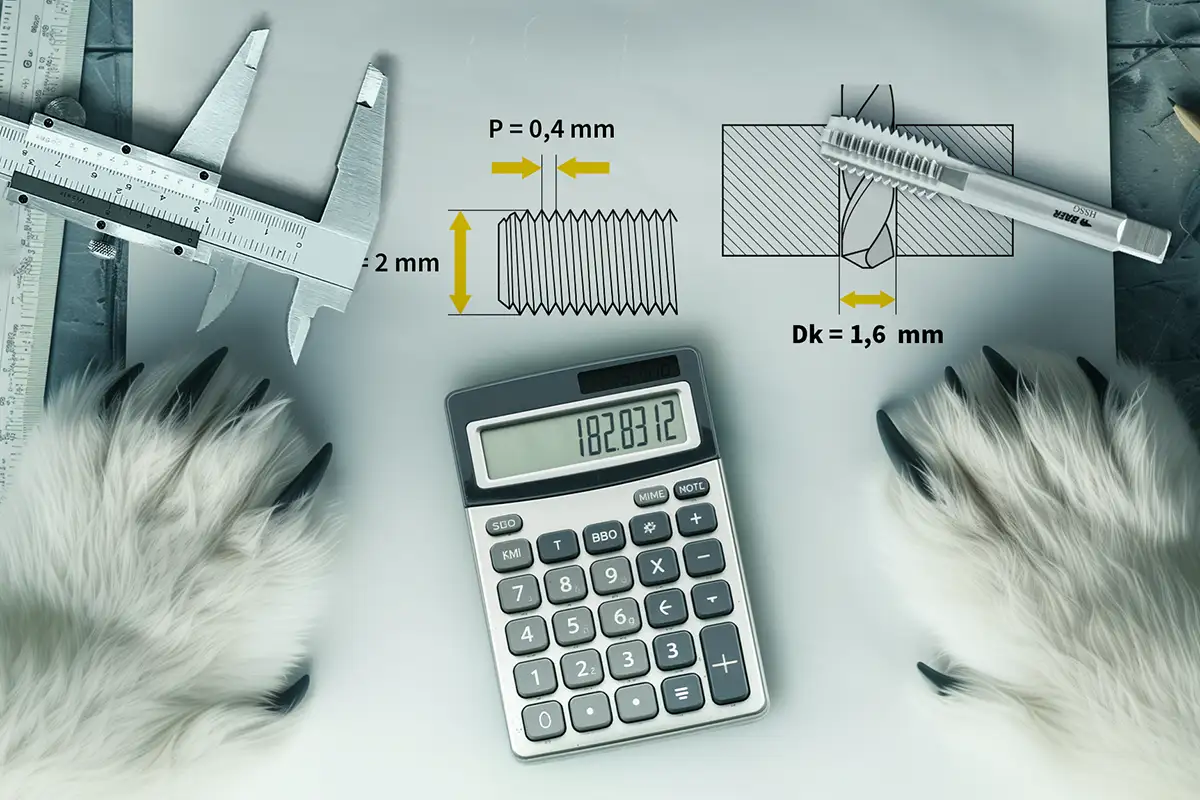
Formulas for Thread Cutting: What You Need to Know
Do you sometimes rely on guesswork when cutting threads or use trial and error to achieve the desired result? Don’t worry, we won’t tell anyone. In fact, these methods often work quite well for DIY projects and many standard applications—until they don’t. And then, expert advice becomes costly.
The thread just won’t turn out right, you keep encountering issues with the component or tool, or you can't achieve the desired dimensions? >Then an error has likely crept in somewhere, usually during the preparation of the core hole drilling or in the machine settings. If you know the correct values for these situations, you can avoid many mistakes before they happen. And that is exactly what this blog post is about. You can calculate the correct settings using formulas, but there are a few things to consider.
Look it up or calculate it yourself? The best way to get a clean thread
The first question is whether you really need to know the formulas for calculating cutting speed and other factors. After all, these calculations have been done thousands of times for every material and diameter, and you can simply look up the results in a table. In fact, this might even be the better option since it helps avoid calculation errors and ensures reliable results.
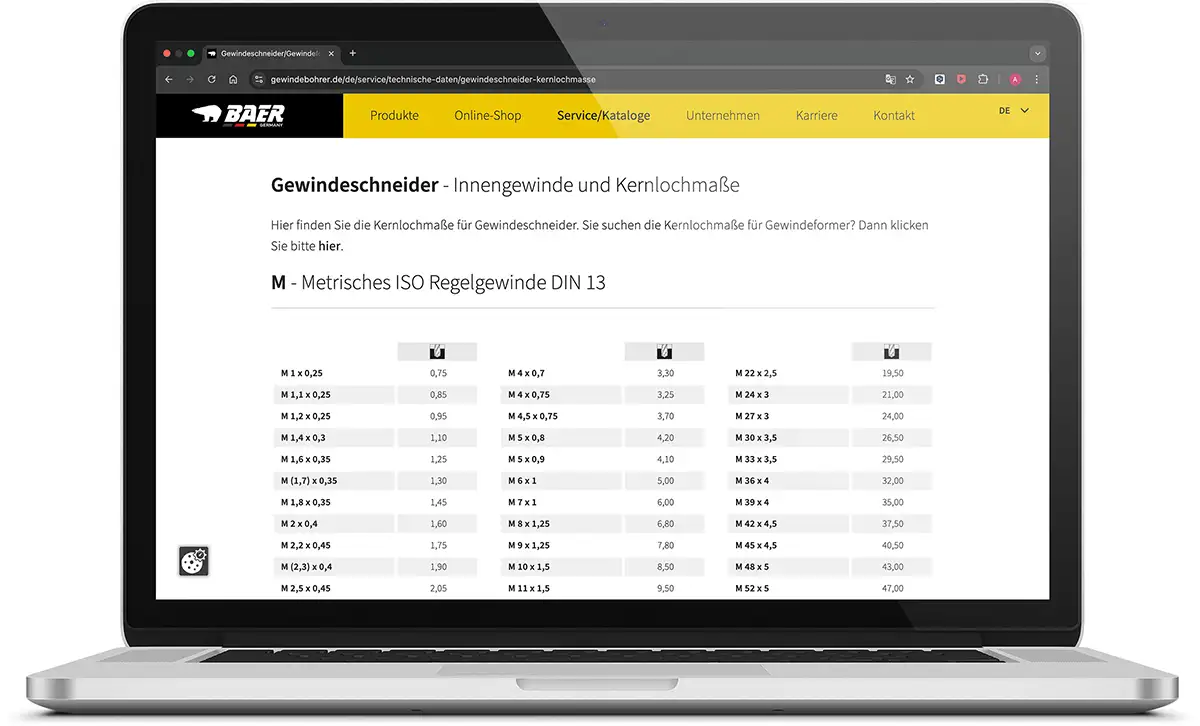
So why does it still make sense to at least familiarize yourself with the underlying formulas? First, it’s much easier to identify errors if you have some basic knowledge of the subject. Second, tables with the necessary values are not always easy for beginners to understand. A bit of foundational knowledge never hurts.
RPM and π – How much prior knowledge is needed?
You probably haven’t studied mechanical engineering; otherwise, you wouldn’t be reading this. So, is what you remember from physics class enough to understand thread-cutting formulas? For our purposes, yes. You only need to be able to read the tables correctly, understand the relationships between different variables, and perhaps perform simple calculations for standard situations.
Using a Tap: The Most Important Formulas
While there are many values you can calculate, the most relevant ones for thread tapping are likely the core hole diameter, followed by the cutting speed and possibly the feed rate. Since these speeds are related to the spindle speed, we’ll take a look at that as well.
Core Hole Diameter
Let's start simple. The core hole diameter for threads with a 60° flank angle (which applies to most fastening threads) is so easy to calculate that you might be done before even looking up the correct value online.
The formula is:
Thread diameter (D) – Pitch (P) = Core hole diameter (Dk)
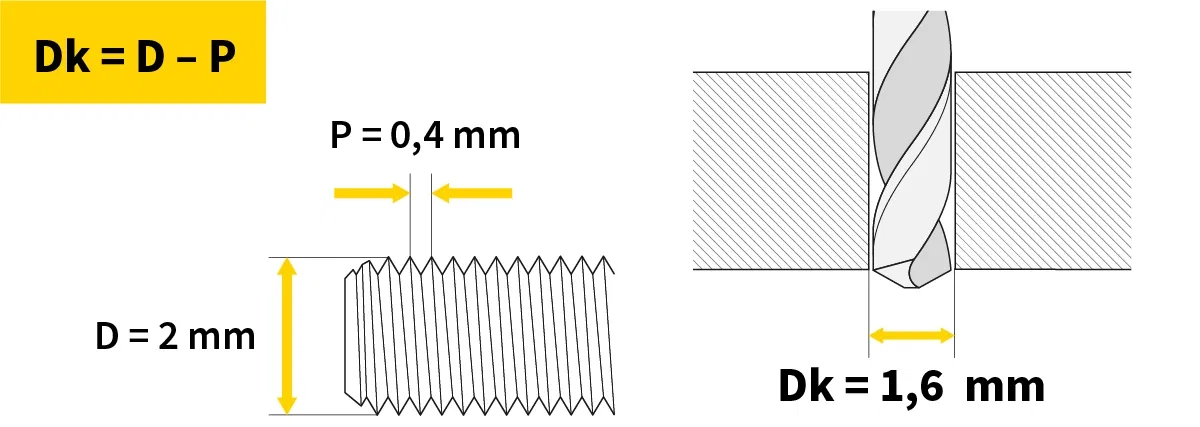
For the M 2 × 0.4 thread, this results in a core hole diameter of 1.60 mm.
Cutting Speed
Cutting speed describes how fast the cutting edge moves in the cutting direction and is influenced by many factors. It is also an economic factor, as a higher cutting speed reduces working time. However, increasing it indefinitely negatively affects the quality of the result and the lifespan of the tool. On the other hand, a lower cutting speed can extend tool life, but certain limits should not be exceeded.
As a DIYer, these economic considerations might not be your primary concern, so it’s enough to ensure that your cutting speed stays within the acceptable range.
Cutting speed is represented by vc, where v stands for velocity and c for cutting. The unit used is m/min. You can calculate cutting speed with the formula:
vc [m/min] = (Outer diameter × π × RPM) / 1000
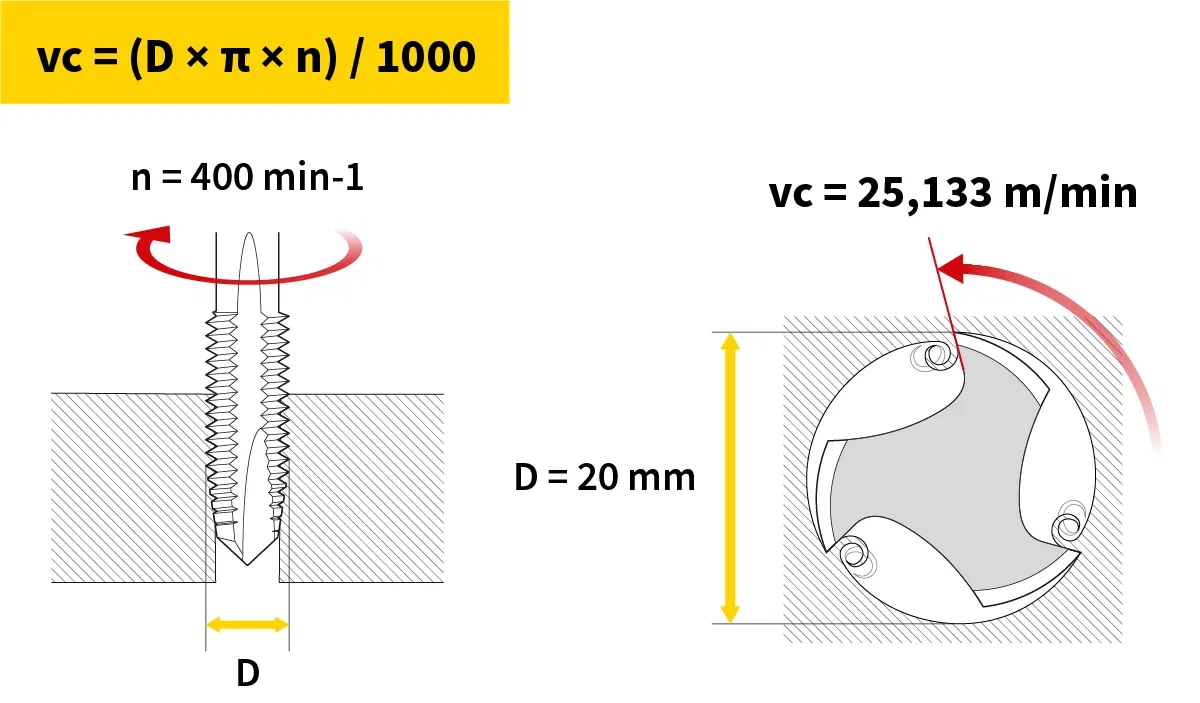
Using an outer diameter of 20 mm and an RPM of 400 min⁻¹, we get a cutting speed of 25.133 m/min.
Feed Rate
The feed rate refers to the speed at which the tool moves into the material. Unlike cutting speed, this is not about rotation but movement in the axial direction.
Feed rate is represented by vf, where v stands for velocity and f for feed. The unit used is mm/min. You can calculate the feed rate with the formula:
vf [mm/min] = (Feed per revolution × RPM)
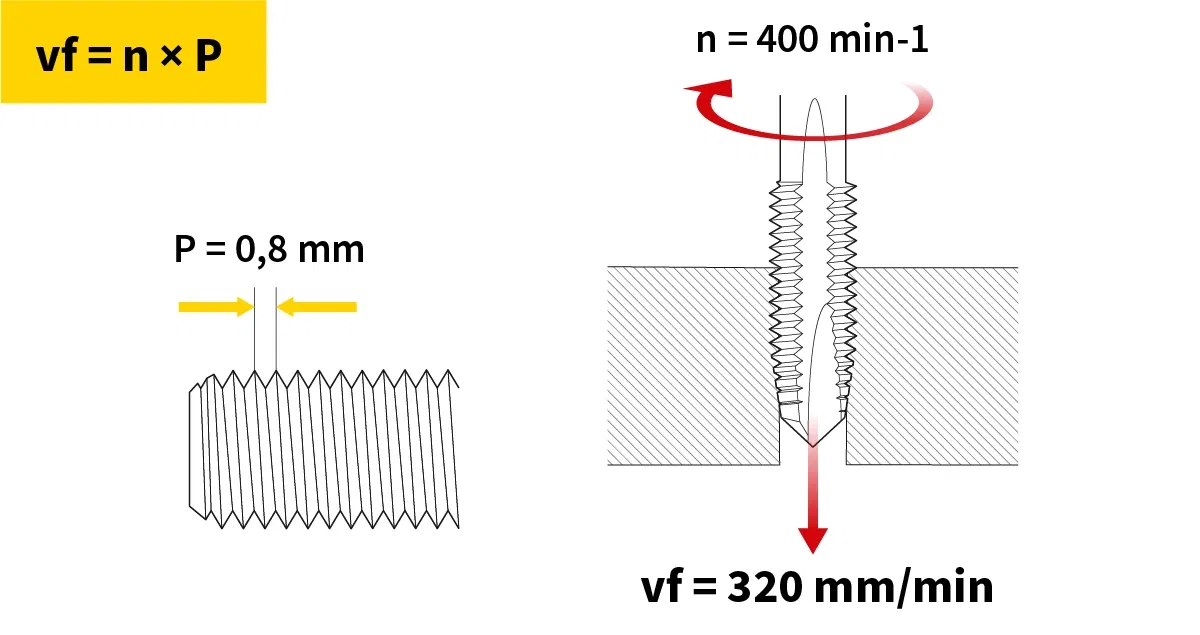
Using an RPM of 400 min⁻¹ and a feed per revolution of 0.800 mm, the feed rate calculates to 320 mm/min.
When cutting threads, there is a direct relationship between feed and pitch, as the pitch defines how far the tool moves in the axial direction per revolution. However, this applies only to metric threads. TPI values for imperial threads must first be converted.
Spindle Speed
That leaves the spindle speed, which indicates how often the tool rotates within a given time. It is represented by the letter n and measured in min⁻¹ or revolutions per minute (RPM).
The formula for spindle speed is:
RPM n [1/min] = (Cutting speed in m/min × 1000) / (Outer diameter × π)
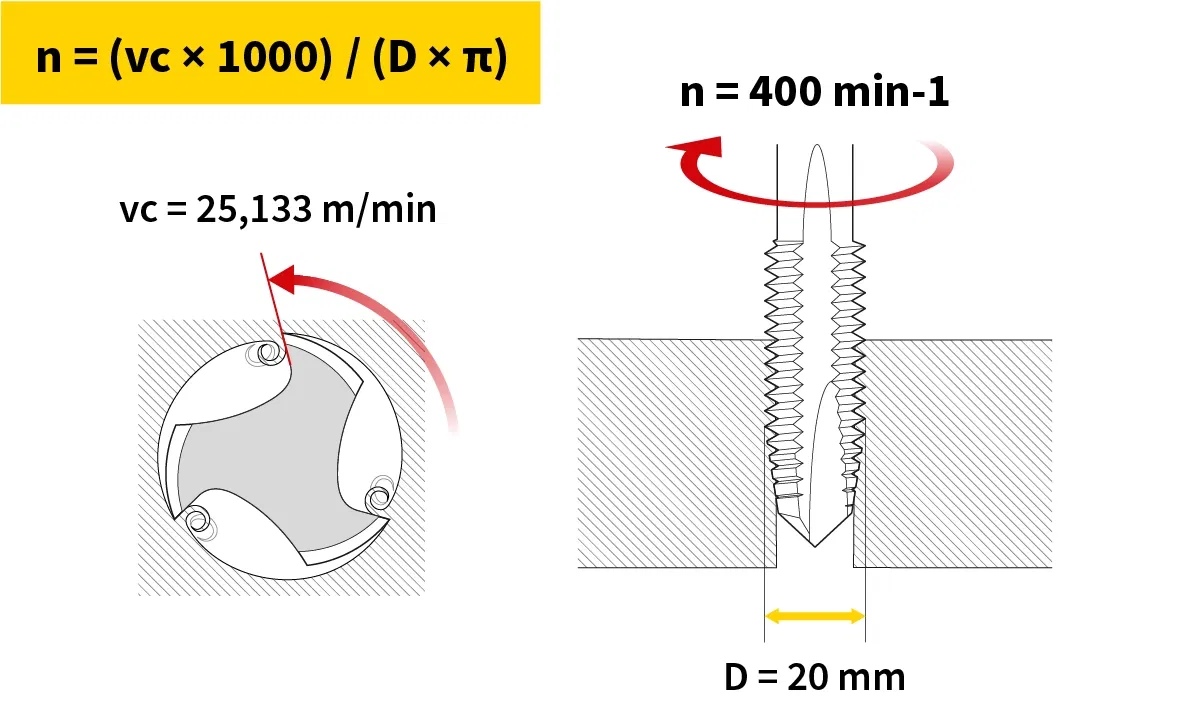
Using the same values as before—cutting speed of 25.133 m/min and an outer diameter of 20 mm—we again arrive at an RPM of 400 min⁻¹.
How to Find the Required Values Without Calculating
Of course, there are ways to determine the correct values without manual calculations. Various calculators online allow you to input known values and get instant results. Reference values can also be found in tables, whether in physical reference books or through a quick internet search.
Additionally, in our BAER online shop, every product page provides detailed information and further links to help you set up your machine correctly. It’s worth taking a look! And if you ever need assistance, our customer service is available via phone or through our contact form.