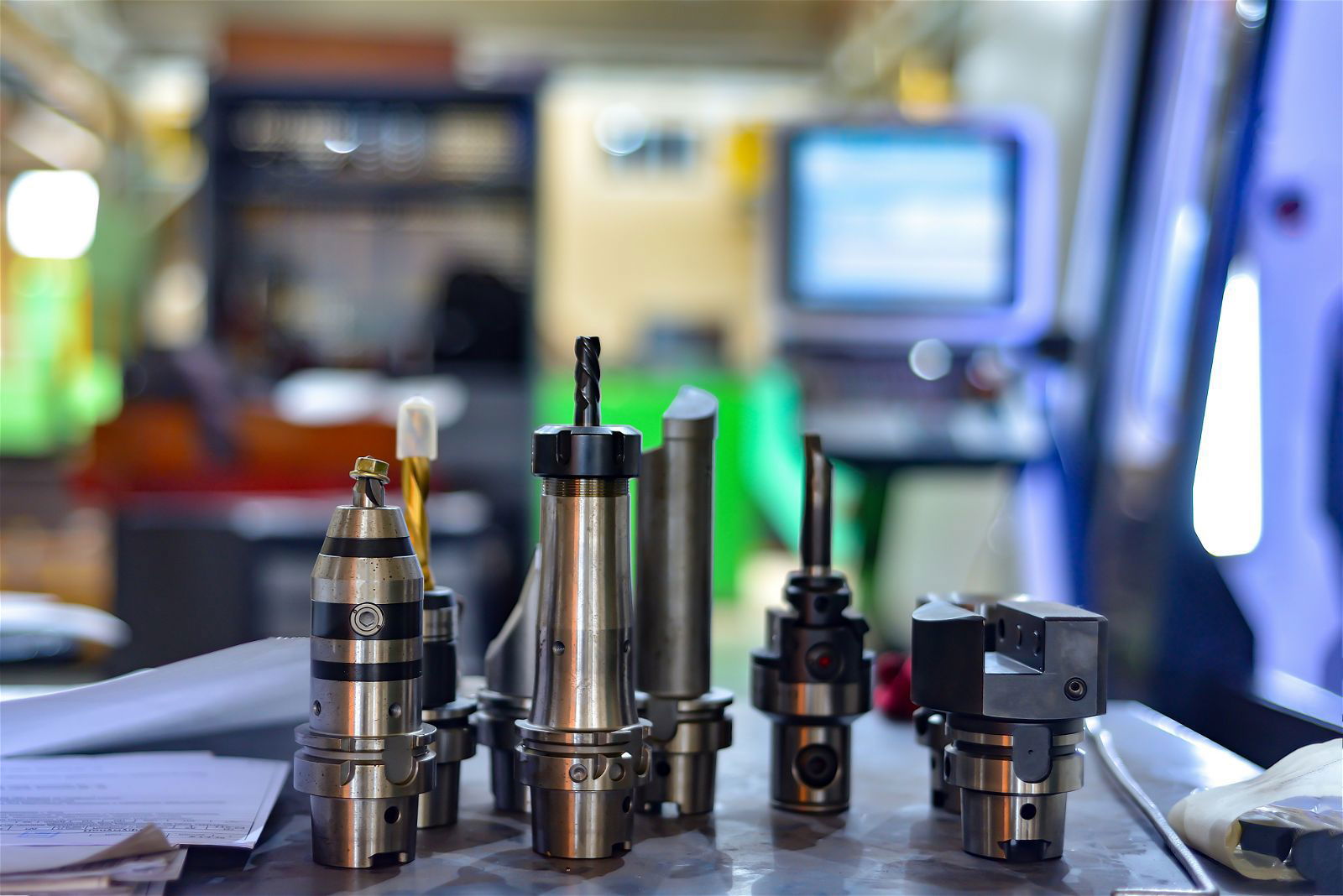
Thread milling: procedure and special features
It's no secret that thread cutting isn't the only method for thread production. Threads can also be turned, whirled, shaped, rolled, or even eroded. Our passion, of course, lies with the thread cutting, but looking beyond one's own horizons is always beneficial. Hence, let's delve into a method not mentioned in the above list: thread milling.
If you've worked with a thread cutting tool before, many aspects of thread milling will seem familiar. Both processes are chip-removing procedures, and the tools used share certain similarities. Nevertheless, thread milling operates on fundamentally different principles. Let's explore the unique features of this thread-production method and understand how it works.
Characteristics of Thread Milling
Several factors distinguish thread milling from other thread production techniques. We've listed some of the most notable ones for you.
Design of a Thread Mill
At first glance, you might confuse a conventional thread mill with a thread cutter. Both consist of a shaft and a head with grooves. But a closer look reveals that the milling part doesn't have a thread. Instead, a thread mill has profile grooves at the pitch's distance.
Thread Milling Requires a 3-Axis CNC Control
To produce a thread with the profile grooves of a thread mill, the machine's involvement is essential. The machine moves the thread mill in a helical motion within the drilled hole, carving out the thread from the material. The resulting thread diameter is larger than the tool itself. Precision is crucial: the movement must match the pitch to mill a clean thread. This is achievable only with a 3D-path-controlled CNC machine.
Thread Milling is Versatile
Owing to its design and unique principle, a thread mill is less restricted in its purpose compared to, for instance, a thread cutting tool. The same tool can cut both left-hand and right-hand threads, through-holes and blind holes, and external and internal threads. Depending on its type, a single tool can even produce different pitches and thread sizes. This means you need far fewer tools for milling threads.
Thread Milling Produces Comma-Shaped Chips
One major advantage of thread milling is the shape of the produced chips. Instead of lengthy spirals, the chips are small fragments, eliminating common chip issues and facilitating easy removal.
Thread Milling Accommodates Large Diameters
The design and application of a thread mill mean it's largely unconstrained by thread size. This allows the milling of even very large diameters, which would require massive tools if cut traditionally.
How to Produce Threads Using a Mill
The thread milling procedure varies based on the tool type used. There are options that can save multiple steps. For simplicity, we'll distinguish applications into thread milling with and without pre-drilling.
Thread Milling with a Core Hole
Some thread mills require a pre-drilled hole. Unlike with a thread cutting tool, there are no fixed formulas for the core hole diameter, as it can vary. The finished core hole is countersunk, and the thread mill is immersed to thread depth. Thread milling starts with a 180° lead-in helix. The thread is then milled through a helical motion, followed by a 180° lead-out helix. The thread mill finally exits the thread completely.
Another variation with a core hole is the so-called thread chamfer mill with chamfering stage. In this case, there's no need for a separate countersink; the thread mill performs this step during the milling process.
Drill Thread Milling
Another type of thread mill can operate without pre-drilling. This drill thread mill has a chamfering stage and a drilling tip. It drills its core hole and chamfers it. Thread milling then proceeds as with the non-drilling type.
Considerations for Thread Milling
Precision is paramount in thread milling. Even during pre-drilling, if it's done, a high level of positional and dimensional accuracy is essential. Moreover, the workpiece should be stably and vibration-free mounted, as close as possible to the milling point. This minimizes vibrations and consequent inaccuracies. The machine used must also exhibit high rotational accuracy.
Cutting speed and feed can be selected independently. However, with the feed rate, you need to work with adjusted values because of the circular movement between the cutter's edge and axis. Otherwise, the machine control might assume too high a speed, risking tool breakage.
The thread depths achievable with a thread mill are limited. Depending on the tool type, only depths about three times the diameter are possible. Moreover, with a small thread profile angle and coarse pitch, there can be deviations in the thread profile. This applies to thread norms like trapezoidal, buttress, or knuckle threads.
Is Thread Milling Suitable for Your Thread Production Needs?
Undoubtedly, given the right conditions, thread milling offers numerous advantages. However, if you're not involved in mass production or don't possess a well-equipped workshop, a simpler method might be more appropriate. Many DIY enthusiasts lack the machine for thread milling. Not everyone has a CNC machine in their garage, after all. Furthermore, the correct programming of a CNC machine is not always straightforward, even for professionals.
If you occasionally need to produce threads or require them for a specific project, the good old thread cutting tools might be a better fit. With the extensive range from screw tap manufacturer BAER, you're bound to find what you need. Plus, our customer service offers expert advice!