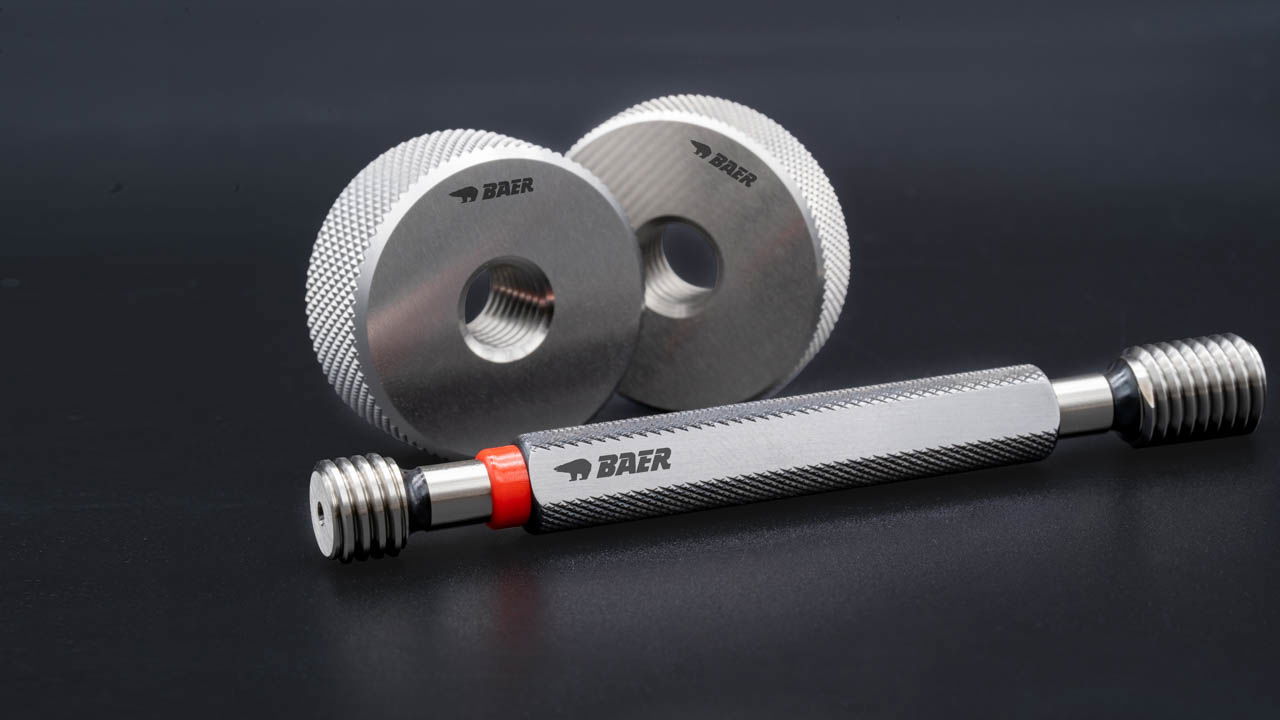
Gauge Capability – What does it actually mean?
Standards are designed to ensure the interchangeability of workpieces. However, standards only work if they are adhered to. Whether a thread is true to gauge, meaning it lies within the prescribed tolerances, can be conveniently determined using a thread gauge. Such a test is especially meaningful in the professional field, as faulty tools can cause significant damage. But even DIY enthusiasts should keep an eye out to ensure their threads are true to gauge. After all, load capacity and interchangeability are relevant topics even for home use. Let's look at why gauge-compliant threads are important and how you can check them yourself.
Gauging is not measuring
You might now be picturing a caliper or another indicating measuring instrument with which you try to determine the exact dimensions of your thread. In fact, gauging and measuring are not interchangeable terms, even if they are sometimes used as such in everyday language. Because thread gauge compliance does not describe a value. Instead, it checks whether the actual size of the thread lies within the set limits. Then the thread is true to gauge.
This difference in gauge compliance is particularly important for manufacturers because only the DIN standard gauge system creates legal certainty. If there is a conflict with a customer about whether a thread is true to gauge, the result of the gauge is decisive. Therefore, in manufacturing, random checks should always ensure that a thread is true to gauge.
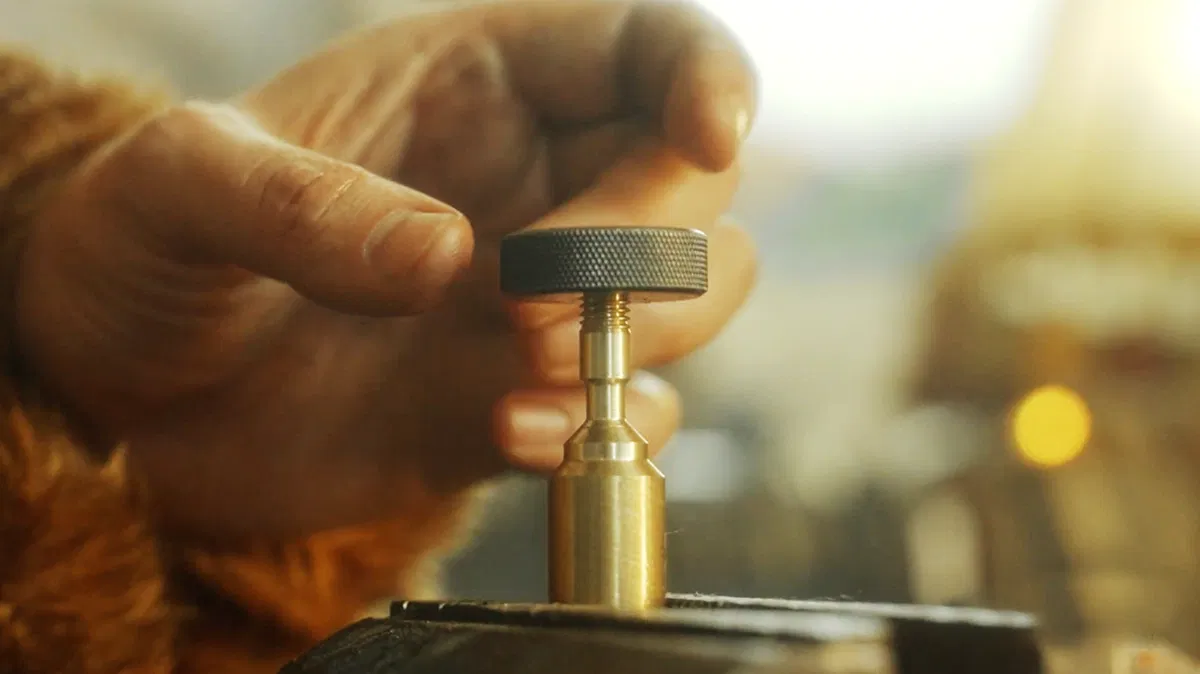
The importance of gauge compliance
A thread is a complex structure. The values established in the corresponding standards, such as diameter, pitch, and flank angle, are precisely coordinated and calculated to guarantee optimal load-bearing capacity and smooth operation of the threaded connection. A small inaccuracy in thread gauge compliance can quickly disrupt this balance. The result is a range of potential problems, from defective tools, frustration and delays due to poorly fitting or damaged components, to real safety risks. For this reason, it is essential that the thread is true to gauge.
Using these tools to determine if a thread is true to gauge
You check whether a thread is true to gauge using so-called thread gauges. They have the advantage of providing a clear result regarding gauge compliance, without the need to read measurement values. That eliminates one source of error.
You always use thread gauges to measure gauge compliance in pairs. After all, no measurement value is determined, but only the statement is made whether the thread dimensions are within the specified tolerances. This must be determined in both directions, meaning even if the thread isn't too small, it could still be too large. You approach the question of whether the thread is true to gauge from both ends of the spectrum. The difference: An internal thread that's too small can still be reworked, while one that's too large is automatically rejected. For the external thread, it's the other way around. Therefore, during the gauge compliance check, the terms "good" and "reject" are used.
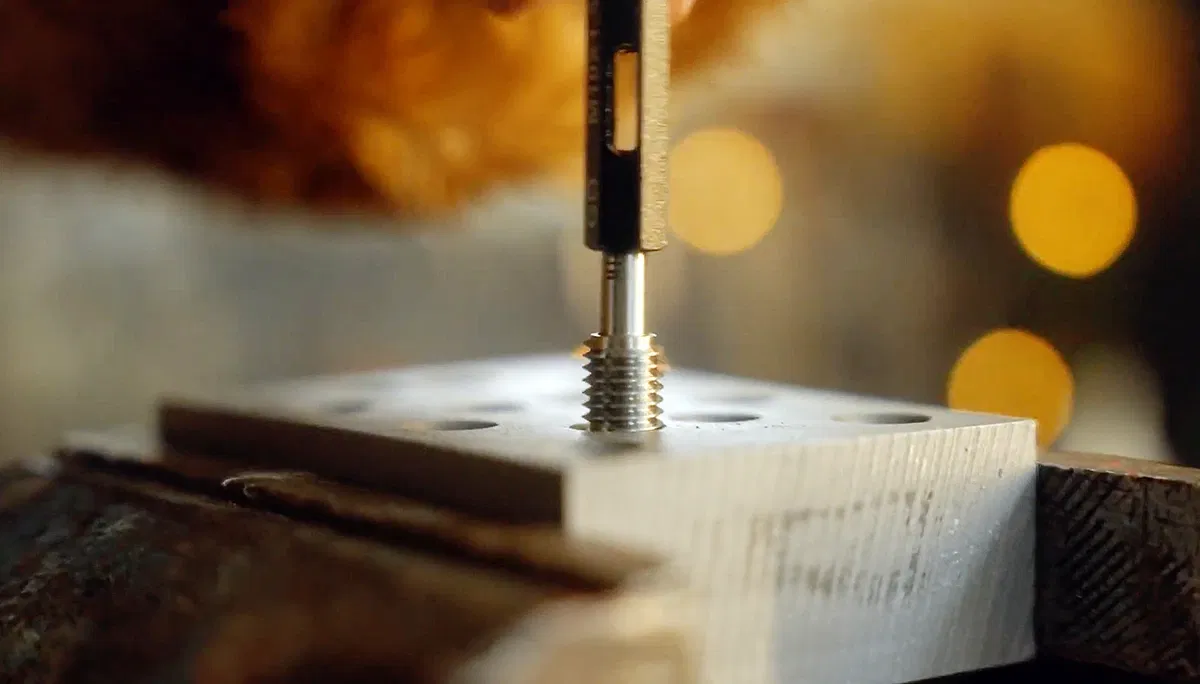
Determining the gauge compliance of internal threads with thread plug gauges
For the correct determination of the gauge compliance of an internal thread, you need two tools: the Go thread plug gauge and its counterpart, the No-Go thread plug gauge. The latter can be distinguished at first glance by its red marking. For smaller thread diameters up to 40 mm, both tools are mounted on a common handle for simplicity. In this case, it is referred to as a limit thread plug gauge. Here too, the No-Go side of the thread plug gauge is marked in red.
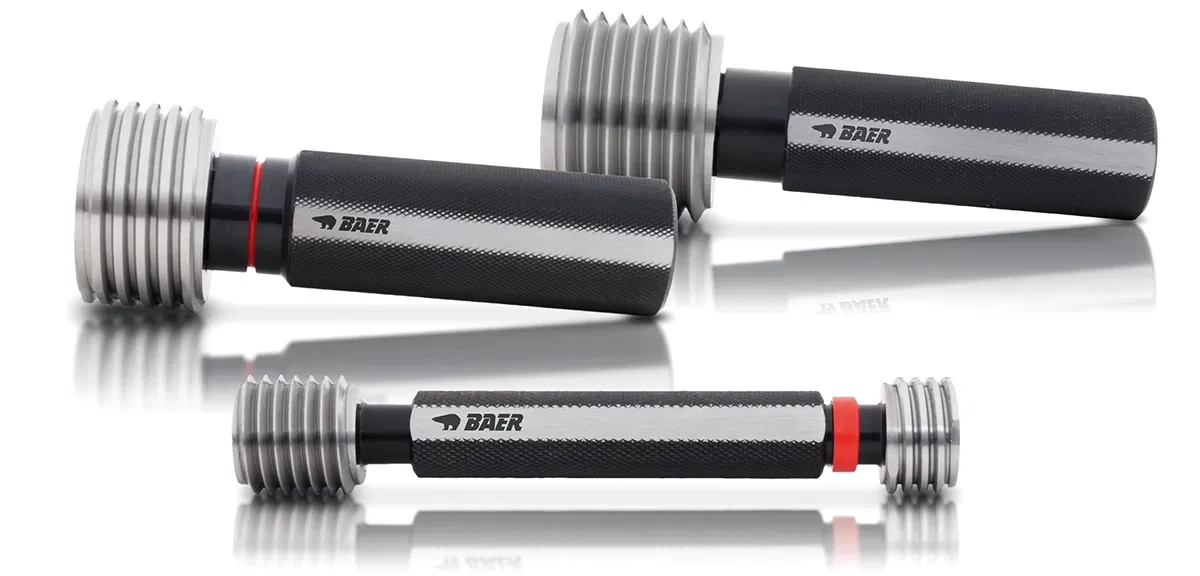
The Go thread plug gauge checks the minimum pitch diameter and various form deviations, e.g., the pitch and thread profile angle, to measure gauge compliance. It must be able to be screwed without force over the entire length of the thread. The No-Go thread plug gauge checks the actual pitch diameter and should not be screwed more than two turns into the thread. Only then the thread can be true to gauge.
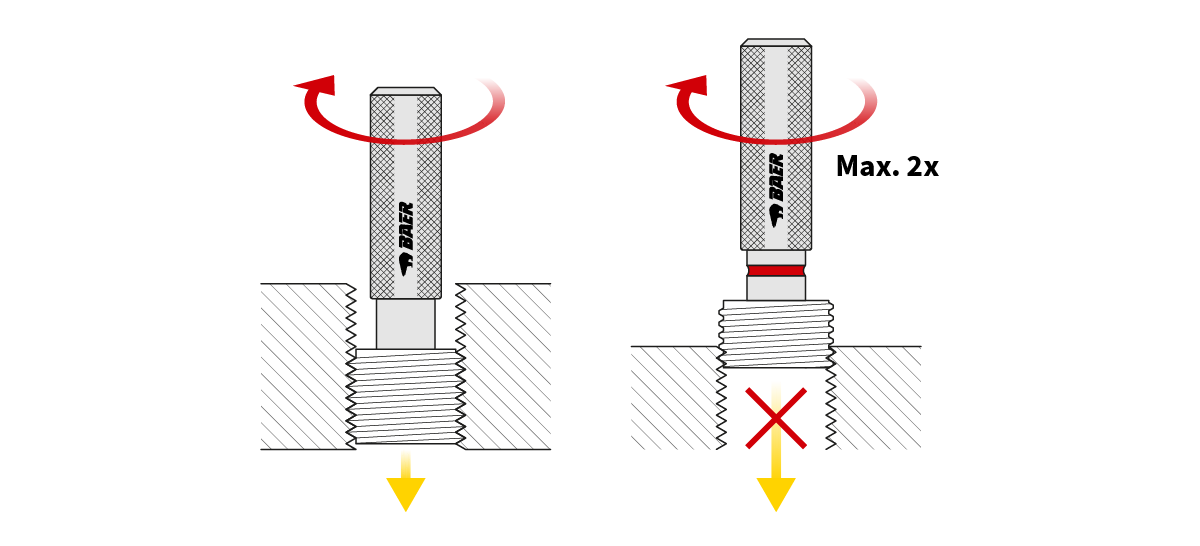
Determining the gauge compliance of external threads with thread ring gauges
External threads are gauged with a thread ring gauge. Here again, there are two tools: the Go thread ring gauge and its counterpart, the No-Go thread ring gauge. A red marking again easily distinguishes them.
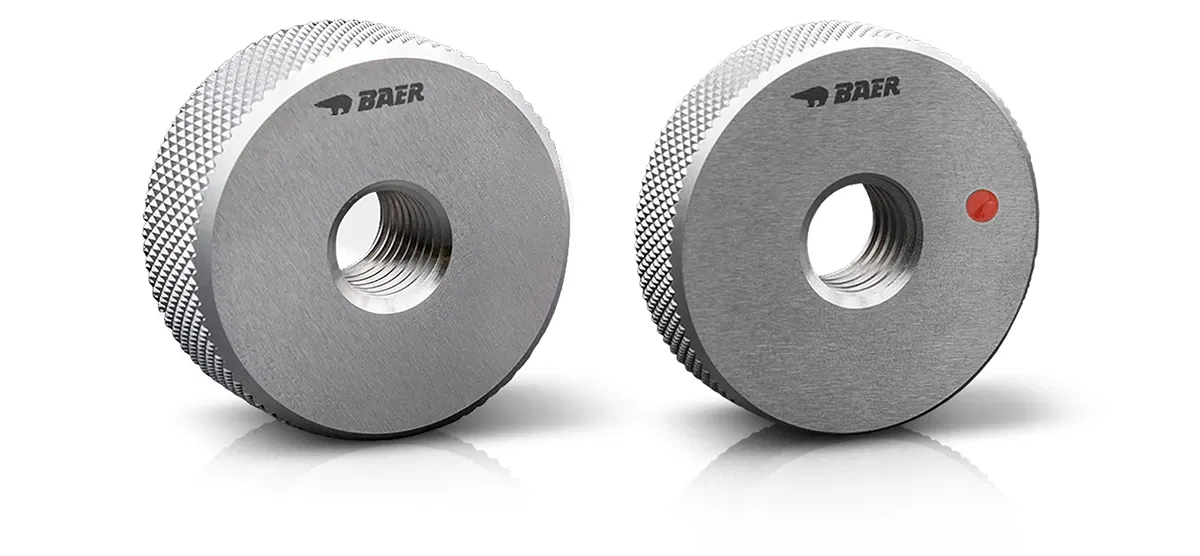
The Go thread ring gauge checks the maximum pitch diameter, form deviations in pitch and thread profile angle, and also checks the straight flank section for sufficient length. For this, the thread ring gauge must be able to screw easily by hand over the entire length onto the thread. The No-Go thread ring gauge checks the actual pitch diameter of the thread and should not screw more than two thread turns. If this is the case, the thread is said to comply with the gauge.
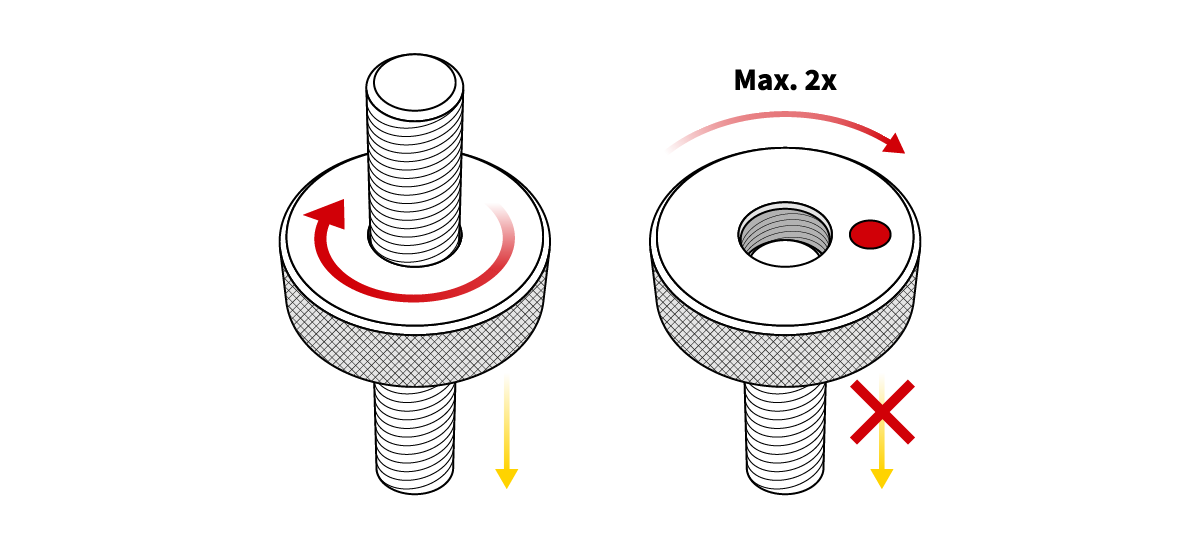
Three quick tips for using thread gauges
- Ensure that the workpiece and gauge have roughly room temperature.
- The thread must be clean and free of lubricant residues.
- Do not apply any force, as this can skew the results.
Calibration of thread gauges
When you research thread gauges and gauge compliance on the internet, you will frequently encounter the term calibration. This term refers to determining the deviation of a measuring instrument's display from the true value. For this purpose, the results obtained from a test device are compared with those of a reference device to determine how much they differ. So if you buy a calibrated thread plug gauge, you will receive a certificate with it, from which you can read the result of the calibration. This lets you see if there's a deviation and how significant this deviation is. The calibration certificate also contains information about the exact circumstances of the calibration, the calibration uncertainty, and more.
Calibration is not only useful for new tools. You can also use it to determine if a thread gauge that you have been using for a longer period is still reliably checking for gauge compliance. Only then can you be sure that the tested thread is true to gauge.
Why should I use high-quality threading tools that comply with the gauge?
The easiest way to cut standard-compliant threads is to use good screw taps. When purchasing, look for high-quality tools from experienced manufacturers. Because here, all guidelines are adhered to during production, and the gauge compliance of the tools is regularly checked. This way, you always cut a thread that is true to gauge, precise, and stable.
In the online shop of screw tap manufacturer BAER, you will not only find quality screw taps, but also thread gauges that allow you to easily check whether your thread is true to gauge!