
Thread cutting with the machine - How to do it successfully!
One of the great things about thread cutting is its accessibility for amateurs and beginners. With the right tap, you can cut a thread by hand even in your home garage, without the need for a fully-equipped workshop. However, this method is not particularly efficient. If you often need to cut threads, you are probably interested in understanding how thread cutting with machines works. In this blog post, we'll explain the basics and address a few common misconceptions about machine-based thread cutting.
Which machines are suitable for machine taps?
First, we need to clarify what we mean by the term "machine tap". Yes, your cordless drill is technically a machine, but it's not the one meant for thread cutting with a machine.
Machine-based thread cutting is a highly sensitive process where human error should play as minimal a role as possible. When you use a handheld drill or cordless screwdriver, you have many factors literally in your hand. If you don't hold the device perfectly straight, the thread might not be cut correctly, and the tool can easily break. Even a manually operated pillar drill only partially solves the problem because you still manually control the feed. Not to mention that for machine-based thread cutting, it's best to use a thread-cutting chuck.
If you do decide to use a pillar drilling machine, consider investing in one with an automatic dip-to-slope program or use a thread cutting device specifically designed for machine-based thread cutting. If you somehow need to use a handheld device, we recommend setting it to the lowest speed and using a machine tap with a long lead (e.g., Form B) for additional guidance. However, please note that this is just a makeshift solution, and machine taps are explicitly not designed for this. If you have to cut many threads, you should consider whether purchasing a machine with a thread cutting program or a thread cutting device would be a worthwhile investment!
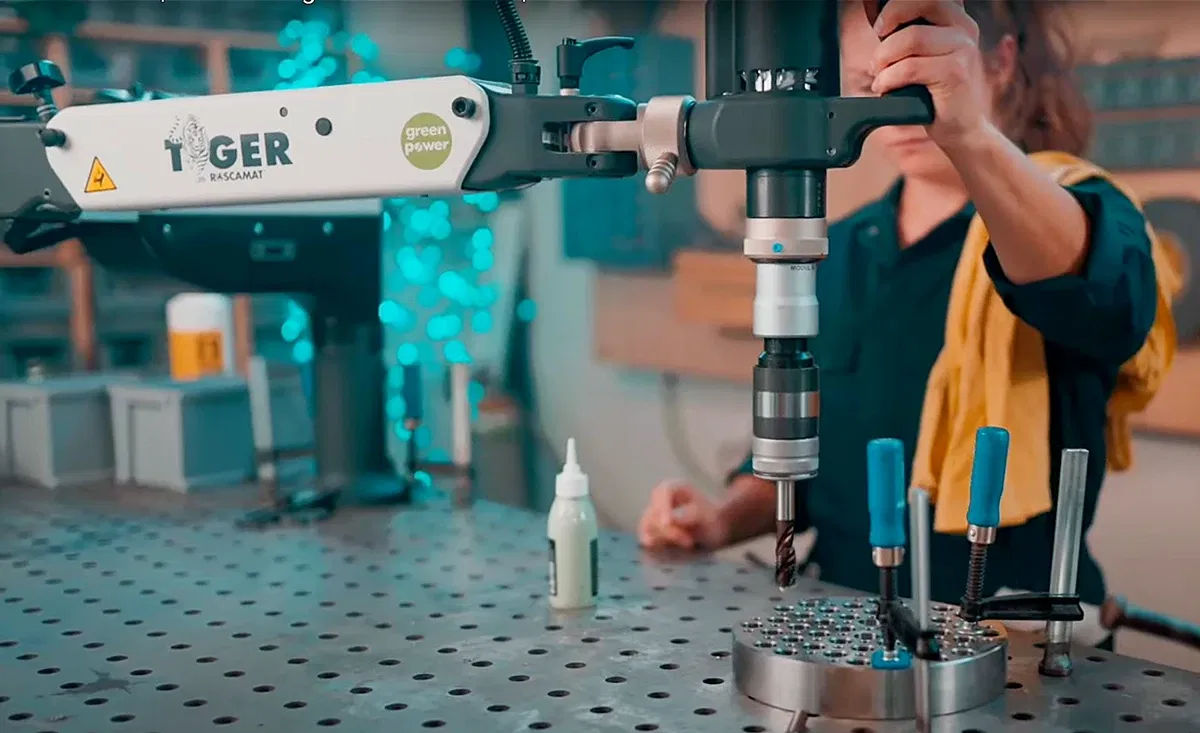
How machine-based thread cutting works
Do you have a suitable tool machine for thread cutting? Great, then you can almost get started. However, there are a few things to keep in mind.
These are the tools you'll need for machine-based thread cutting
Obviously, the most crucial tool is the machine tap itself. Various types differ mainly in the shape of the lead and the material used. To make the right choice, you should know the intended use of the machine tap and the material you'll be working with.
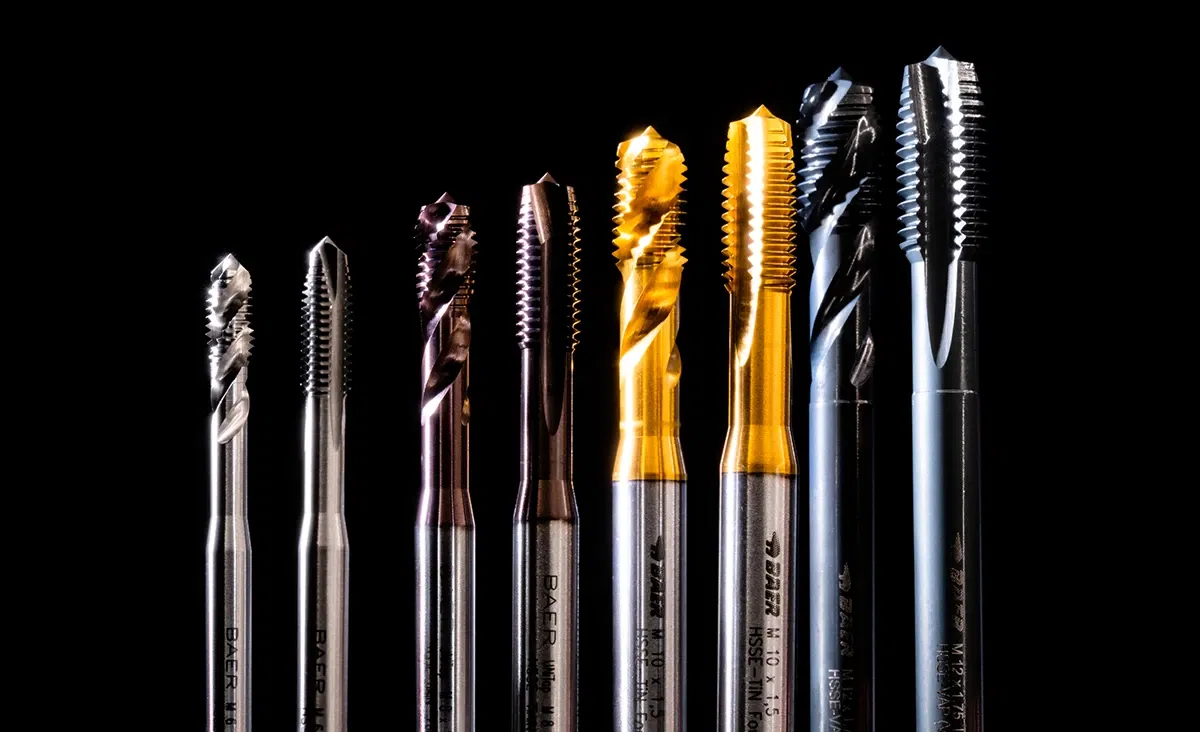
Additionally, you'll need a suitable tool holder for machine-based thread cutting. Its job is to connect your machine tap to the machine tool. What you use depends on the type of machine and your equipment. Frequently used are collets with square receptacles that also transmit torque. For smaller thread dimensions, a cylindrical collet may suffice. Thread cutting devices also count as tool holders. Specialists in this area are tapping heads, capable of compensating for minor irregularities during machine-based thread cutting, thus significantly extending tool life.
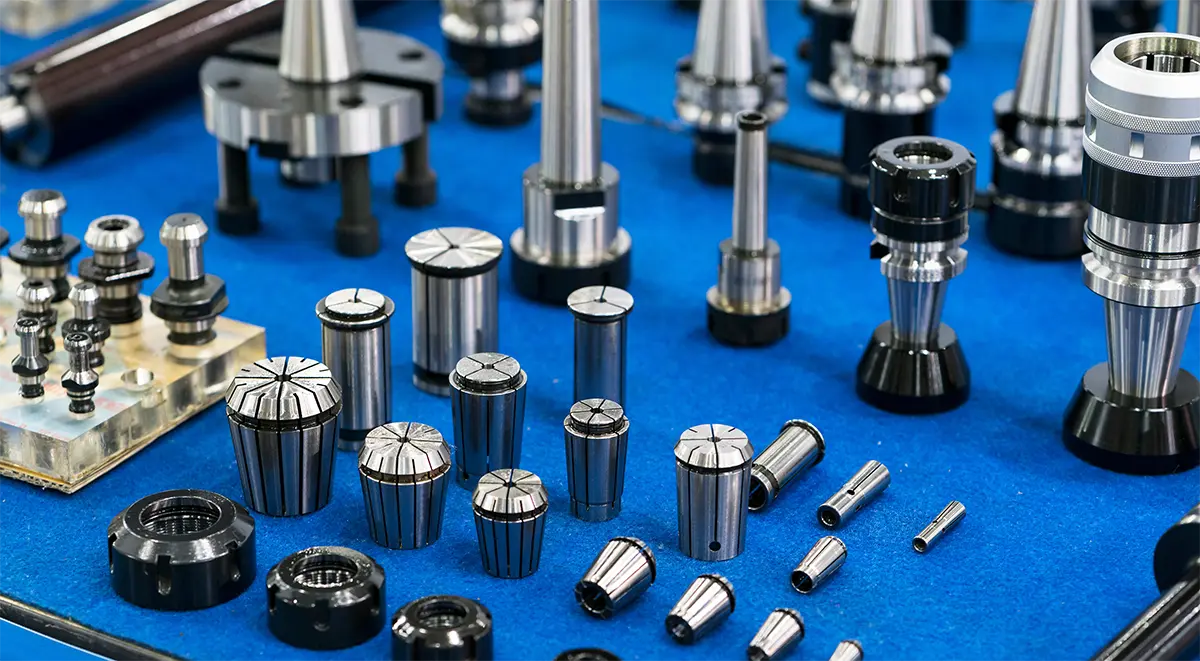
Lastly, you'll need tools to prepare the core hole drilling: drill bits and countersinks.
Step-by-step guide to machine-based thread cutting
- 1. Pre-drill the core hole: The tap can only work in a prepared hole. Use an ordinary twist drill bit for this. Ensure the correct diameter! Learn all about it here.
- 2. Countersink the core hole: We recommend chamfering the edges of the core hole with a countersink afterwards. This helps with centering and ensures a clean finish.
- 3. Cut the thread: Now it's the machine tap's turn. Ensure the correct settings (feed according to pitch per rotation) and use plenty of lubricant!
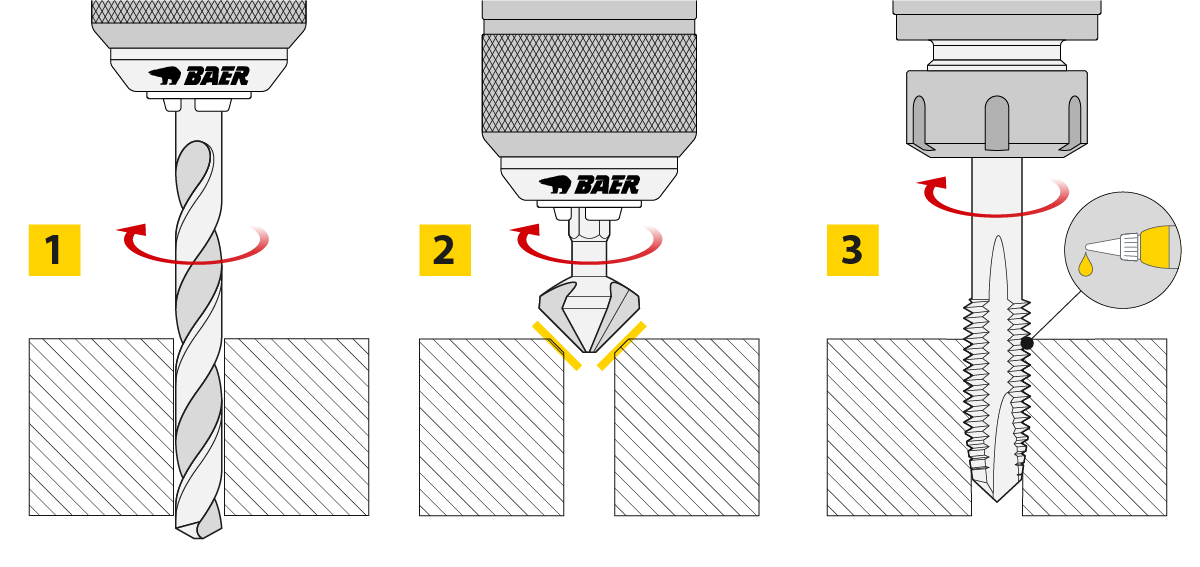
Finding the right settings for machine-based thread cutting
As we've seen, thread cutting works best when you select the appropriate program beforehand and let the machine do the rest. However, this also means you need to know the necessary programming for machine-based thread cutting. An important value is the feed, i.e., the distance the machine tap moves into the material per rotation. The feed should correspond to the thread's pitch. Obtain the correct feed programming by multiplying the rotation speed by the pitch during thread cutting.
The cutting speed for machine-based thread cutting depends on the drill used and the material being processed. Recommendations can typically be found in the product description of the drill, e.g., in our BAER Online Shop. Values usually range between 5 and 15 m/min. We recommend starting at the minimum value or slightly below, then adjusting the speed based on the behavior of the drill. This information refers to computer-controlled machines, not manual devices.
An overview of the essential formulas for machine-based thread cutting:
- Cutting speed vc [m/min] = (outer diameter * π * speed) / 1000
- Rotation speed n [1/min] = (cutting speed in m/min * 1000) / (outer diameter * π)
- Feed programming [mm/min] = rotation speed * pitch
Ensure smooth operations: don't forget the coolant!
Unwanted friction arises during machine-based thread cutting, which you can counteract using lubricants. The higher the speed, the more critical this becomes, as more frictional energy is released, producing more heat.
But not all coolants are created equal. Again, recommended products depend on the application. Coolants are divided into solutions or dispersions, emulsions, and cutting oil. Various additives can also create additional properties, such as corrosion protection.
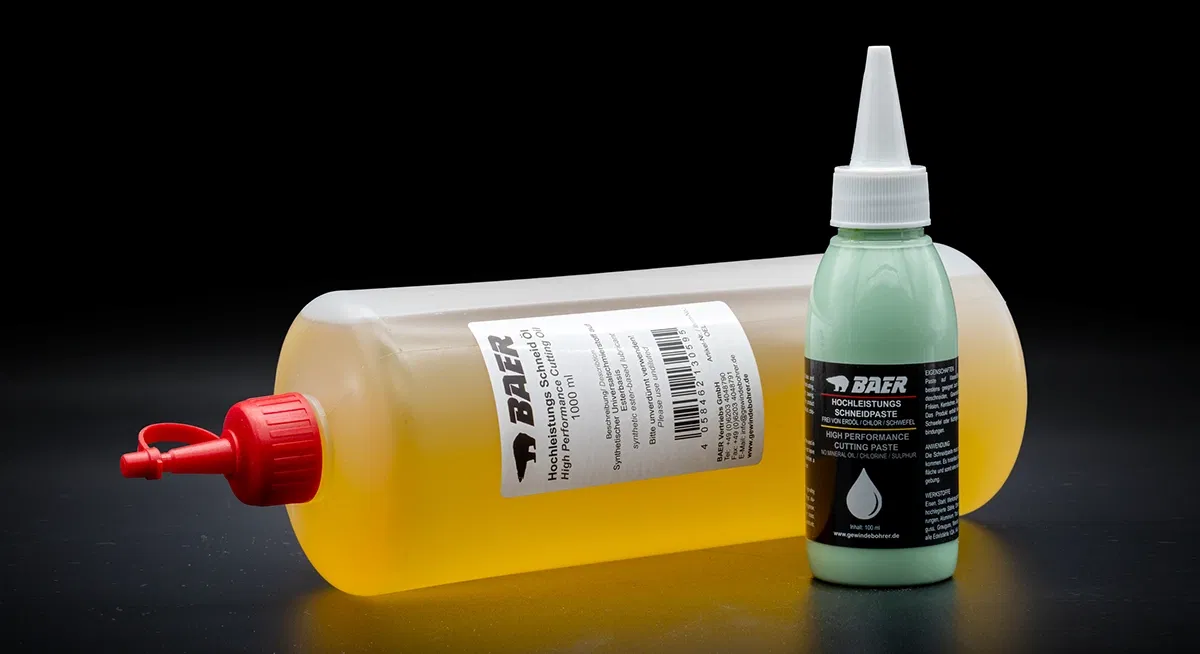
For machine-based thread cutting, lubrication is the focus, and coolants are typically used in the form of thread cutting oil or thread cutting paste. Many machines automatically supply coolant via external nozzles or an internal mechanism within the spindle during drilling. It's essential to use sufficient pressure to ensure an adequate amount of coolant is present.
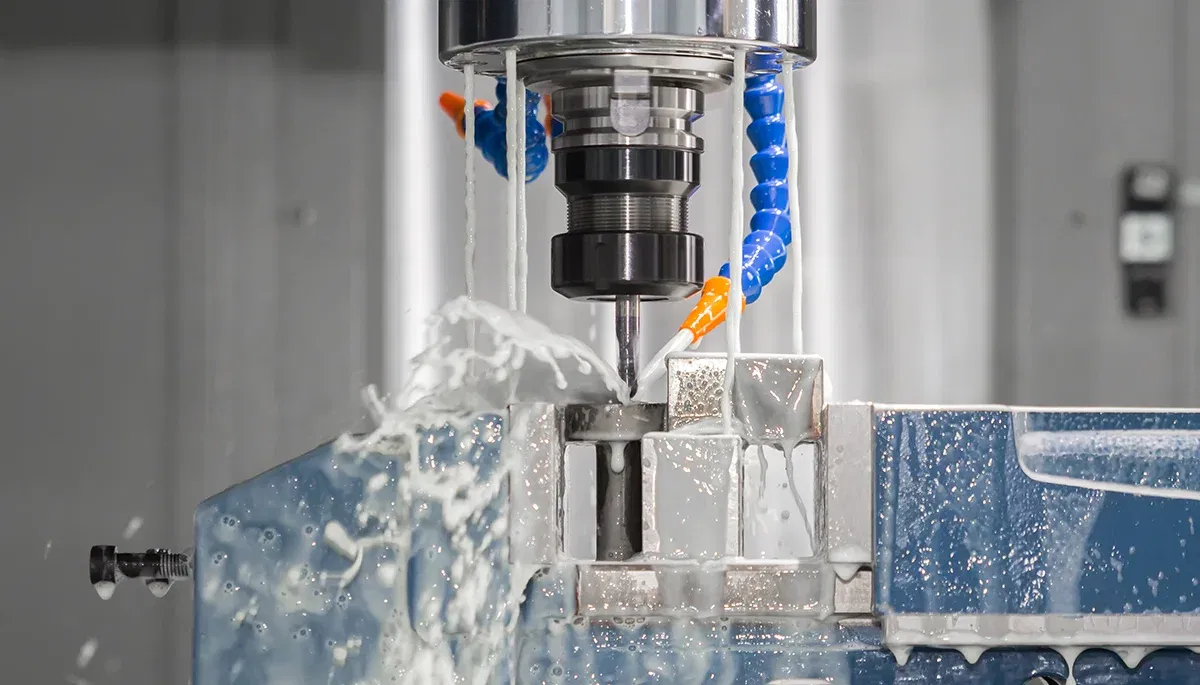
High-quality machine taps for machine-based thread cutting are available in the online shop of Tap Manufacturer BAER. Check it out!