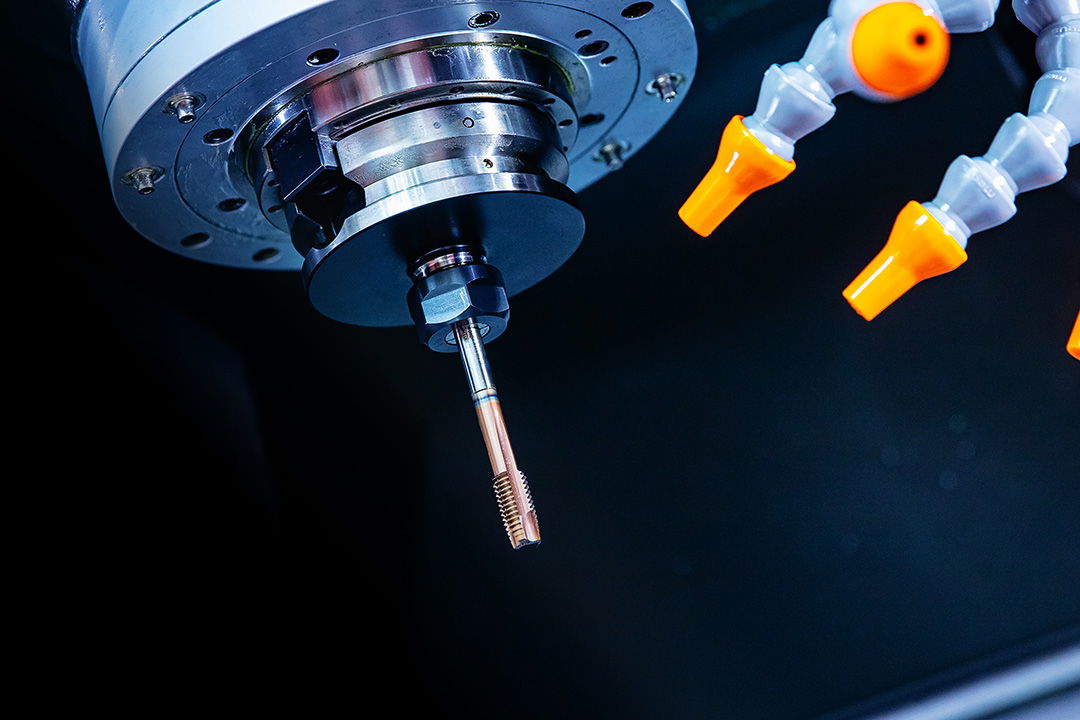
Thread cutting with the CNC machine
Automation is already a common method, as since the invention of the steam engine, humans have continuously tinkered to take as much work as possible off machines. But the savvy engineers of the 19th century surely couldn't have imagined thread cutting with a CNC machine, because in modern industrial processing, muscle power hardly plays a role anymore – instead, you need to use your brain.
You've probably noticed that specialized knowledge is required to program thread cutting for your CNC machine. While your basic knowledge of threads and mechanical processing helps, without technical understanding of the setting options, thread cutting on the CNC machine won't work. To ensure everything runs smoothly for you, we've compiled the most important tips on the subject.
What are the advantages of thread cutting with the CNC machine?
Creating a work plan and programming a machine might sound like a lot of effort when you could simply grab the thread cutter from your toolbox and do it yourself. But the CNC machine offers two decisive advantages: efficiency and precision. If you have to perform the same workflow many times, then thread cutting with a CNC machine, after programming it once, is unbeatably fast and accurate. But even for custom productions, thread cutting with the CNC machine offers a unique advantage because it is much more precise than a human could ever be. With thread cutting, the CNC machine only does exactly what you specify, so proper programming of CNC machines is crucial for optimal results.
This is how a CNC program for thread cutting is structured
The program for thread cutting with a CNC machine contains all the data that the machine needs to execute its work correctly. It consists of several sets, which in turn consist of words. These words, as the smallest unit, consist of an address letter, which determines the type of instruction, and a number, which further describes this instruction. The following words can be contained in a program set:
- N: Set number
- G: Path conditions
- X, Y, Z: Coordinates
- F: Feedrate
- S: Spindle speed
- T: Tool
- M: Auxiliary function
The exact program structure for CNC machines has its own standard with DIN 66025, so it is always the same regardless of the manufacturer.
Use the correct cycle for thread cutting with the CNC machine
In DIN 66025, nine fixed cycles are standardized and additional ones can be programmed additionally. These cycles include a fixed sequence of processing steps for frequently used functions. You specify the desired cycle to the control by specifying the path conditions, which are assigned the letter G. The cycle intended for thread cutting is designated as G84. When using a cycle for thread cutting with the CNC machine, you can save a lot of time and programming effort. Of course, this only works if the respective cycle also fits your workflow. For more specific cases, such as cutting a left-hand thread, you will need to make detailed adjustments again for thread cutting with the CNC machine.
Set important values correctly for thread cutting with the CNC machine
When using the thread tapping cycle G84 with the CNC machine, you also need to provide some additional information. Two values are the pivot points for successful thread cutting with the CNC machine: spindle speed and feedrate. We'll show you how to determine these two values correctly here.
What spindle speed do you need for thread cutting with the CNC machine?
In thread cutting with the CNC machine, the spindle speed is assigned the address S (for speed), it can be programmed by specifying a constant cutting speed in m/min or ft/min using the G96 path condition. We recommend setting the speed n by the G97 path condition. You can calculate the correct value based on the cutting speed using the following formula:
Spindle speed n [rpm] = (Cutting speed in m/min * 1000) / (Outer diameter * π)
Calculate the feedrate for thread cutting with the CNC machine
You program the feedrate with the address F (for feedrate). Using the G94 path condition, you can set the feedrate directly in mm/min or inch/min. The feedrate is calculated using the formula:
Feedrate = Spindle speed * Pitch
But beware, because this formula applies only to metric standard threads or fine threads. For inch threads, the number of threads per inch (TPI – "threads per inch") is usually defined instead of the pitch. The formula for calculating the feedrate is:
Feedrate = Spindle speed / TPI * 25.4
If you are using a CNC machine set to inches for thread cutting, you can use the following formulas based on the reverse principle:
- Feedrate = Spindle speed / TPI for inch taps
- Feedrate = Pitch * Spindle speed / 25.4 for metric taps
If you get decimal numbers in the feedrate calculations, always round to as many decimal places as your CNC machine can handle – the more accurate the input, the more precise the result at the end.
As a tap manufacturer, we are experts in threads – if you have any questions about thread cutting with your CNC machine, we are happy to help! Simply contact us via our contact form. And in the BAER online shop, you'll find a wide selection of taps for CNC machines and more.