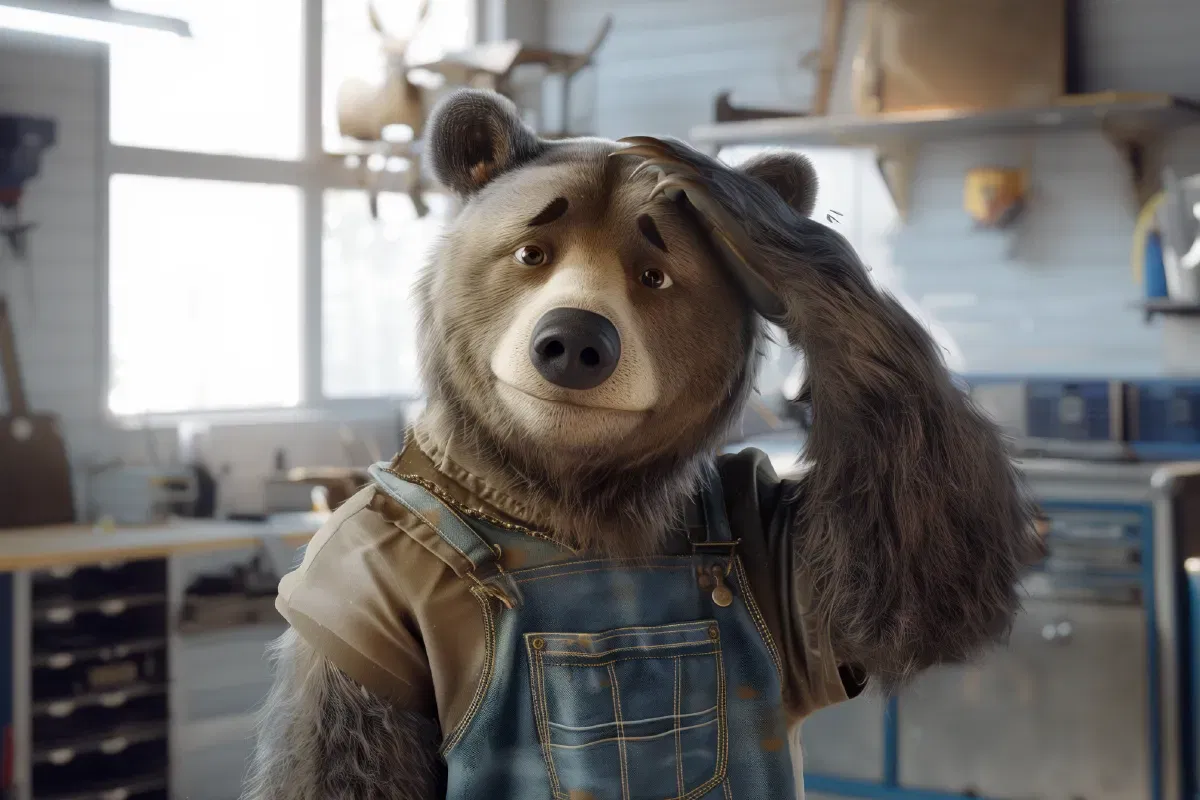
Thread Cutting Errors and How to Avoid Them
Do you ever have days where nothing seems to go right? Every tradesperson knows the frustration when things go wrong on the job. You’ve put in a lot of time and effort, only to end up with nothing. Even worse is when you can’t determine the cause of the issue — and you're tempted to give up the entire project.
Problems during thread cutting happen from time to time. After all, producing threads is a complex process, and beginners in particular often struggle. That’s why we’ve compiled the most common mistakes and explained how to handle them best. Keep reading to find out how to make sure your thread meets specifications after the work is done.
Common Thread Tapping Mistakes
If the thread fails or there's even a tool breakage, the root cause often lies in the same set of mistakes. The good news: with a few adjustments, these problems can usually be resolved easily.
Tap Doesn't Match the Application
There’s a reason why the range of taps is so extensive. The geometry and material of a tap determine which material and which application it’s suitable for — and the differences should not be underestimated.
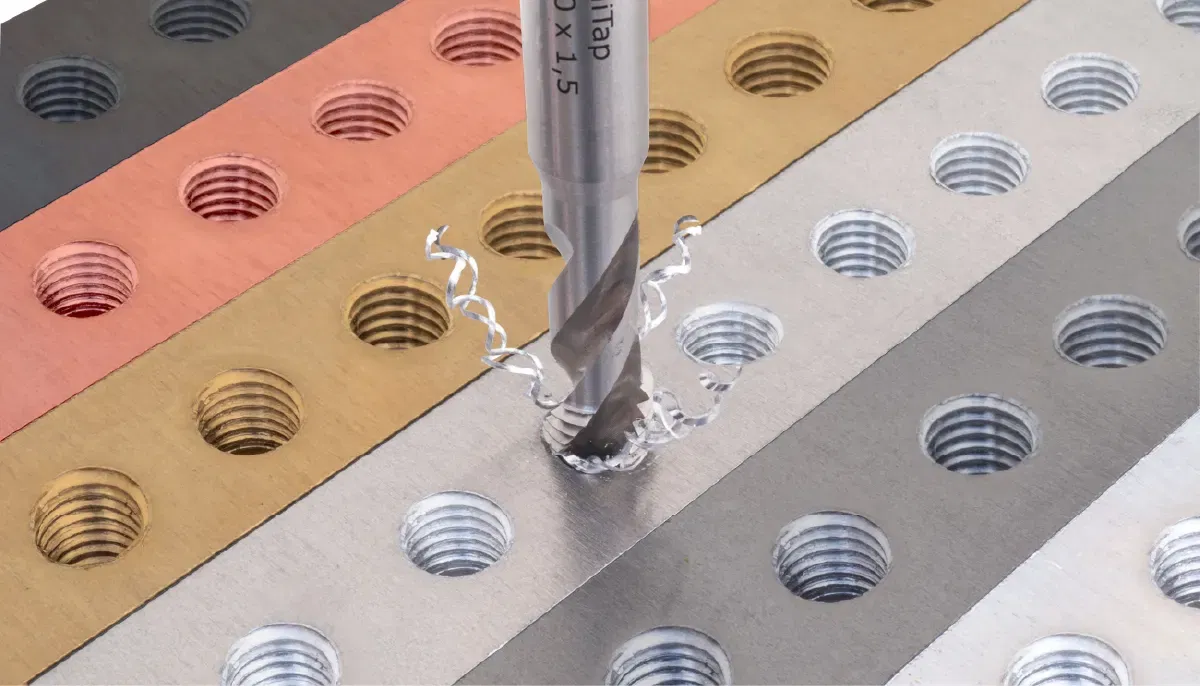
So when starting a new project, don’t just grab the first tool you find in your drawer. Take a moment to review the key specs. Are you working with aluminum or stainless steel? Is it a blind hole or a through hole? What kind of chips should you expect? What machines are available to you? The answers to these questions will guide you to the right tap.
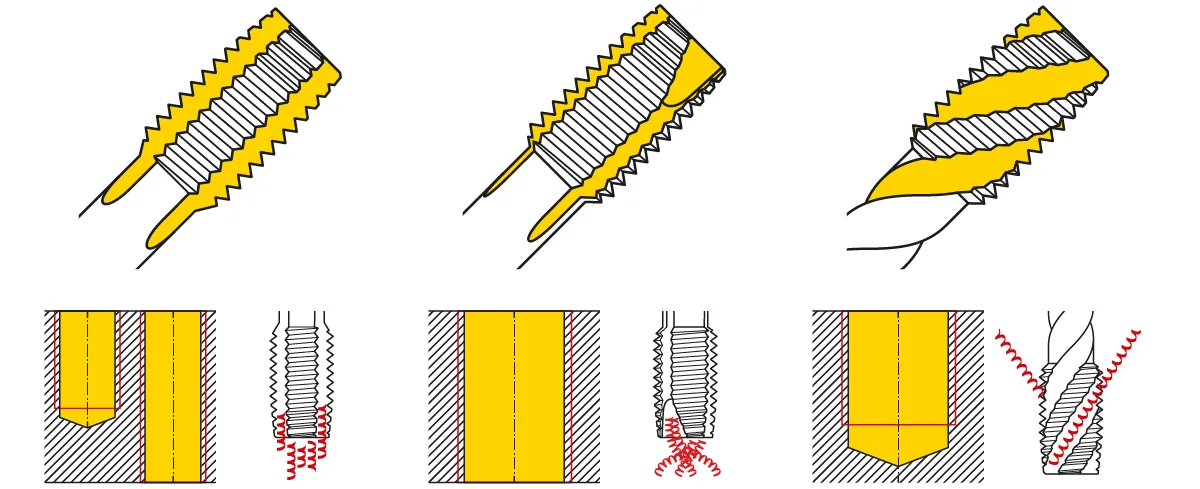
Incorrect Core Hole Diameter
The core or pre-drill diameter is one of the most important factors for a successful thread. Thread tapping is a cutting process, meaning material is removed. However, the cutting edges are only capable of creating threads on the walls of the pre-drilled hole — they cannot enlarge the hole itself. If the core hole is too small, the tap will get stuck, break, or the thread will end up with incorrect dimensions.
You can look up the correct diameter in tables or calculate it yourself. For threads with a 60° flank angle, it's easy — just subtract the pitch from the thread diameter.
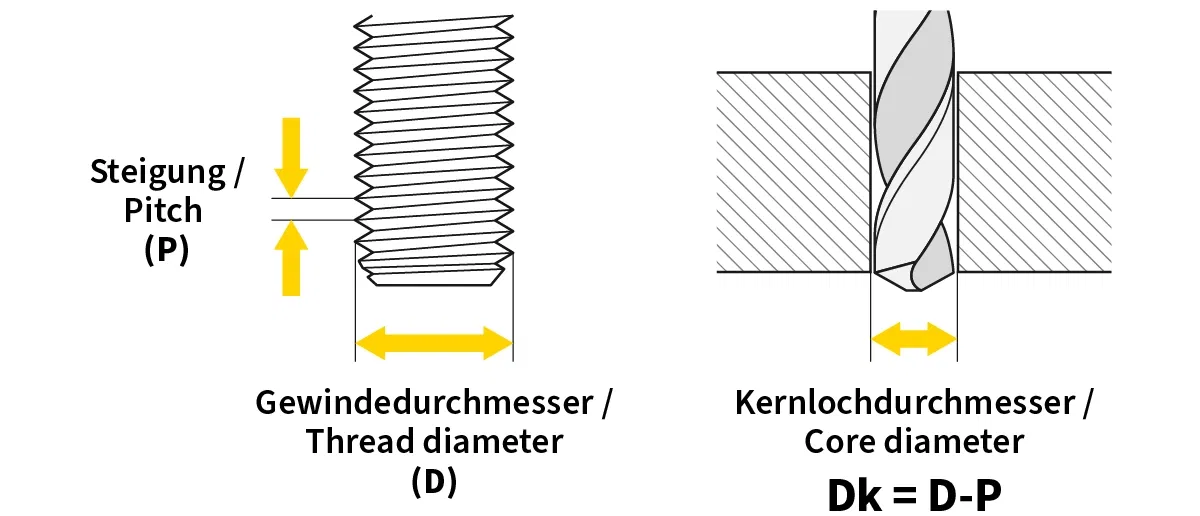
Incorrect Machine Settings
If unexpected problems arise during machining, it’s not always the tap’s fault. It’s worth double-checking the machine and especially its settings.
Cutting speed in particular often causes uncertainty, as the correct value depends on several factors. Once again, the decisive factor is the material you’re working with. In our online shop, you’ll find the recommended cutting speeds for each material listed with the respective product.
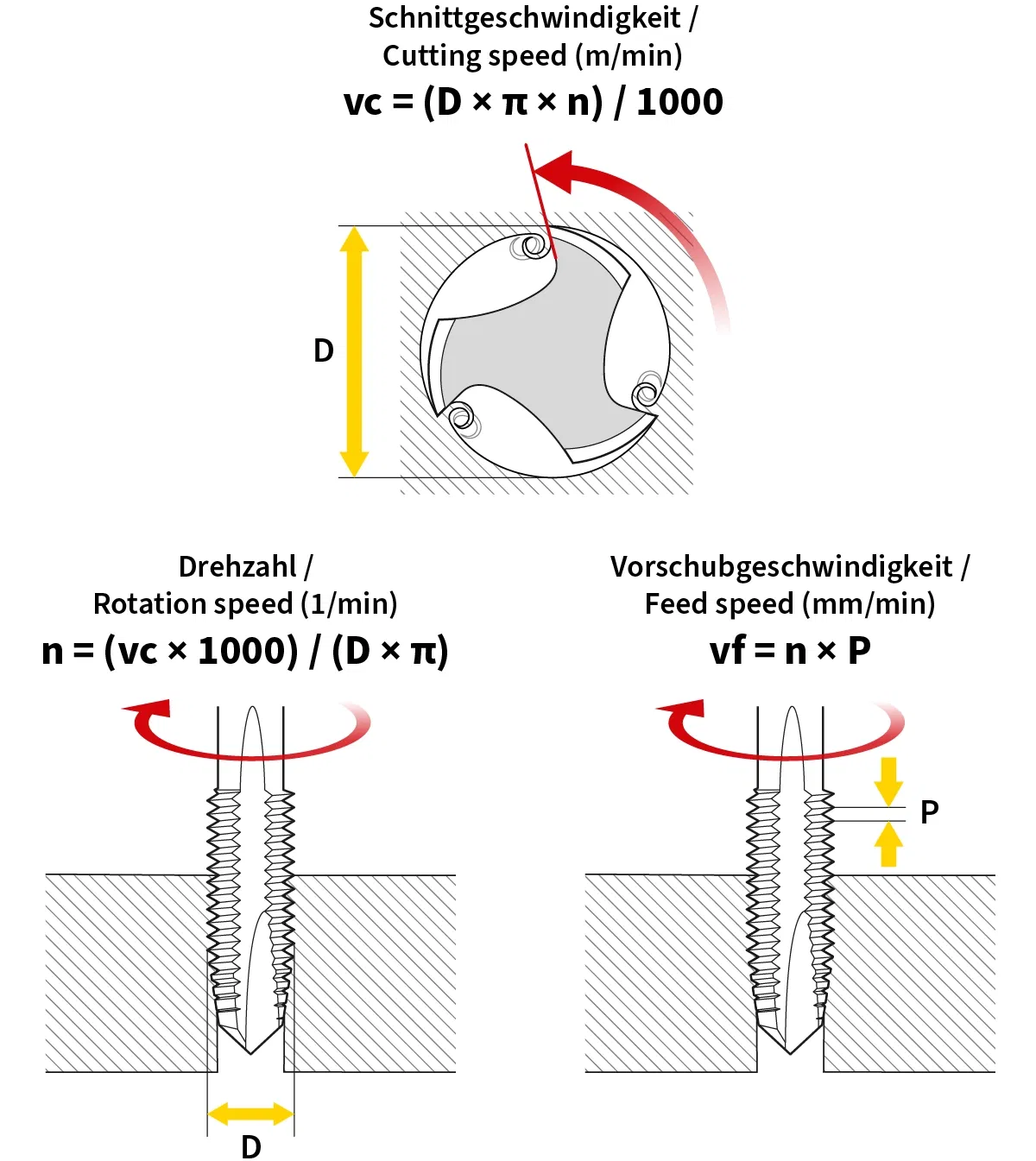
Issues can also arise in the machine's tool holder. A low-quality drill chuck with poor concentricity can negatively affect the quality of the finished thread.
Tool Is Not Held Straight
This point is especially important when threading by hand or using a handheld machine. In these cases, you can’t rely on a clamping device to keep the tool properly aligned. An incorrect angle when entering the core hole can quickly damage both the tap and the thread.
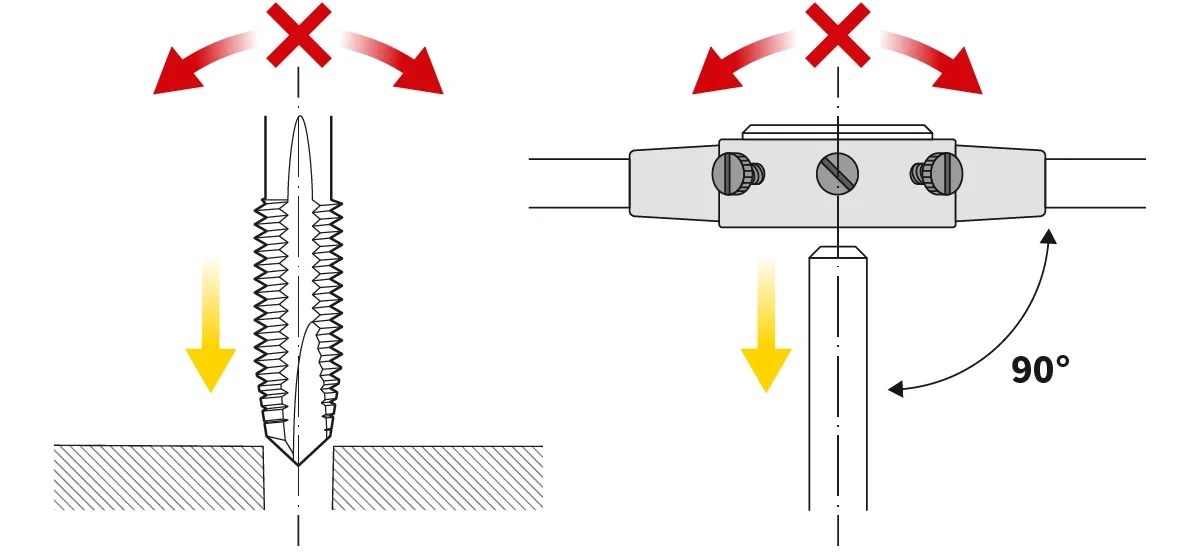
To prevent this, you can use an angle guide or other helpful tools to keep the tap aligned. When cutting external threads, die guides are particularly effective. Moving slowly and deliberately can also help reduce errors.
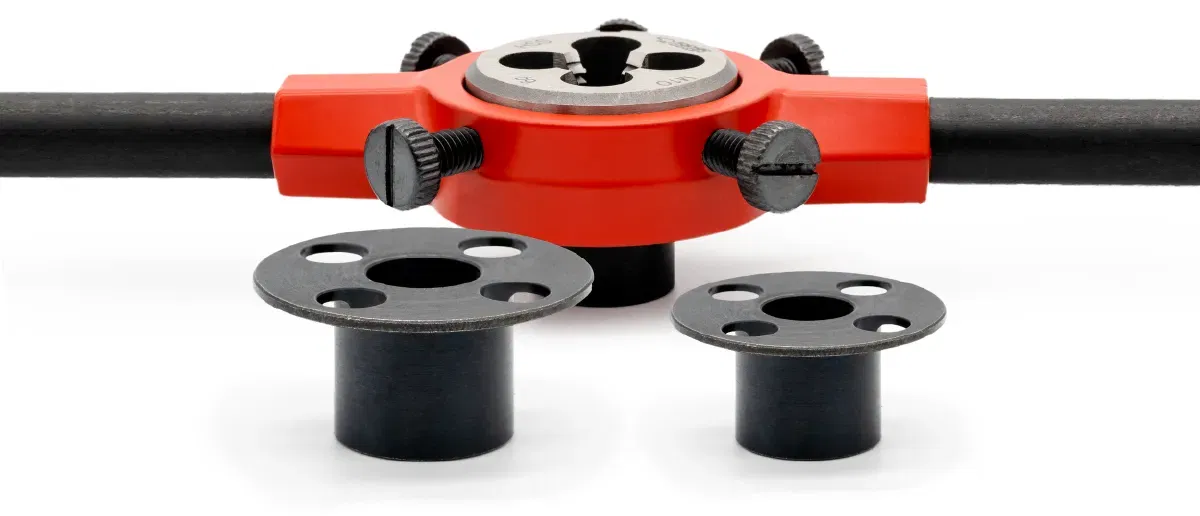
Wrong or Insufficient Lubrication
If friction during tapping becomes too high, it can affect both surface finish and tool life. So don’t neglect the use of lubricants. Make sure your chosen product is appropriate for the tapping operation and use it in sufficient quantity.
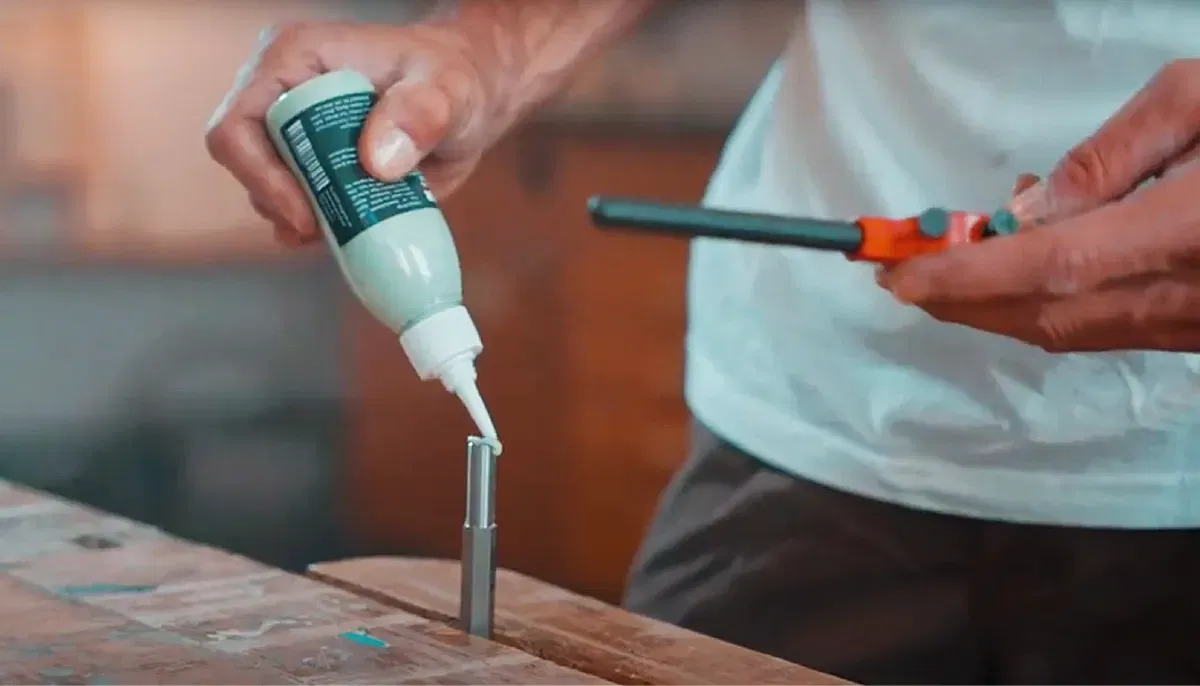
Quality Control in Thread Production
Threads are very complex structures and can become unusable due to even minor deviations. Any of the above issues can result in threads that don’t meet requirements or function as intended. That’s why regular quality control is essential — especially in industry.
Key parameters in the thread profile such as pitch, flank angle, and the precise formation of edges and transitions are examined at a microscopic level. This is done using high-tech sensors — or time-tested mechanical tools like thread gauges.
Verifying Dimensional Accuracy of Threads
If you're working with threads mostly as a hobby and not concerned with production efficiency, then quality control may seem less important. But even as a DIYer, you can benefit from occasionally checking your thread tolerances. It’s a good way to spot early signs of wear on your taps and identify root causes of common issues.
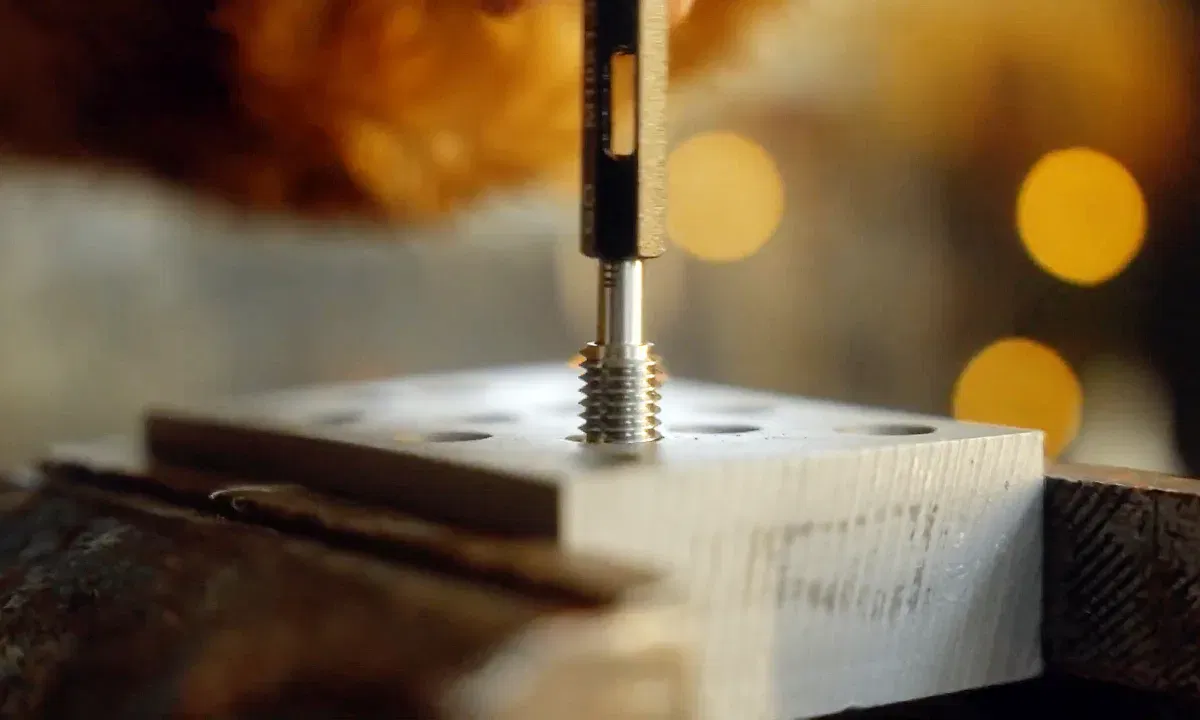
Just like in industrial settings, you can use thread gauges in your home workshop. These inspection tools help determine whether your threads are within the specified tolerances. You can identify the pitch using a thread pitch gauge, and the so-called light gap method allows you to detect deviations with the naked eye. And to determine the nominal diameter, a good old caliper will do the trick.
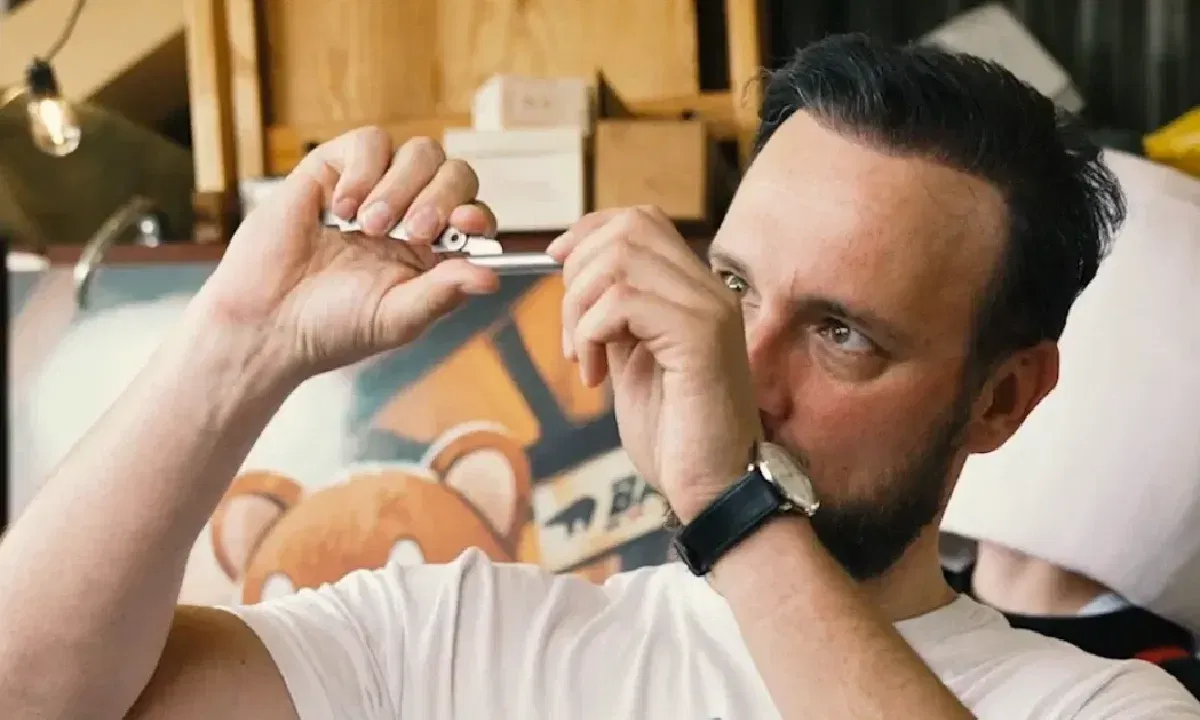
Avoiding mistakes starts with choosing the right tool. You’ll find high-quality taps for virtually every threading task in the BAER Online Shop. Feel free to get advice from our customer service. We’re available by phone or through our contact form anytime.