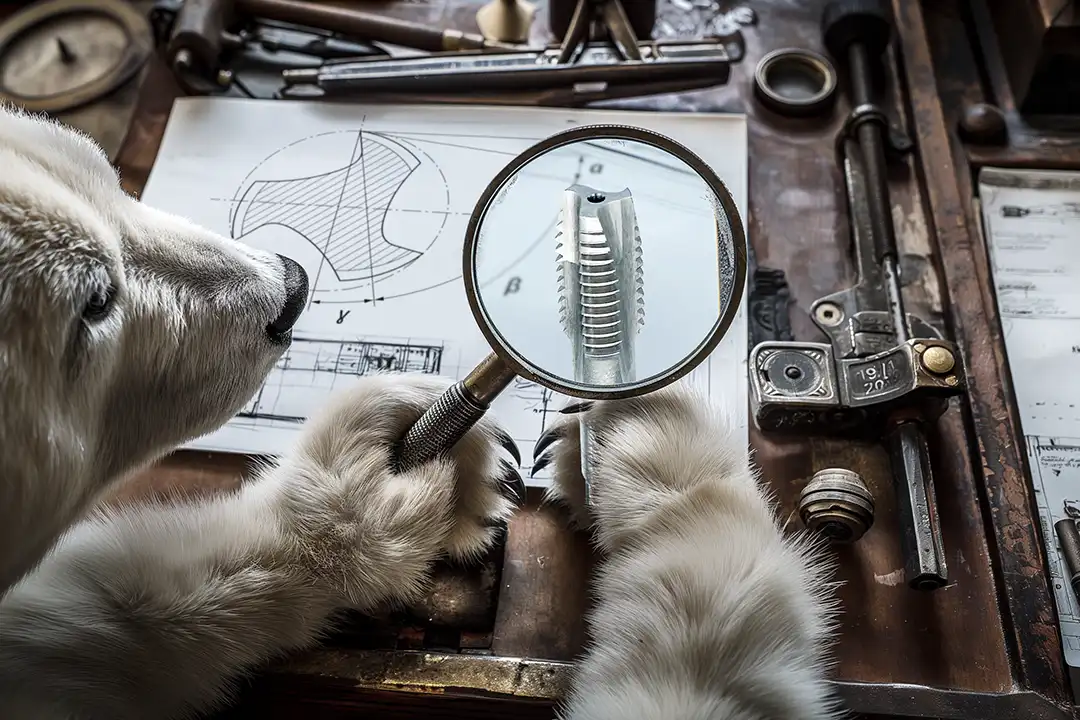
Everything you need to know about the relief angle on the tap
Do you really need to know every little thing about a thread profile to be able to cut good threads? No, of course not. Under normal circumstances, a few basics are enough and if you manage to select the right tap for your cutting application, then you have already done a lot right. So why do we keep going into detailed specialist knowledge that you don't necessarily need in everyday life? Because it can be worth its weight in gold at the crucial moment.
Specialist knowledge always pays off when you repeatedly stumble across the same problem and have to investigate the cause. And it can help if you have an overview of all the dimensions and angles on the tap. We would like to provide you with this overview in our blog posts - today on the subject of clearance angles. Can you tell us off the top of your head what the clearance angle is, where it is and how big it should be? No? Never mind. Because we answer all these questions in this blog post.
What exactly is the clearance angle on the tap?
So let's first look at what the clearance angle is. To do this, we must first find it and then determine what effects it has during thread cutting. Incidentally, clearance angles are not only found on taps, but also on every tool cutting edge, including twist drills. If you are familiar with the clearance angle, this will have a positive effect on your entire manual work.
This is where the clearance angle can be found on the tap
The clearance angle is one of the angles on the cutting edge of the tool. More precisely, the clearance angle is the angle between the flank face of the tool and the workpiece. The term clearance angle refers to the area on the cutting wedge that faces the surface of the workpiece. The rake face is located on the other side of the cutting edge.
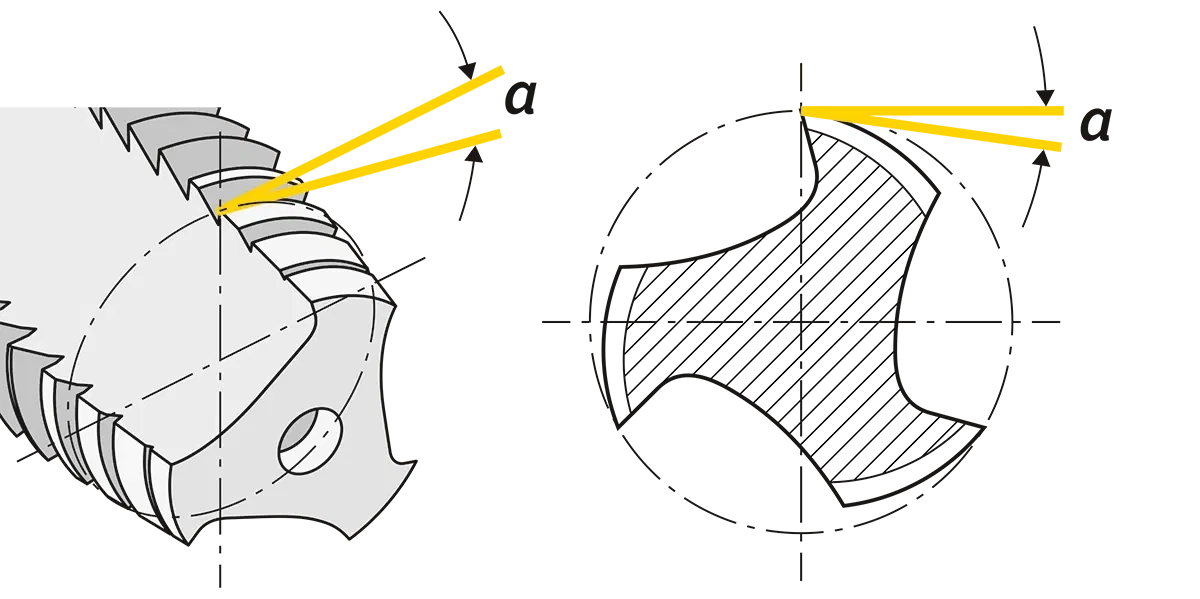
This is the function of the clearance angle on the tap
The clearance surface on the tool and the cutting surface on the workpiece should touch each other as little as possible. Too much contact would result in high frictional forces, which in turn would lead to an enormous build-up of heat. And as we all know, too much friction and heat is not a good idea for either the workpiece or the tool. The result would be a short tool life and unsightly surfaces. So the clearance surface must be angled away from the cutting surface on the workpiece so that both surfaces have as few points of contact as possible. And this is possible thanks to the clearance angle. In this way, the clearance angle prevents the tap from jamming or breaking off.
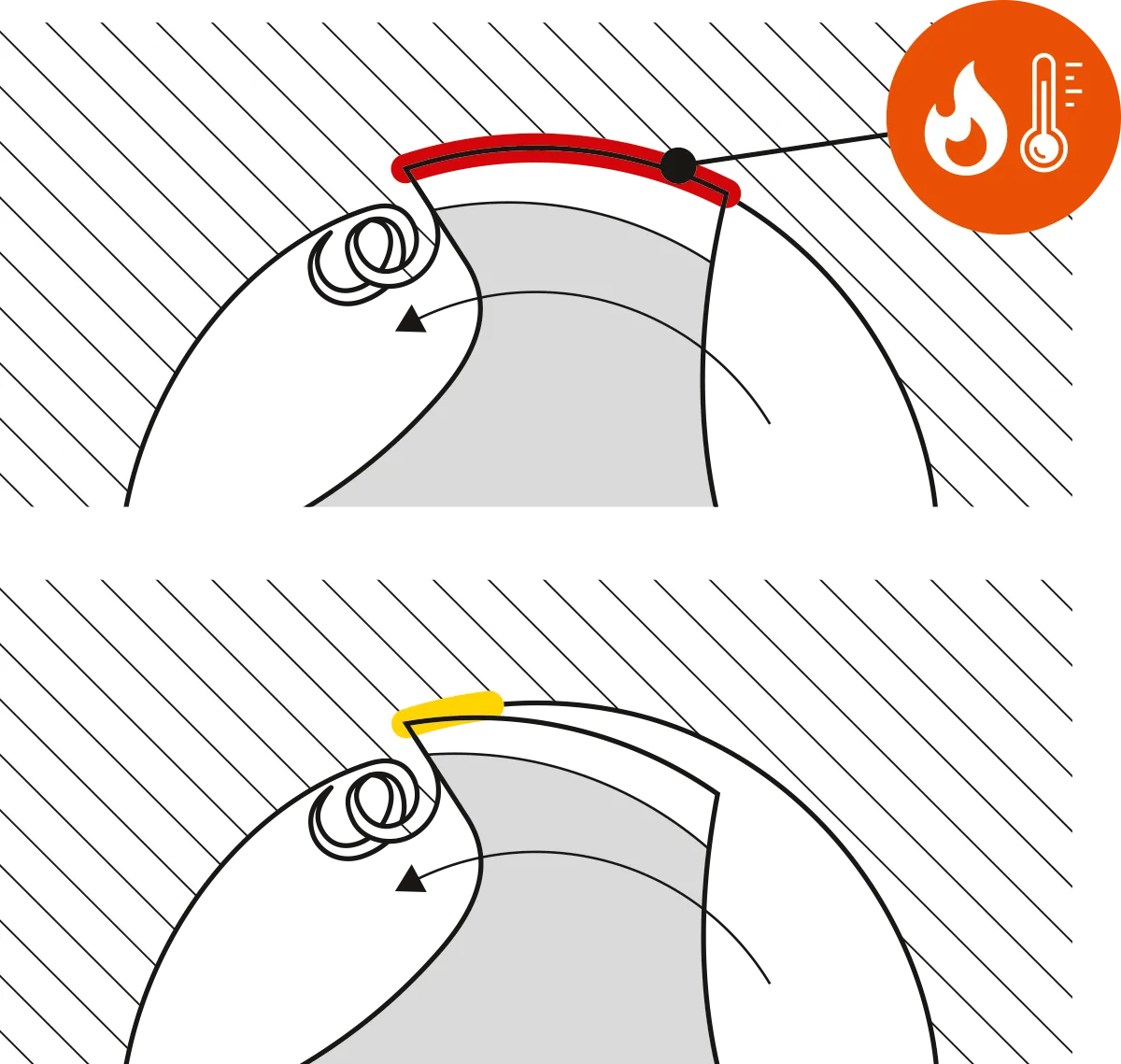
The interaction between clearance angle and other angles on the tap
A large clearance angle therefore ensures a large distance between the flank face and the cutting surface and therefore less friction. Unfortunately, the calculation is not quite so simple. This is because the clearance angle does not stand alone, but only ever occurs as part of a trio. In addition to the clearance angle α, there is also the wedge angle β and the rake angle γ, which must always be taken into account. All three angles together always result in 90°, so the choice of clearance angle has a direct effect on the size of the two colleagues. The larger the clearance angle, the less leeway there is for the rake and wedge angles. However, as these are also of great importance for the success of the tapping process, the clearance angle must always be selected with care and sensitivity.
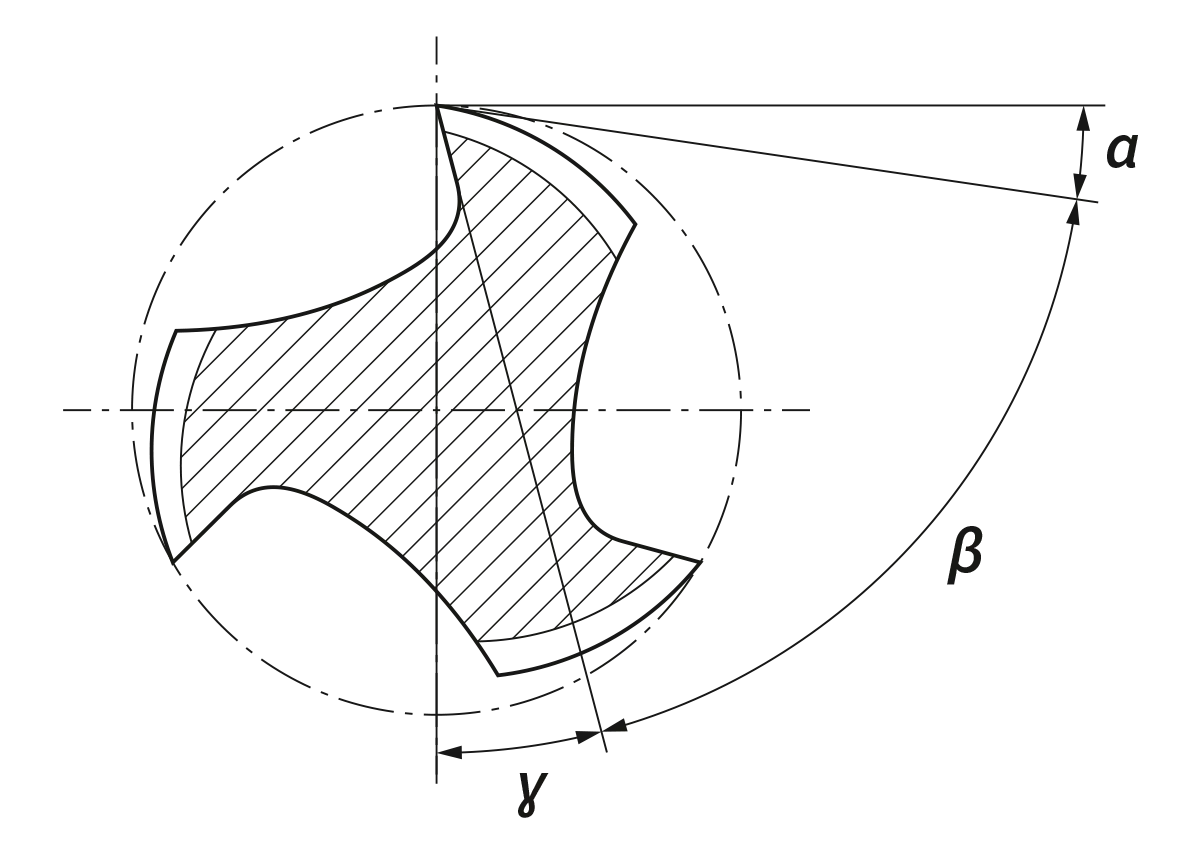
How large should the clearance angle of the tap be?
As a general rule, the clearance angle should be as small as possible but as large as necessary. Due to the correlation explained above, a large clearance angle leads to a smaller wedge angle and therefore to a cutting wedge that is more susceptible to wear and damage. However, if the clearance angle is too small, it cannot prevent friction effectively enough. A good balance between the two extremes is therefore crucial for the clearance angle.
The choice of clearance angle also depends on the machinability of the material. The more difficult a material is to machine, the larger the clearance angle should be. A large clearance angle is when the angle is between 6° and 13°. If it is less than 6°, it is a small clearance angle.
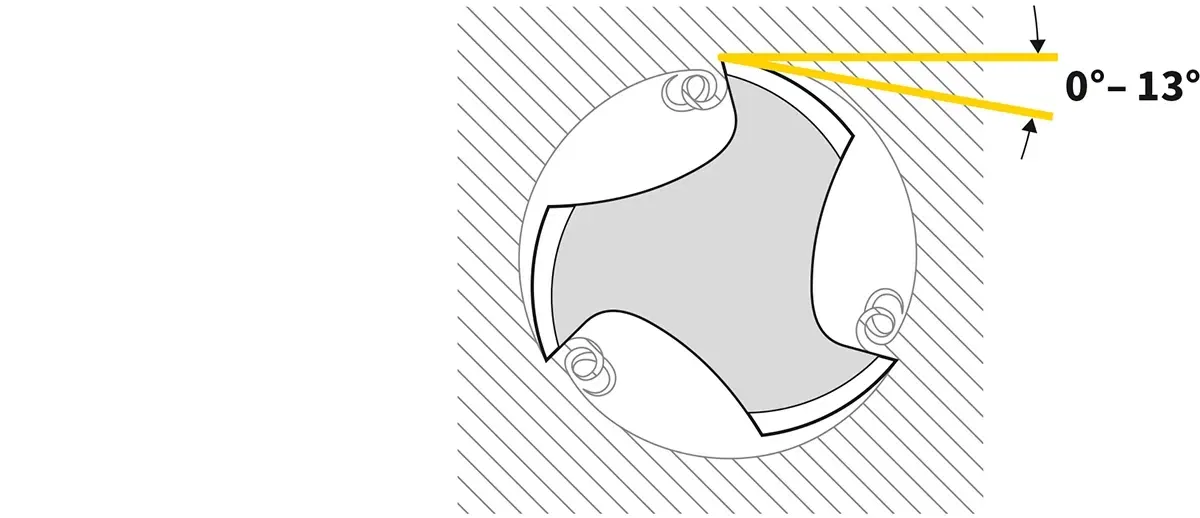
These typical problems are related to the clearance angle of the tap
If we take a look at what we have established with regard to the size of the clearance angle, we can already see the most common problems. A small clearance angle causes too much friction and heat generation and consequently leads to high tool wear. However, a clearance angle that is too large can also lead to increased wear because it destabilizes the cutting wedge.
However, too large a clearance angle can also be the cause of a tap breaking off when removing it from the finished thread, as it increases the risk of the chip jamming. To avoid this, you should always ensure that the last thread is completely cut before unscrewing through threads.
What do relief angle and relief grinding have to do with each other?
As is so often the case, there are various terms for clearance angles, some of which are used interchangeably. Instead of relief angle, the terms relief grinding or free grinding are often used. The term relief grinding simply focuses more strongly on the grinding process in which the clearance angle is created. The relief angle and relief grinding therefore refer to the same point on the tap, but look at it from slightly different angles.
You can also find tapping tools with exactly the right clearance angle in the BAER online store! All your questions on this and many other topics will be answered by our friendly customer service team, which you can reach conveniently via our contact form.