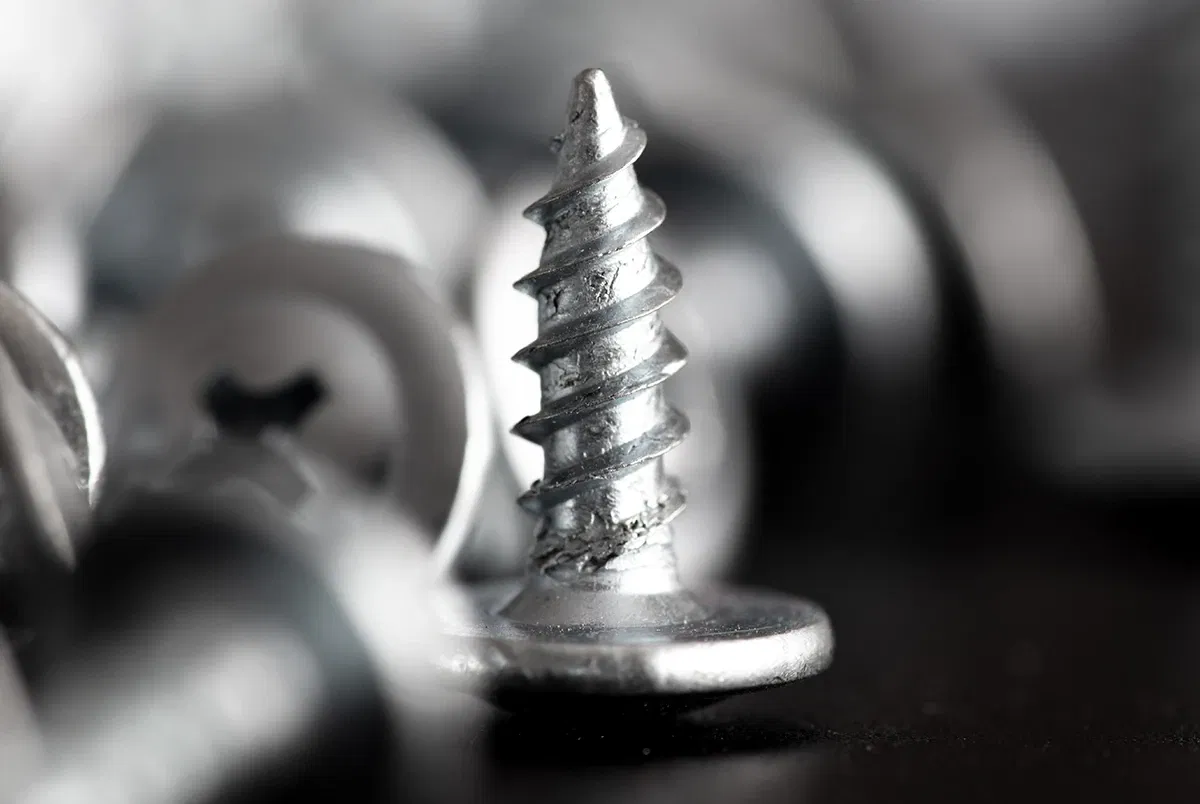
Not for the faint-hearted: The sheet metal screw thread
When it comes to screws and threads, the power dynamics are clearly defined: All screws have a thread, but not all threads are on a screw. Without its thread, a screw would just be a boring bolt. It is the thread that gives the screw the necessary properties for fastening components and bestows the specialists among them with their unique capabilities.
This blog post focuses on one such specialist: sheet metal screws and their corresponding thread type. As the name suggests, sheet metal screws are commonly used when working with sheet materials. But they offer more than that and have some interesting characteristics that may surprise you. Curious? Then keep reading to learn everything about sheet metal screws and their threads!
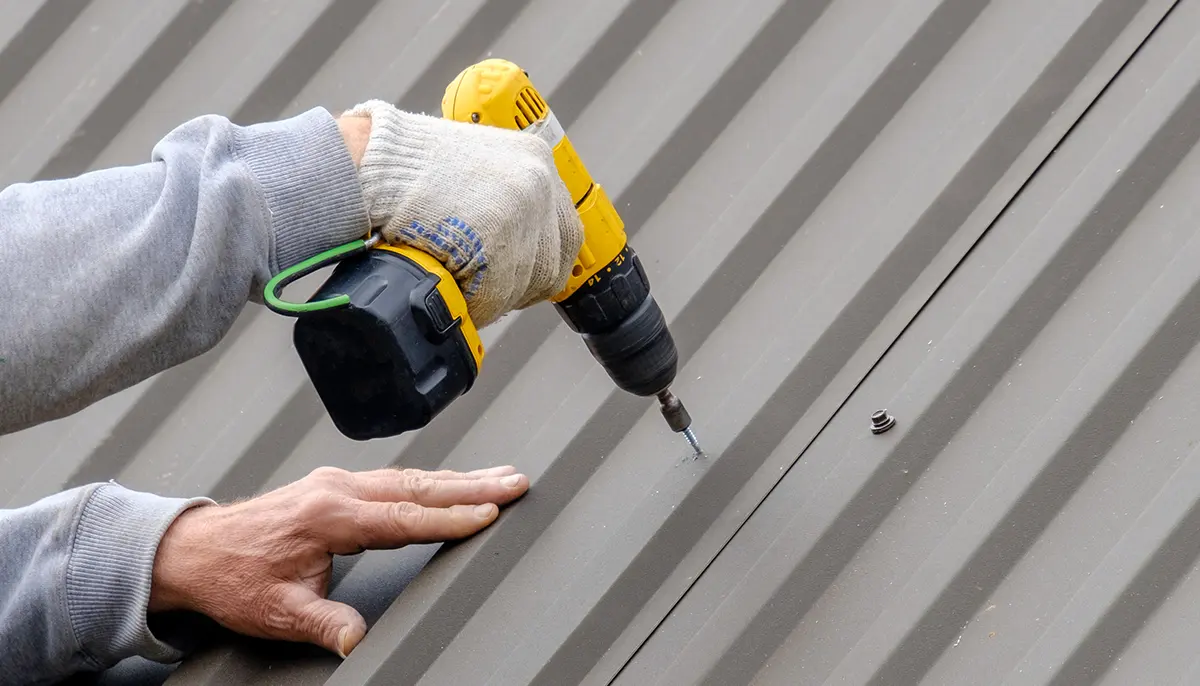
Sheet metal screw thread according to DIN EN ISO 1478: All the special features of this thread type
Let's start with the thread itself. Sheet metal screws are equipped with a thread standardized according to DIN EN ISO 1487. The flank angle is 60°, and the edges in the profile are slightly rounded. At first glance, the wide thread grooves stand out, which resemble those of wood screws.
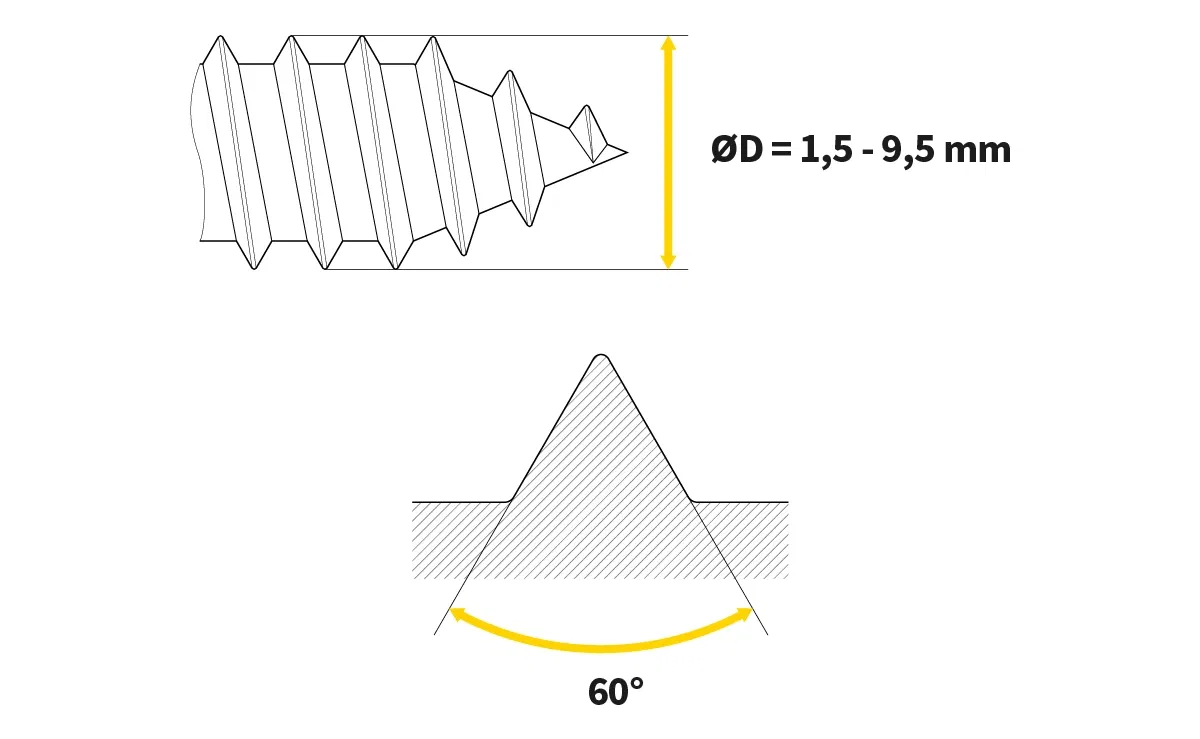
According to the EN standard, the abbreviation for the sheet metal screw thread is ST, although BL is also occasionally used. The standard covers thread sizes from 1.5 mm to 9.5 mm nominal diameter. The thread designation consists of the abbreviation ST and the indication of the nominal diameter. The sheet metal screw thread is a metric thread, which means that all measurements are given in millimeters.
Where are sheet metal screws used?
Typically, sheet metal screws are used wherever thin sheets of metal need to be fastened to other components, such as during the assembly of casings or in vehicle construction. A common issue arises due to the material thickness. The sheet metal used must always be thicker than the pitch of the screw's thread to ensure that at least one full thread turn can be formed. If the material is thinner, the screw will not hold. Therefore, this factor must be carefully considered when selecting the thread size.
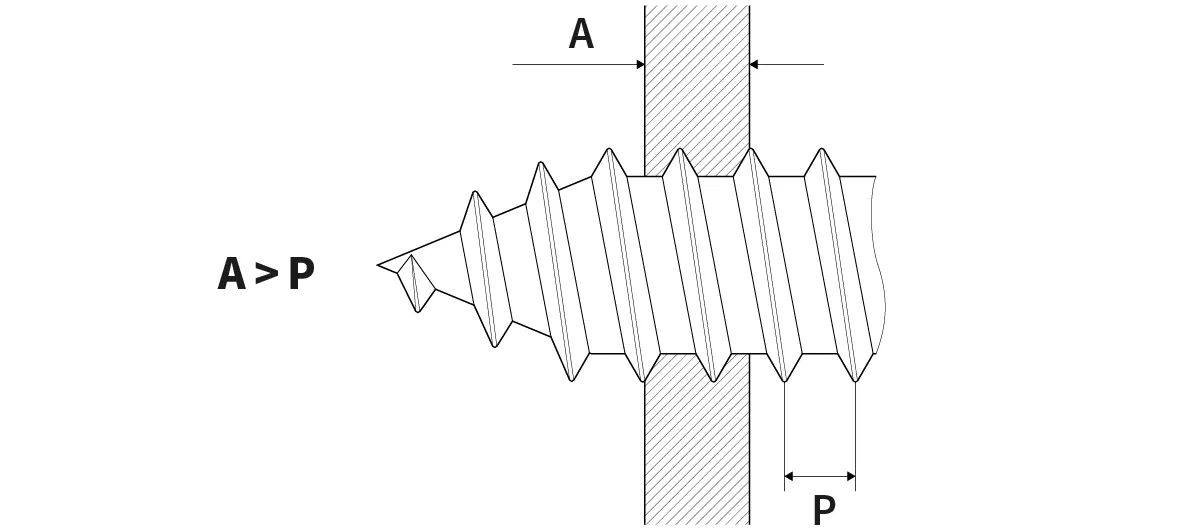
Sheet metal screws are usually self-tapping screws
Sheet metal screws are often self-tapping screws. This means that these special screws can cut their own internal thread as they are screwed in. A prerequisite for this is sufficient material thickness and a suitable pilot hole.
This pilot hole essentially corresponds to the core hole used in thread tapping. The hole must be slightly smaller than the thread itself so that enough material remains to form the thread flanks. The exact dimensions depend on the properties of the material and the mounting conditions, but reference values can be found in appropriate charts.

Just like with thread production using a threading tool, sheet metal screws can either cut or form the thread. Cutting is a material-removing process in which material is shaved off to create the thread. This excess material appears as chips and can cause issues depending on the application. In contrast, thread forming merely displaces the material, so no chips are produced.
In general, self-tapping screws offer the advantage that, when used correctly, the thread fits perfectly and has no play. Caution is only advised if you regularly remove and reinsert such a screw. In these cases, particular care and a delicate touch are required to re-engage the already cut thread. If you're too forceful, you may inadvertently create a new thread, potentially damaging both the thread and the component permanently.
No tap needed?
So the question remains: If the screw cuts the sheet metal thread itself, do you still need a thread tap? In certain cases, yes. The self-cutting feature works best in softer materials like aluminum and thin sheet metal. But what if you want to cut a sheet metal screw thread into other materials like steel or components with greater material thickness? In these cases, you won’t be able to avoid using a thread tap. Also, not all screws for sheet metal are actually self-tapping. In such cases, you will need to create the thread before screwing in.
Head shape and more: These variants exist
Sheet metal screws are one of the most important fastening elements in modern industry. Accordingly, the variety of products is large. They are primarily distinguished by their head shape, with flat head, countersunk head, and pan head being the most common types. The tip of the screw is usually pointed. However, there are also models that end in a pin.
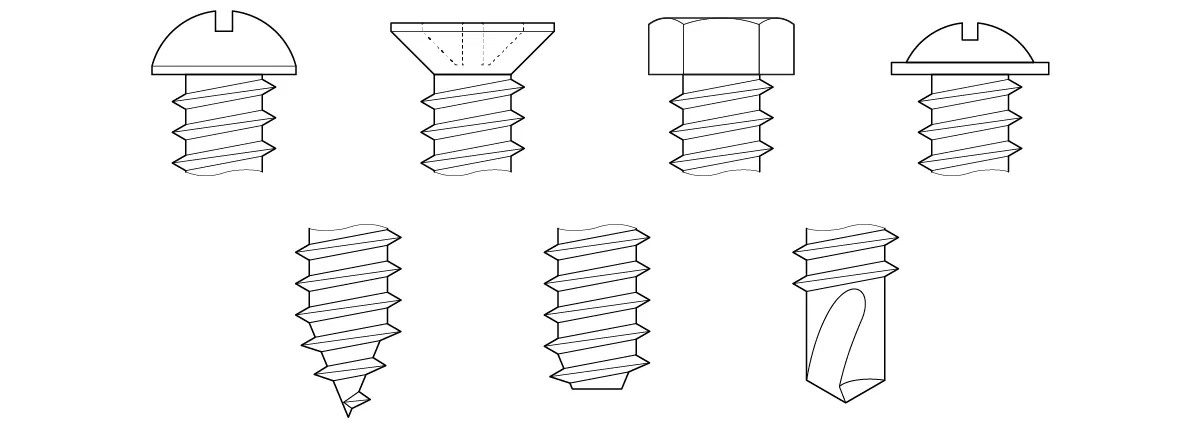
There are also some special types. One of them is the screw with a drill point. This makes it possible to eliminate not only thread cutting but even the need for pre-drilling. These screws are therefore also known as self-drilling screws, as they allow very fast work without interruptions.
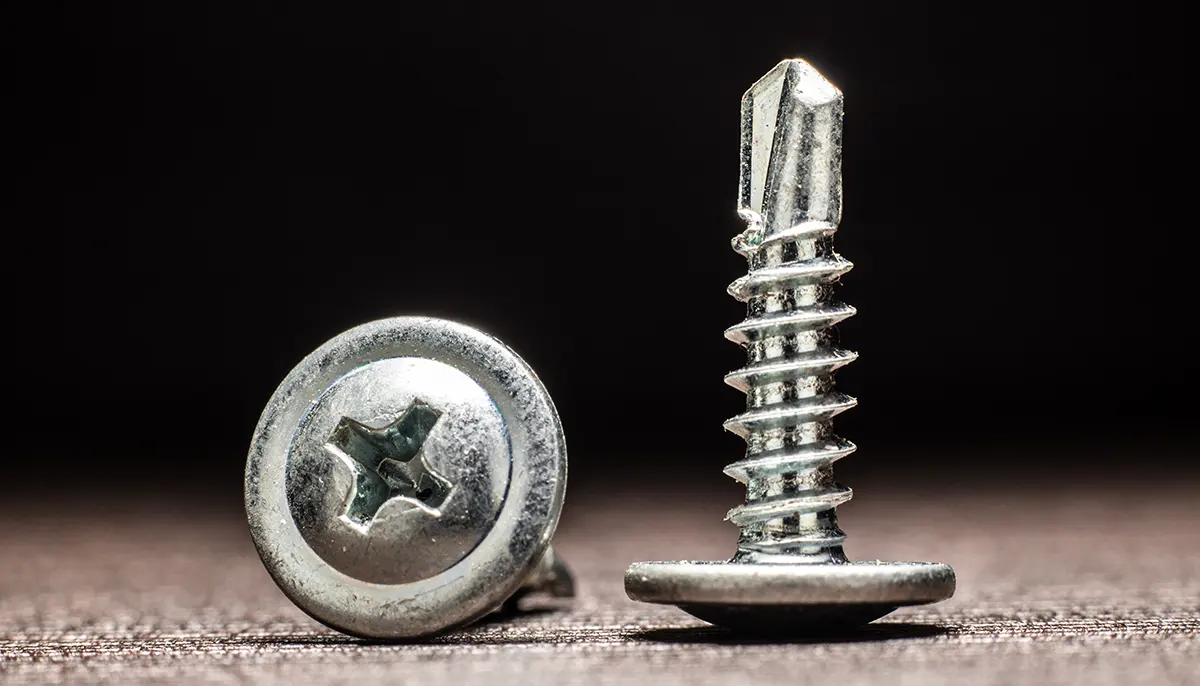
At BAER, we have made it our mission to fully meet your needs when it comes to threading tools. Even if you only rarely need a thread tap for sheet metal threads – if you ever do, you’ll find what you need with us! We offer taps and dies for sheet metal screw threads and countless other items for processing both common and rare thread types. Take a look at our shop and see for yourself. Need more information or have a question? Our customer service will be happy to help.