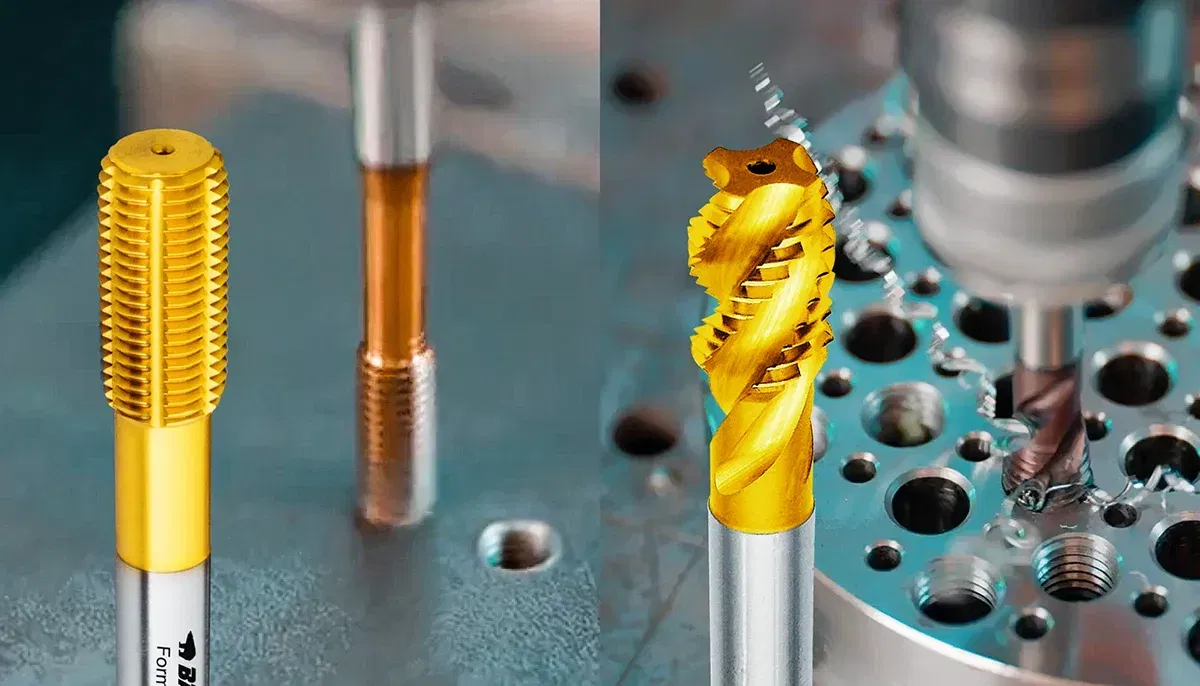
What is a thread forming tap?
Forming or rolling threads is a chipless method of thread production. This means that in this process, the thread isn't cut from the material. As a result, no material is removed, and no chips are produced. But how is the thread created then?
The thread forming tap displaces material when forming the thread, effectively pressing the thread shape into the surrounding material. The process is often referred to as cold forming, as it takes place below the recrystallization temperature. This allows for a higher pull-out strength.
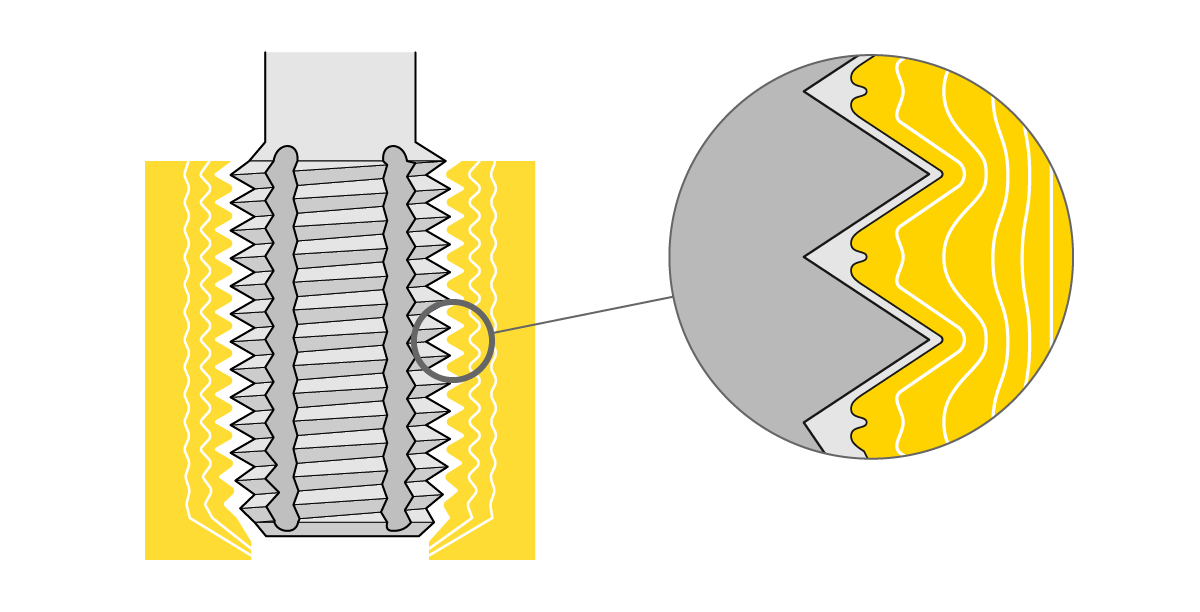
Forming or cutting threads – What's the difference?
Let's approach thread forming by comparing it with the threading method most are familiar with: thread cutting.
The two tools, screw taps and thread forming taps, can be distinguished at first glance despite some similarities. The thread forming tap doesn't have cutting edges and has a polygonal fotm. It doesn't necessarily need flutes, as no chips are produced that need to be transported away. However, some thread forming taps have oil grooves for better distribution of lubricant. Instead of a chamfer, you'll find a forming cone when forming threads. The thread teeth are fully formed from the start, only increasing in diameter.
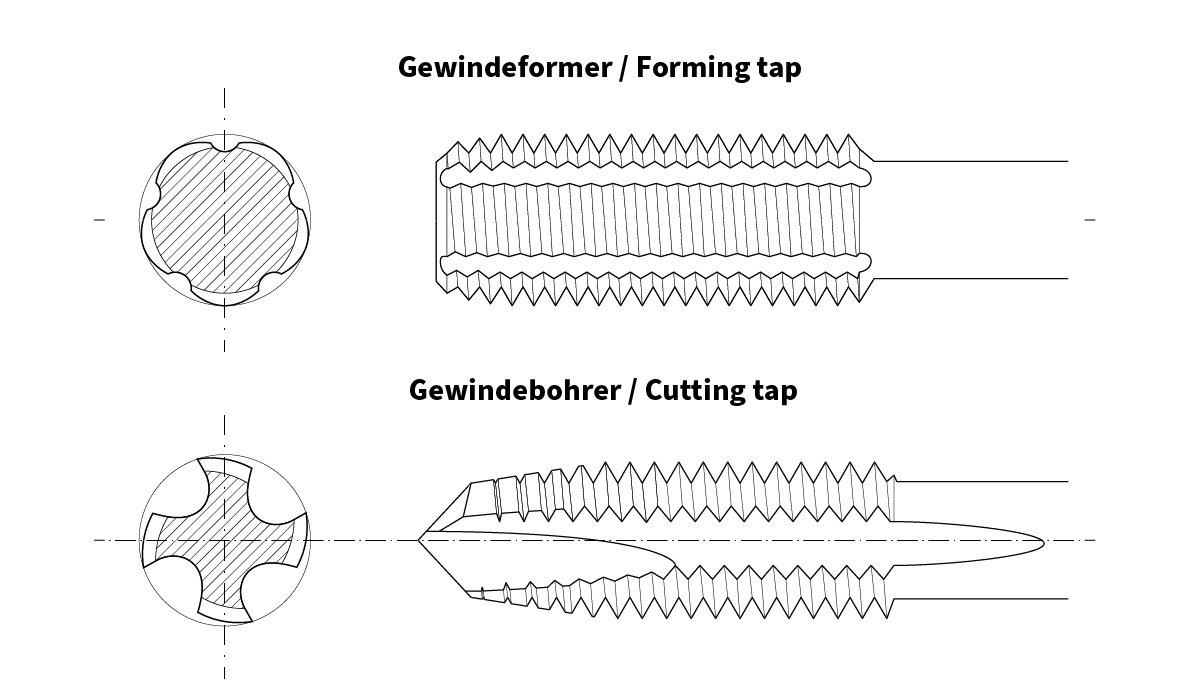
Even the thread itself can be identified as formed upon closer inspection. When forming threads, small hollows, often referred to as claws, form at the thread tips. However, the primary differences occur within the material itself. Unlike cutting, thread forming does not sever the material fibers but merely compresses them. This maintains the continuity of the fiber flow.
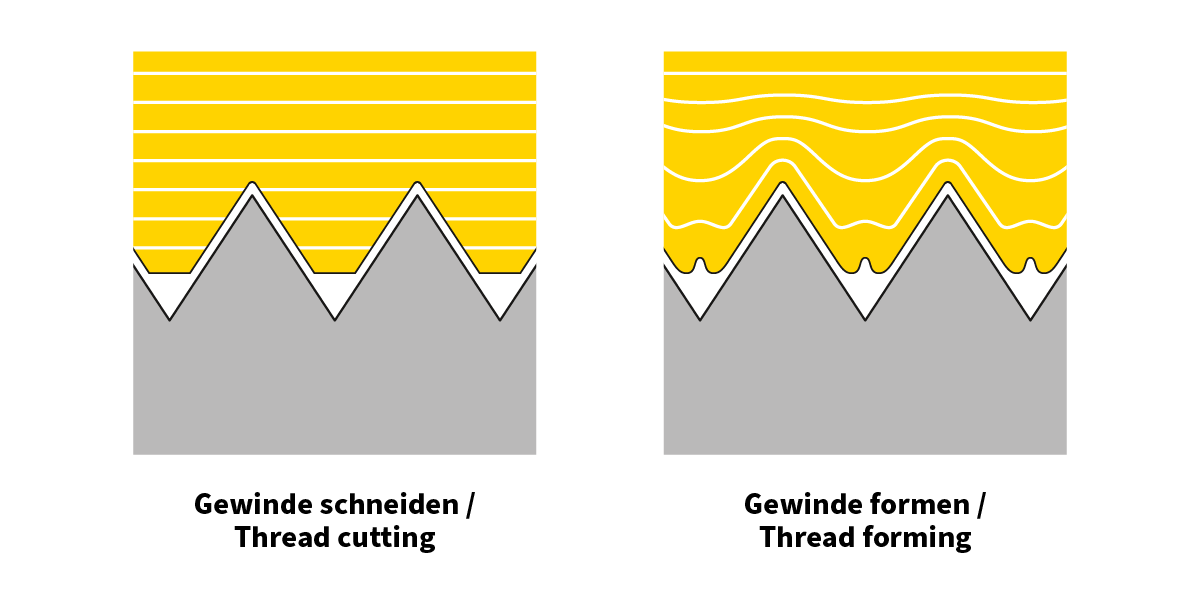
Good news regarding the maximum thread depth: it's larger when forming threads compared to machining methods and is only limited by the tool's length, provided you ensure sufficient lubrication. Also, the possible circumferential speed is higher with thread forming than with machining methods. For lubrication, however, you must pay special attention to the adequate and professional use of cooling lubricants due to the high friction forces generated.
The torque is also higher than with thread cutting, with the specific increase depending on various factors such as diameter, material, pitch, lubrication, and coating.
Applications for thread forming
As we've seen, thread forming has significant advantages. To benefit from them, however, you must know where and when you can apply thread forming. After all, not every situation is suitable for this method.
The main limitations lie in the material. It must be highly formable at cold temperatures, or else you won't achieve usable results with a thread forming tap. Suitable materials include light metals and their alloys, nickel and cobalt alloys, titanium and its alloys, non-ferrous metals, steels up to about 1200 N/mm2, and rust, acid, and/or heat-resistant steels up to 1200 N/mm2. For all other materials, you'll likely need to resort to other threading methods.
The pitch is another factor that limits the application of thread forming taps. Very high pitches can't be achieved through thread forming. Depending on the material, you can expect maximum achievable pitches of about 3 to 4 mm. If you need a higher value, then thread forming is not the right method.
Things to consider when forming threads
In thread forming, you must first observe the correct core hole diameter . This is calculated differently than in thread cutting. The core hole for the thread former is larger compared to the screw tap, but the tolerance is smaller. The formula for calculation is: Dk = D – (0.5 x P) + 0.05. Dk represents the core hole diameter, D the thread's nominal diameter, and P the pitch. Alternatively, you can also read the values from an appropriate table.
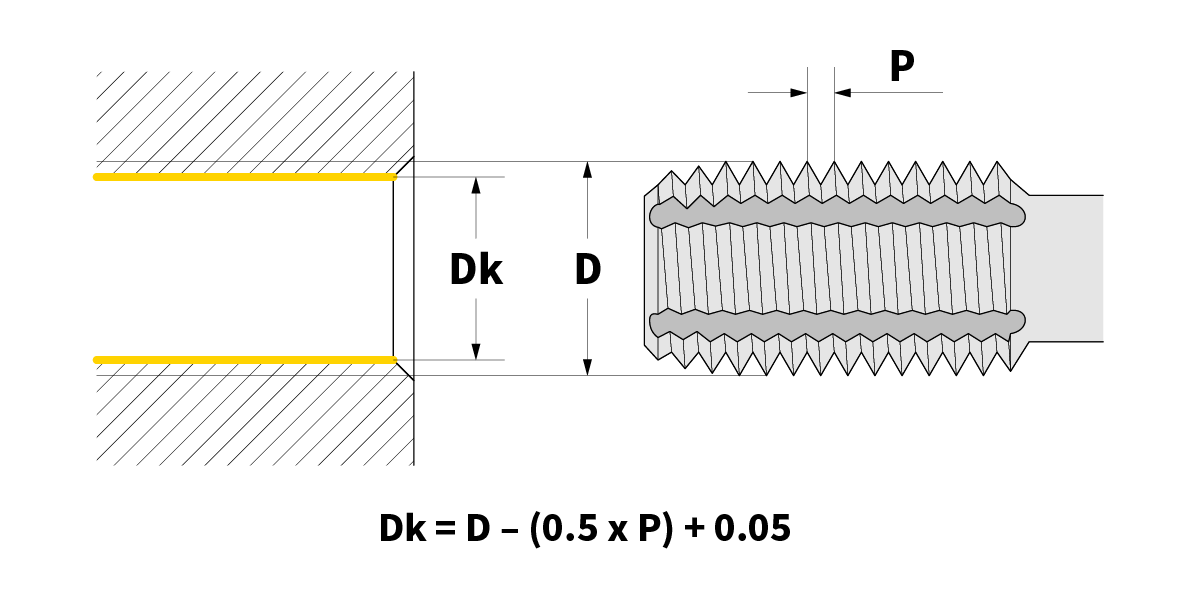
Another distinctive feature is the very high frictional forces released during the forming process. More than with thread cutting, the right use of lubricant is essential for success. The lubricant used should be tailored to the material and be of very high quality. Oil grooves or an internal lubricant supply can further facilitate proper lubrication during thread forming.
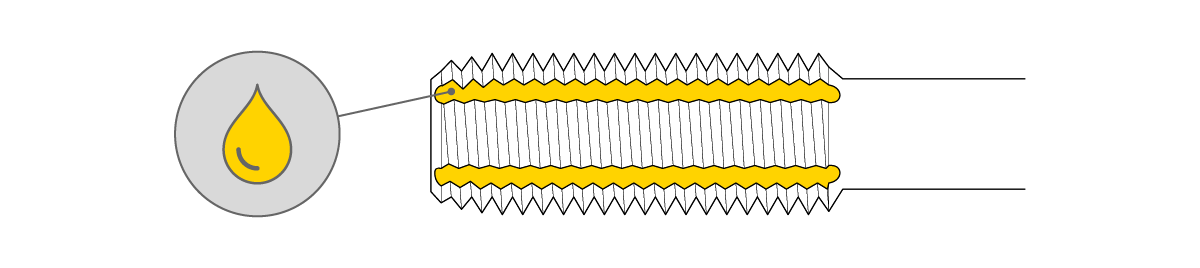
Pros and cons of thread forming
The benefits of thread forming are numerous. Notably, no chips are produced, so chip-related issues are eliminated. Threads produced also have particularly high pull-out strength. The thread forming tap is suitable for very deep threads and has a longer lifetime than a tap. Threads produced also have a very high surface quality due to forming.
On the downside, the limited application range is notable. You'll only enjoy the benefits if you use a material from a restricted selection. For many materials, you'll need to revert to other threading methods. Additionally, thread forming generates very high friction forces leading to a significant increase in heat. This demands high-quality cooling lubricants and their correct application. Also, the tight borehole tolerances require particularly careful work. Lastly, a thread forming tap is not usable as a hand tool, meaning you can only use it if you have the appropriate workshop equipment.
You can find thread forming taps and suitable cutting oils in the online shop of tap manufacturer BAER. Feel free to browse! If you have questions or suggestions, our friendly customer service staff are always ready to help.