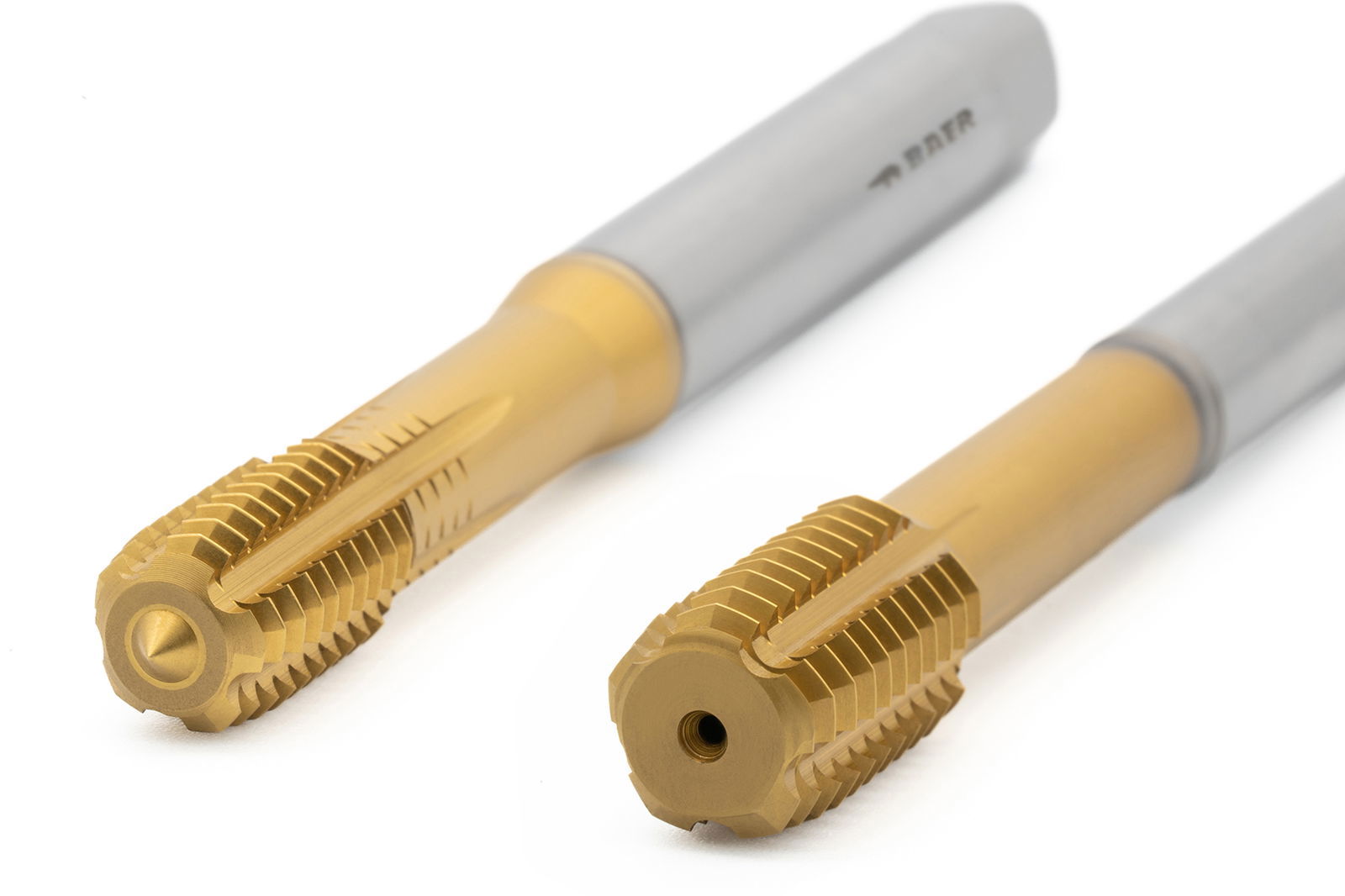
Forming threads - achieving a clean finish without chips
While thread cutting is particularly close to our hearts, it is not the only way to create a thread. In fact, there are various methods of production, each with its own unique features, advantages, and disadvantages. Your choice depends on many factors, such as the material used, the workshop equipment at your disposal, and your personal experience and preference. To make an informed decision, let's take a look beyond the horizon! Today, we are exploring a chipless method for thread generation, known as thread forming or thread rolling. Learn how it works, when to use this method, and what makes thread forming so special in this blog post.
How Does Thread Forming Work?
Thread forming creates threads without removing material, unlike thread cutting where material is cut. In thread forming, you displace the material rather than severing it. This process is often referred to as cold forming. Cold forming occurs when a shaping process takes place below the recrystallization temperature of the material, resulting in no changes on a molecular level in the crystal lattice. This leads to an increased material strength.
The Tool for Thread Forming
Thread forming requires a special tool, the thread forming tap or so called roll tap. When inserted into a prepared core hole, the thread forming tap pushes the thread into the material. The thread forming tap does not require flutes because no chips are produced during this process that need to be removed. Narrow grooves may be helpful for better distribution of coolant. Where a screw tap has a cutting edge, a toll tap has a pilot taper. All thread teeth are fully developed on the taper, increasing only in diameter. Furthermore, the forming tap has a polygonal profile rather than being round.
The Process of Thread Forming
The steps for thread forming are similar to those for cutting threads. First, you must create a core hole. Pay attention, as special dimensions apply to core holes for thread forming. You can further chamfer the core hole with a countersink . Once this is done, you can proceed with thread forming.
During thread forming, claw marks form at the thread tips, small voids that distinguish this manufacturing process. These marks do not affect the functionality of the thread.
The Core Hole Diameter for Thread Rolling
In thread rolling, the core diameter is larger than in thread drilling, but the tolerances are narrower. This means that you have less room for error when it comes to the diameter of the core hole. You can calculate the appropriate dimensions for thread rolling using this formula:
Dk = D – (0.5 x P) + 0.05
Where:
- Dk = Core hole diameter
- D = Thread major diameter
- P = Pitch
Due to the narrow tolerances, you should only perform the calculation yourself if you are confident in your skills. Otherwise, it's better to read the correct core hole diameter for thread forming from a table to avoid mistakes.
When Is Thread Forming Practical?
The thread forming method is only suitable for thread production when working with a material that is highly cold formable. This includes light metals and light metal alloys, nickel and cobalt alloys, titanium and titanium alloys, non-ferrous metals, steels up to about 1200 N/mm2, and corrosion-resistant, acid-resistant, and/or heat-resistant steels up to 1200 N/mm2. Other materials are not compatible with thread forming.
Material properties also set limits on pitch. The pitch in thread forming can be a maximum of 3 to 4 mm. However, the achievable thread depth is much greater than with machining tools and is only limited by the tool's length.
Thread forming also generates significant friction forces, leading to heat generation. Therefore, compared to other methods of thread generation, lubrication and cooling become even more critical. If you cannot ensure a constant supply of lubricant in sufficient quantity, thread forming is not a suitable method for you.
Furthermore, thread rolling works best when using a stationary machine tool. This method of thread generation is less suitable for manual work.
The Advantages of Thread Forming
Despite these limitations, thread forming also offers several advantages. One of the key benefits is that no chips are produced during thread rolling. This eliminates chip issues, which are one of the most common sources of errors in thread generation. With thread rolling, you do not need different tools for blind holes compared to through holes. Additionally, thread forming creates threads with exceptionally high strength and excellent surface quality due to cold forming.
Thread forming prevents the issue of axial misalignment that is a concern when cutting threads, which can potentially ruin the entire thread. Thread rolling allows for higher cutting speeds and longer tool life. Tools for thread forming are designed for extended use. However, it's important to note that unlike thread cutting tools , thread formers cannot be re-sharpened if they wear out.
Is Thread Forming Suitable for You?
If you are working with a compatible material and prefer to avoid chips, perhaps because you need to create threads in a blind hole, then thread formers are a viable alternative. However, you should be aware that thread forming has its challenges. To counteract the high friction forces, you require a substantial amount of high-quality lubricant. Precision is also crucial when creating the core hole for thread forming due to the tight tolerances. It's easy to make the hole too large or too small, which can result in an improperly formed thread or tool breakage.
Intrigued by thread forming? Feel free to visit the BAER online shop! As your screw tap manufacturer we offer a wide range of thread forming taps. You can reach out to our customer service through the contact form with any questions.