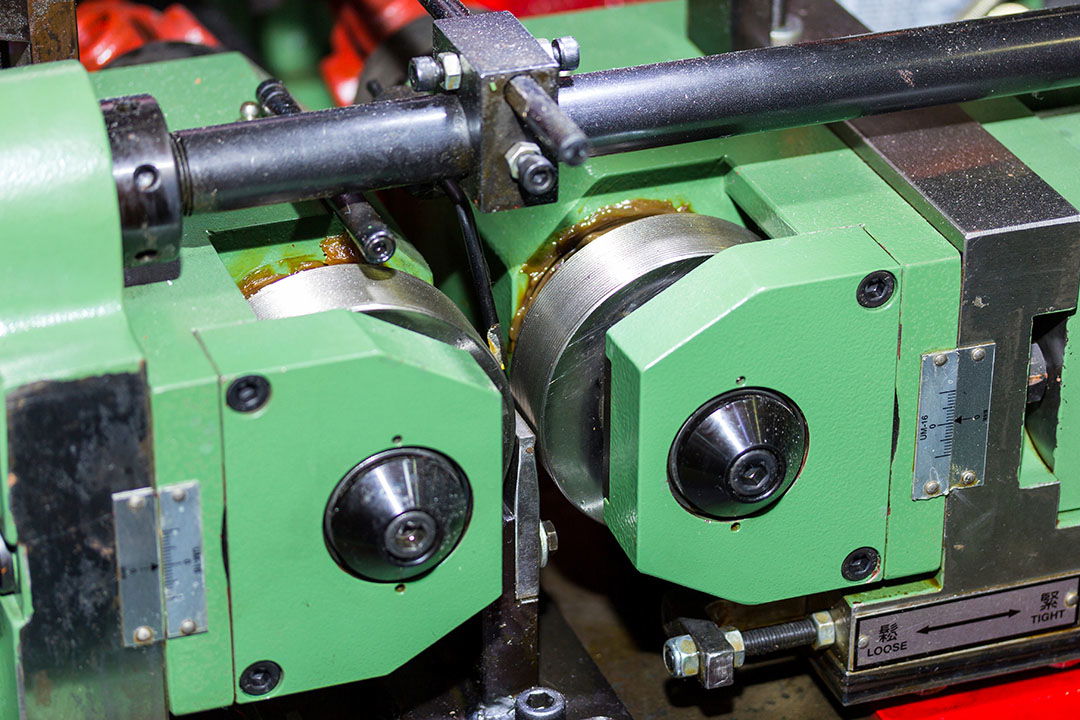
Thread rolling: chipless production of threads
Threads have been produced by humans for millennia, and over time, many different manufacturing processes have evolved. We don't want to withhold thread rolling from you, even though our hearts belong to thread cutting. Each method has its pros and cons and is particularly well-suited for certain industries or applications.
Today, let's focus on the chipless manufacturing process of thread rolling – also often referred to as thread forming. Both terms mean the same method, and in everyday language, thread rolling has prevailed over rolling. We'll explain what makes thread rolling special, how it works, and whether you should make room for a rolling machine in your workshop.
Thread Rolling is a Chipless Manufacturing Method
The central feature of thread rolling and the most important difference from thread cutting is that it is a chipless manufacturing method. Rolled threads are created by cold forming – meaning the desired thread profile is not formed by removing excess material, as in thread cutting. Instead, the material is displaced and shaped into the appropriate form, compressing the fibers in the material without cutting them. Consequently, no chips are generated during the thread rolling process.
Thread Rolling: Different Processes
There are several ways to generate a thread using thread rolling, and they all involve the use of rolling dies or thread rolling dies. These tools are round rollers with the profile that should be impressed on the workpiece. These rollers rotate and, through pressure, displace material into the indentations on the rollers, creating the thread peaks. Due to the high frictional forces involved, the correct use of lubricants is crucial for all rolling processes. The most common rolling methods include the plunge method and the through-feed method.
Thread Rolling in the Plunge Method
In thread rolling in the plunge method, the blank is placed between the open rolling dies. The rotating rolls move towards the blank and apply friction pressure to the workpiece, resulting in the thread profile being plunged into the workpiece by the rolls. In this type of thread rolling, only one thread length corresponding to the width of the rolling dies can be generated in one step. The advantage of this method is the very high accuracy of pitch and profile, and the processing is particularly fast.
Thread Rolling in the Through-Feed Method
In thread rolling in the through-feed method, the blank moves through the rolls instead of staying in place. The rolling dies for this method have three different areas: an entry cone, a calibration area, and an exit cone. With this method, long threaded rods can be produced, as the length of the rollable thread is only limited by the dimensions of the blank.
Advantages of Thread Rolling
Since the material fibers remain intact during forming, rolled threads often have a particularly high surface quality and are highly resistant to wear. The processing time per thread is very short, which is advantageous in mass production. Thread rolling is therefore frequently used in the industrial production of screws. Moreover, especially in industrial production, thread rolling can save a significant amount of raw material, as the blank is smaller than the finished workpiece – a thread cutter saves less raw material in comparison. Additionally, no chips are produced during thread rolling, which prevents chip problems and reduces the cleaning effort.
Challenges of Thread Rolling
More of a peculiarity than a problem is the fact that thread rolling cannot produce internal threads. Due to the special manufacturing process with the rolling dies, thread rolling is a method exclusively applied to external thread rolling.
Not every material is suitable for thread rolling, as the material must be easily cold-formable and have a high elongation at break. The elongation at break indicates how deformable a material is – it is given in percentage. Materials with 12% elongation at break or more are very well suited for thread rolling; below 12%, the load on the rolling dies increases, and with less than 8%, rolling does not yield good results. Many hardened steels, cast iron, titanium, or aluminum alloys cannot be processed by thread rolling due to their low elongation at break.
Another challenge of thread rolling is the desired thread profile. As you already know, the profile is created by pressing the material into the grooves of the thread rolling dies – this does not work equally well for all profile types. Sharp threads with a 60° or 55° flank angle, as found in most fastening screws, can be easily rolled. Slightly more complicated but still feasible are profiles of trapezoidal and saw threads, as long as they have sufficiently inclined flanks. Round threads, on the other hand, require very high rolling force to develop optimally during thread rolling. Thread rolling as a method completely fails for profiles with vertical flanks.
Is Thread Rolling a Good Alternative to Thread Cutting?
One thing is clear: if you only occasionally want to cut a thread in your DIY projects or in your professional workshop, you should definitely stick with thread taps and dies. While thread rolling has some advantages, they only come into play when it comes to mass-producing components. The significant cost and space requirements of a specialized rolling machine are likely to pay off on a smaller scale in only a few cases. If you still need a rolled external thread, it's better to consult a professional manufacturer.
In all other cases, you are better off with high-quality threading tools – as a thread tap manufacturer, we are happy to assist you with any questions. Take a look at our BAER online shop!