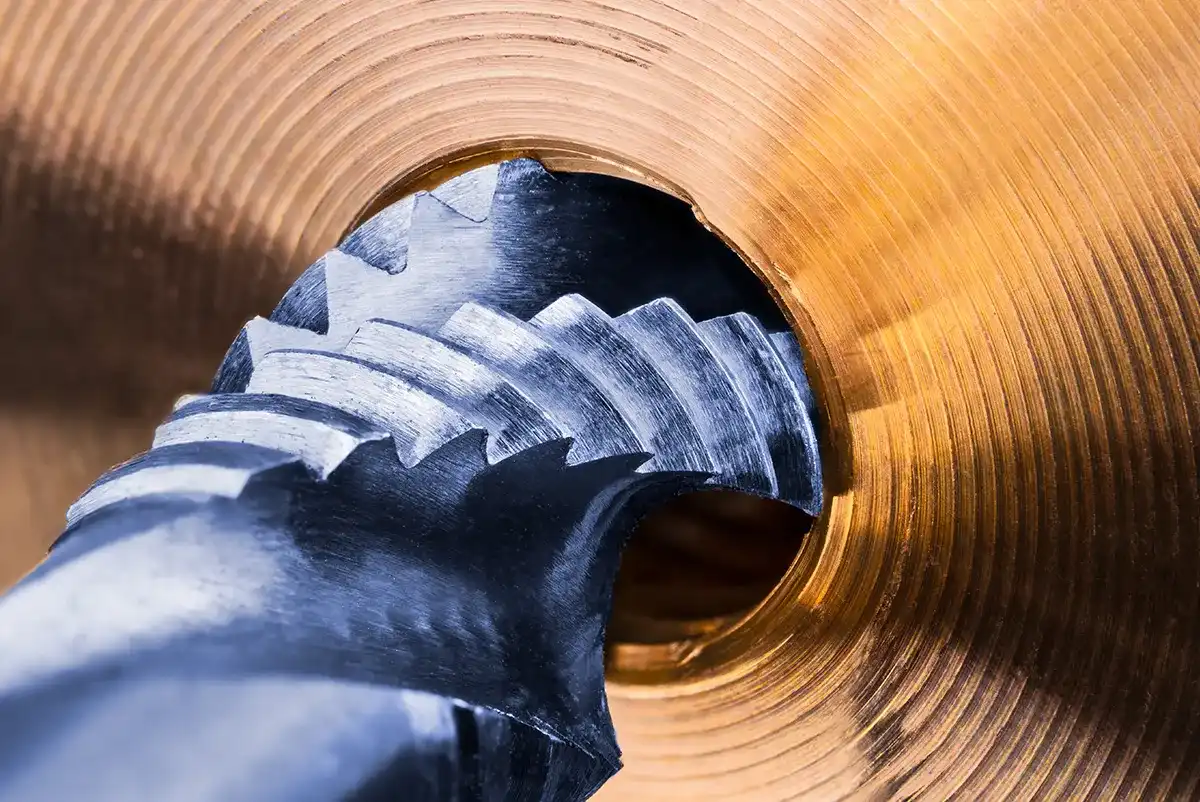
Thread cutting as a machining production process
Thread cutting is a machining production process - you've probably heard that a lot. But have you ever wondered exactly what it means? Let's get to the bottom of this question together today.
What is the difference between machining and other manufacturing processes, what exactly happens when a thread is cut and are there other ways of producing a thread? You will find out this and much more if you read on.
A distinction is made between the following manufacturing processes
The common goal of all manufacturing processes is to produce a previously planned workpiece shape, preferably as precisely and economically as possible. There are numerous ways to achieve this goal. In manufacturing technology, these are initially divided into six main groups:
- Prototyping
- Reshaping
- Cutting
- Joining
- Coating
- Changing material properties
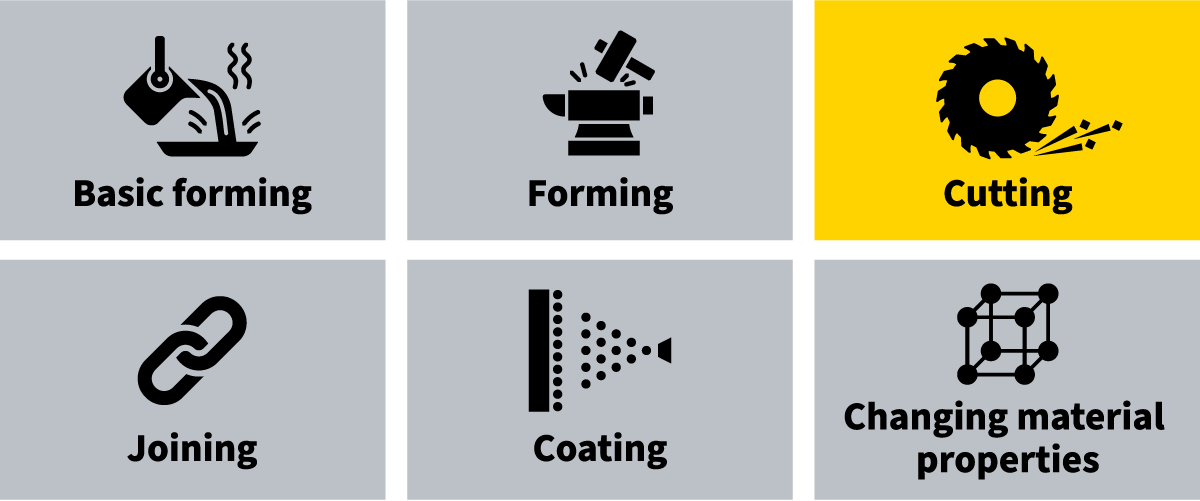
Machining processes belong to the third group, cutting. What all processes in this group have in common is the fact that material is removed in order to change the shape of the workpiece.
Which machining processes are available according to DIN 8589?
If you were already surprised by the number of main groups, then unfortunately we can't give you the all-clear yet. We are still a long way from tapping. The machining processes can also be further subdivided in many ways.
The subdivision of machining processes
Machining is therefore a subgroup of the separating manufacturing processes. However, further subdivisions can be made here. Firstly, it is divided into:
- Cutting with a geometrically defined cutting edge or
- Cutting with a geometrically undefined cutting edge
When tapping, the number and exact geometry of the cutting edges are not only fixed but extremely important for the result of the process. These are therefore cutting processes with a geometrically defined cutting edge.
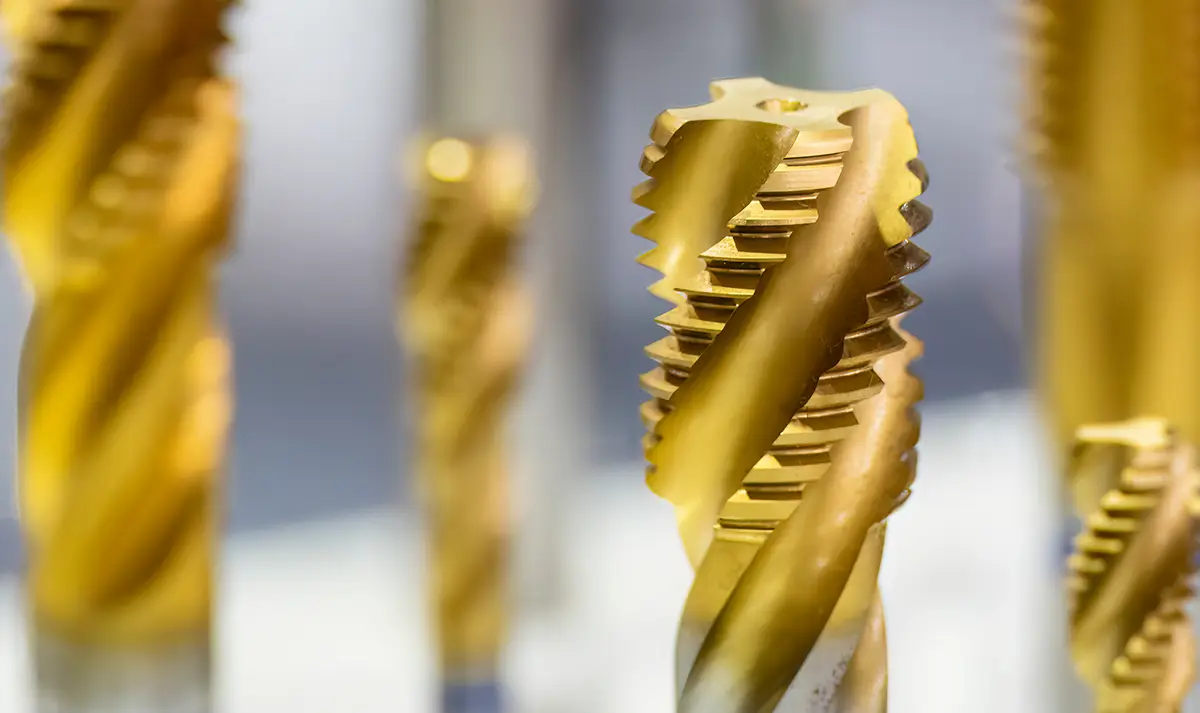
In contrast, grinding is an example of cutting with a geometrically undefined cutting edge. Here, cutting edges remove material at a microscopic level along the edges of the grains on a grinding wheel.
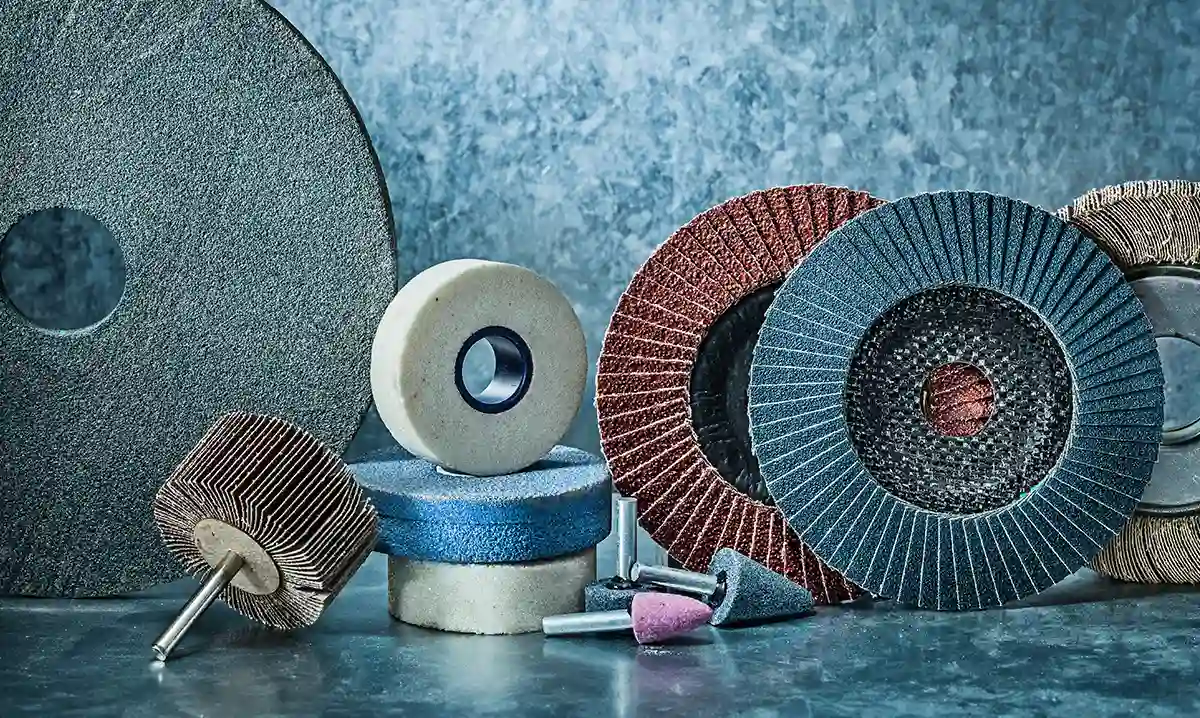
Cutting with a geometrically defined cutting edge
The group of machining processes with a geometrically defined cutting edge can also be divided into numerous other subgroups. These include turning, milling, and sawing. Drilling, countersinking, and reaming form a common subgroup, and now we have almost arrived at tapping!
Drilling, countersinking, reaming
These three processes are grouped together because they share similar cutting and feed conditions, and the tools used are also similar in many respects. In addition to solid drilling, boring, and profile drilling, drilling also includes tapping.
In summary, the sequence of the groups is as follows:
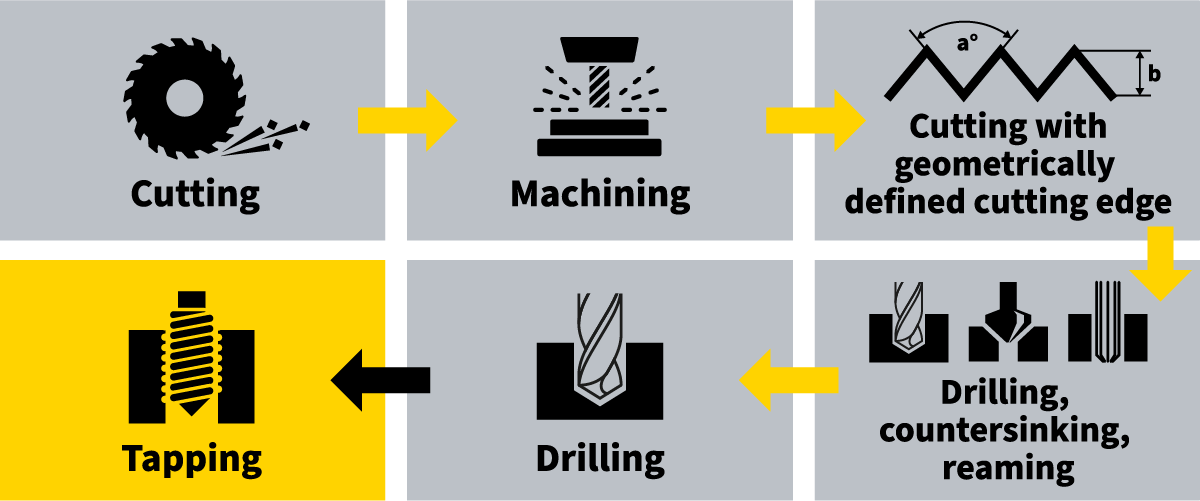
Cutting → Machining → Machining with a geometrically defined cutting edge → Drilling, countersinking, reaming → Drilling → Tapping
What happens to the tool and workpiece during machining
Two movements are crucial when machining: the cutting movement and the feed movement. In drilling, the cutting movement is circular and is carried out by the tool – unlike turning, where the workpiece rotates. The feed ensures that the tool can penetrate the material.
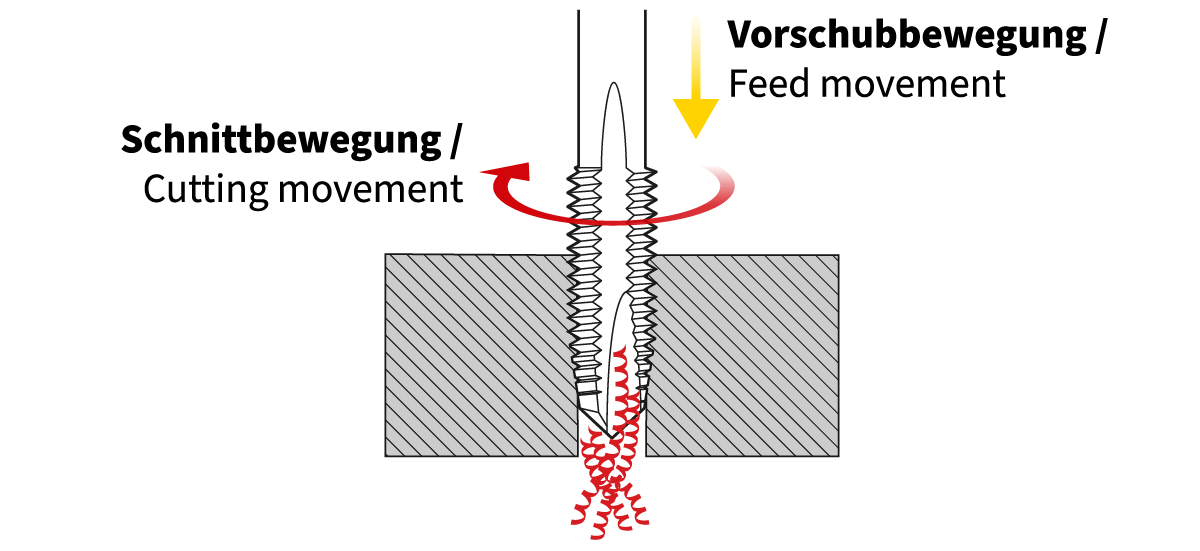
A key characteristic of machining is chip formation. The removed material does not simply disappear into thin air but forms chips of various shapes. This is an unavoidable side effect that can lead to problems, especially when tapping.
The machinability of a material is a crucial factor when it comes to shaping workpieces by hand or using machine tools. Most metals are easy to machine, which is why this manufacturing process is particularly important in metalworking.
Chipping during tapping
Unlike drilling into a solid material, the first step in cutting a thread is creating a core hole. The cutting process takes place at the very front of the tool, in the area of the chamfer. The remaining threads on the tap serve as guidance.
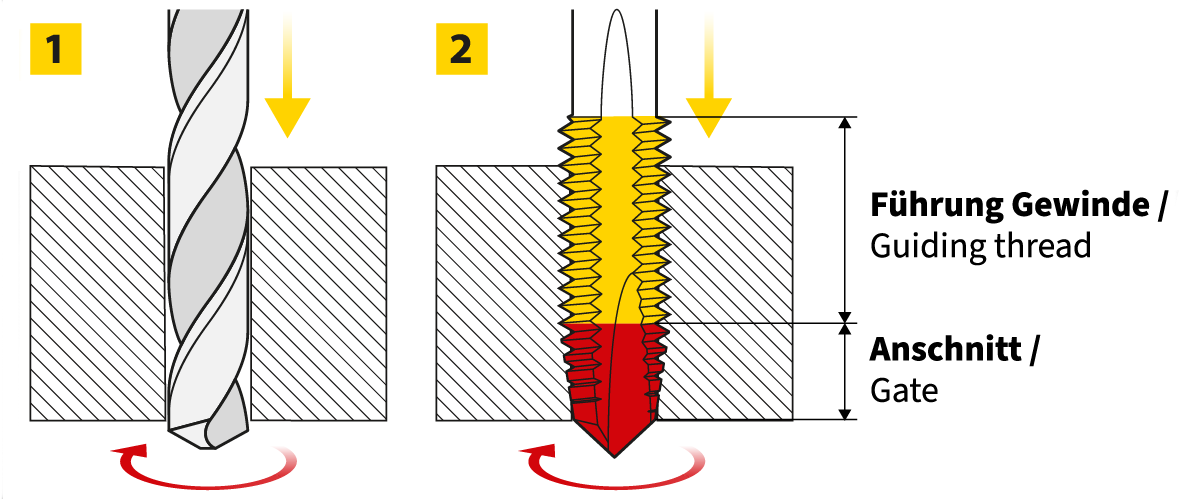
A tap also performs a cutting and a feed movement, with the feed being determined by the thread pitch. Depending on the type of hole, the removed material is transported away through the flutes either in the cutting direction or against it.
A machine tool can create a thread in a single operation. When tapping by hand, however, three (or two for fine threads) tools are always required: a pre-cutter, an intermediate cutter, and a finish cutter. This divides the cutting process into multiple steps, and only the finish cutter creates the fully developed thread profile.
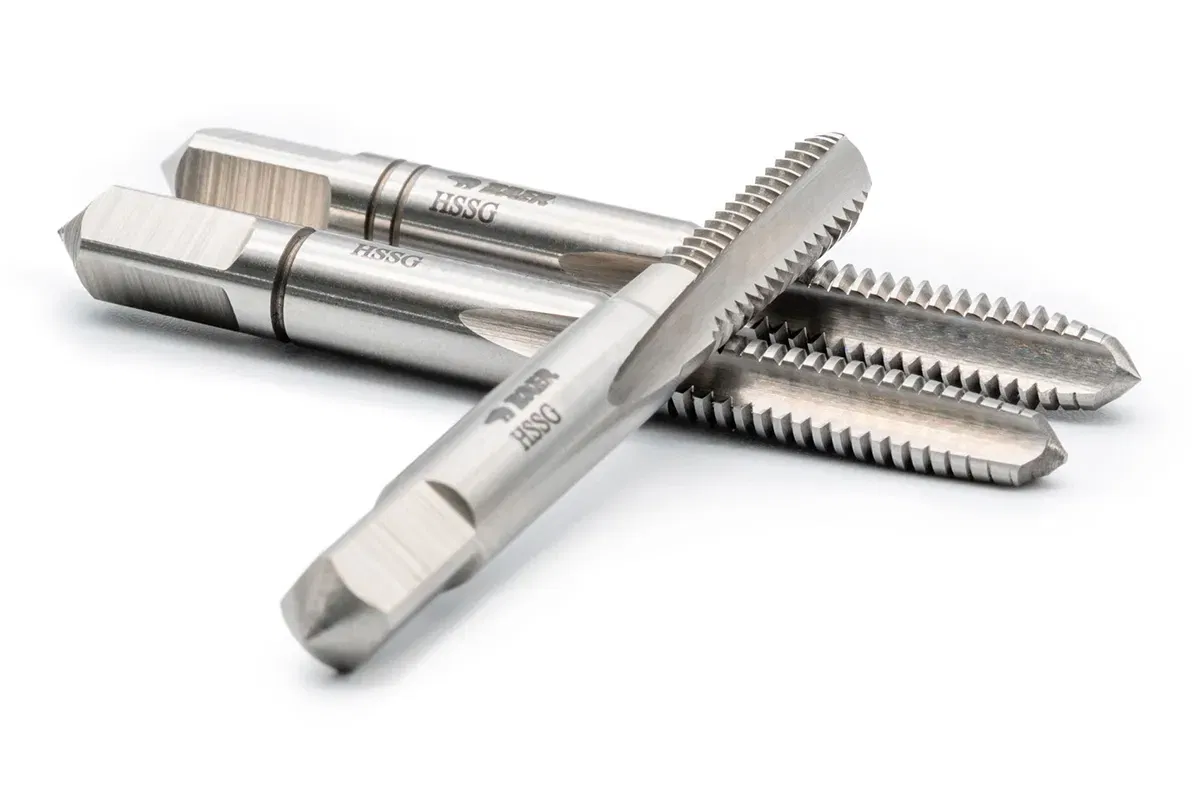
Are there also non-cutting methods for thread production?
In addition to tapping, other processes can be used to produce a thread. These include machining methods such as turning or milling. However, it is also possible to produce threads without any cutting.
Thread forming or thread rolling is a non-cutting process that is also frequently used to produce threads. In this process, the material is not removed but merely displaced. As a result, the fibers of the material remain intact.
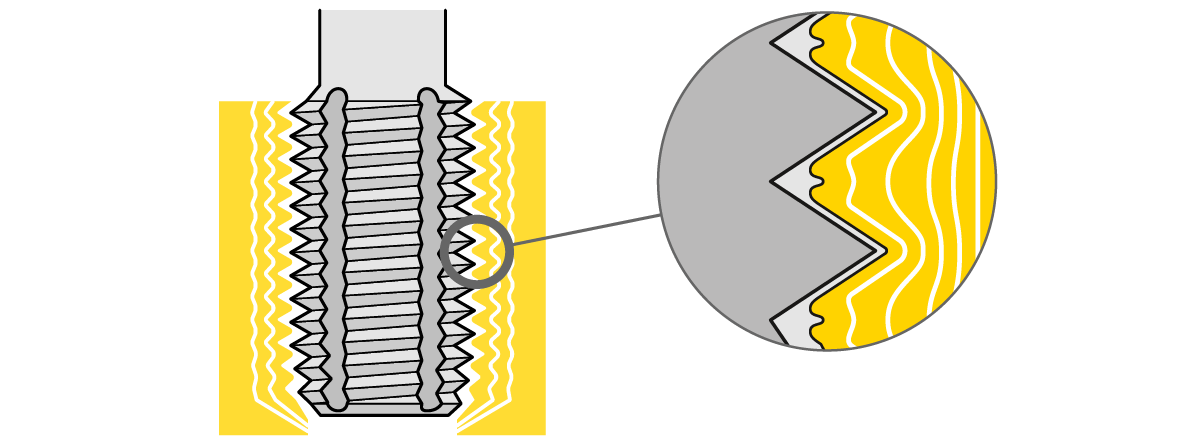
Thread forming is a good alternative for stable internal threads in materials with low tensile strength. As no chips are produced, there is no risk of chip-related issues, and the process creates an especially smooth workpiece surface. However, many materials are not suitable for thread forming. Additionally, this method cannot be used manually and requires special attention to cooling and lubrication due to the high heat generation.
You can easily meet your needs for cutting and non-cutting tools for thread production in the BAER online store. We offer taps and thread formers in perfect BAER quality, as well as many other products for your daily work. If you have any questions or problems, our customer service will be happy to assist you. You can reach us by phone or via our contact form.