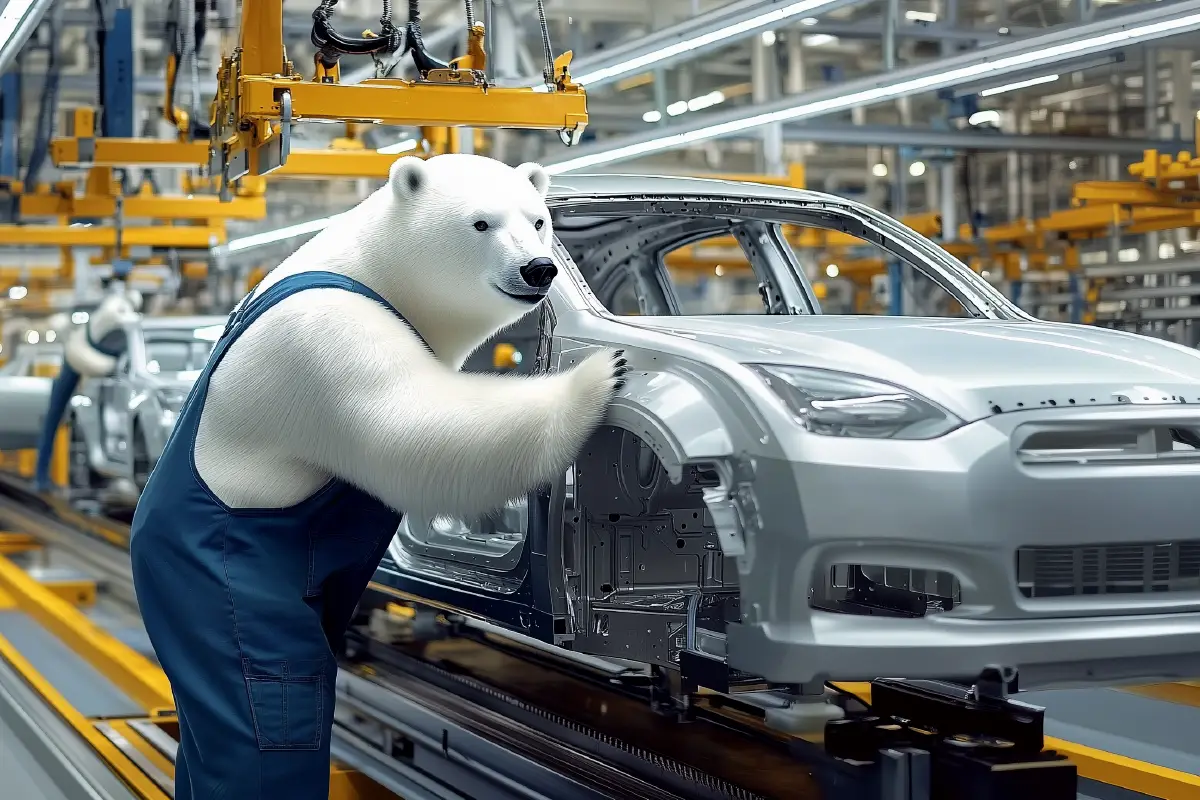
Threads for the Automotive Industry and Beyond: Specialty Threads for Various Sectors
Components such as screws, bolts, and nuts can always be placed somewhere along the spectrum between universal applicability and high specialization. For DIYers or craftsmen, it's obviously convenient to use the same thread for a wide range of projects. That way, you need fewer tools, your work becomes quicker and more routine, and you don’t have to constantly deal with new dimensions and thread types.
However, universal applicability always means that compromises are inevitable. And in many industries and companies, such compromises are unacceptable for safety reasons alone. That’s where specialty threads come into play, tailored precisely to a specific application. In this article, we’ll take a closer look at what that really means.
Why Do Certain Industries Need Specialty Threads at All?
Threaded connections are used worldwide and in all sectors as a simple and efficient way to join two components while still allowing them to be separated again. This means that the requirements for threads can vary enormously.
Stability and Durability
Whether it’s a car, a pacemaker, or a space shuttle – there are situations where the stability of a threaded connection is of utmost importance. One factor is the durability and service life of a thread. Often this relates to safety, but not always. In industrial manufacturing, the use of specialty threads may simply be driven by economic considerations.
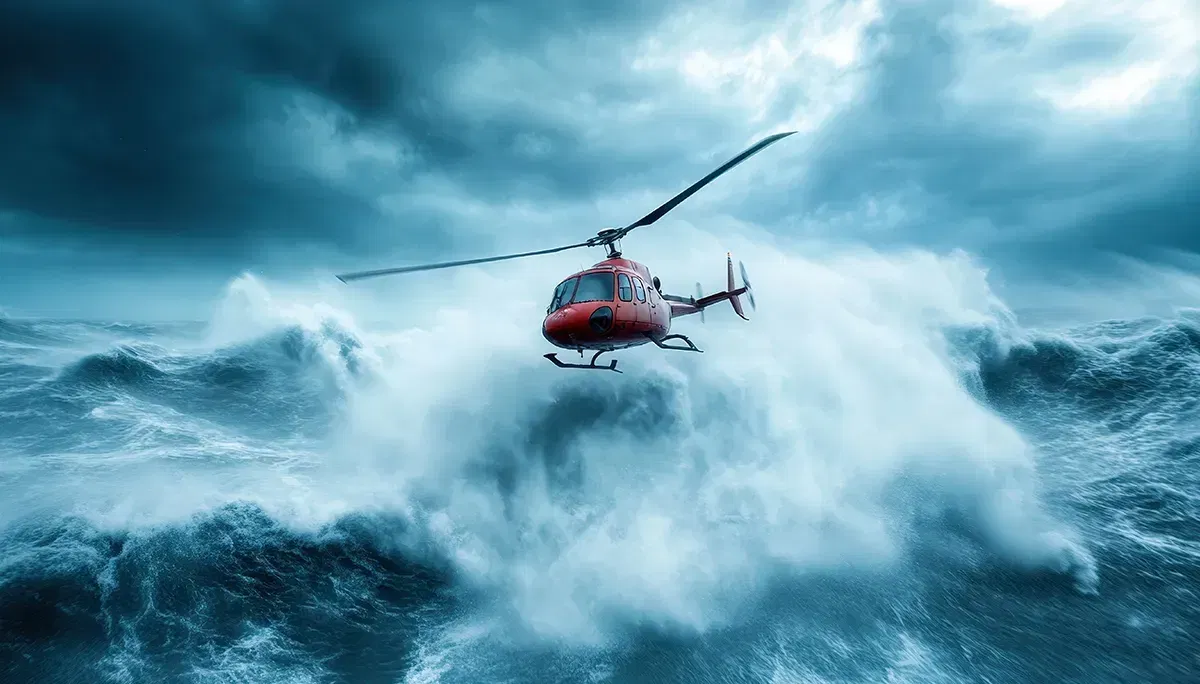
Industry-Specific Materials and Other Requirements
In addition, many sectors have specific requirements for thread production. In some industries, only very specific materials may be used for a product – and the thread must adapt accordingly. In other cases, chip evacuation must not cause contamination in sterile environments or interfere with sensitive mechanical systems. Sometimes it’s simply about the dimensions, especially when extremely small or large thread sizes are needed. In such cases, a specialty thread can be the solution.
Threads in the Automotive Industry: So Nothing Comes Loose
A very real-world use case for specialty threads is the automotive industry. Here, the safety of all road users is the central concern. Threads at the wheel, especially wheel nuts and bolts, must withstand significant stress while still being removable on a regular basis.
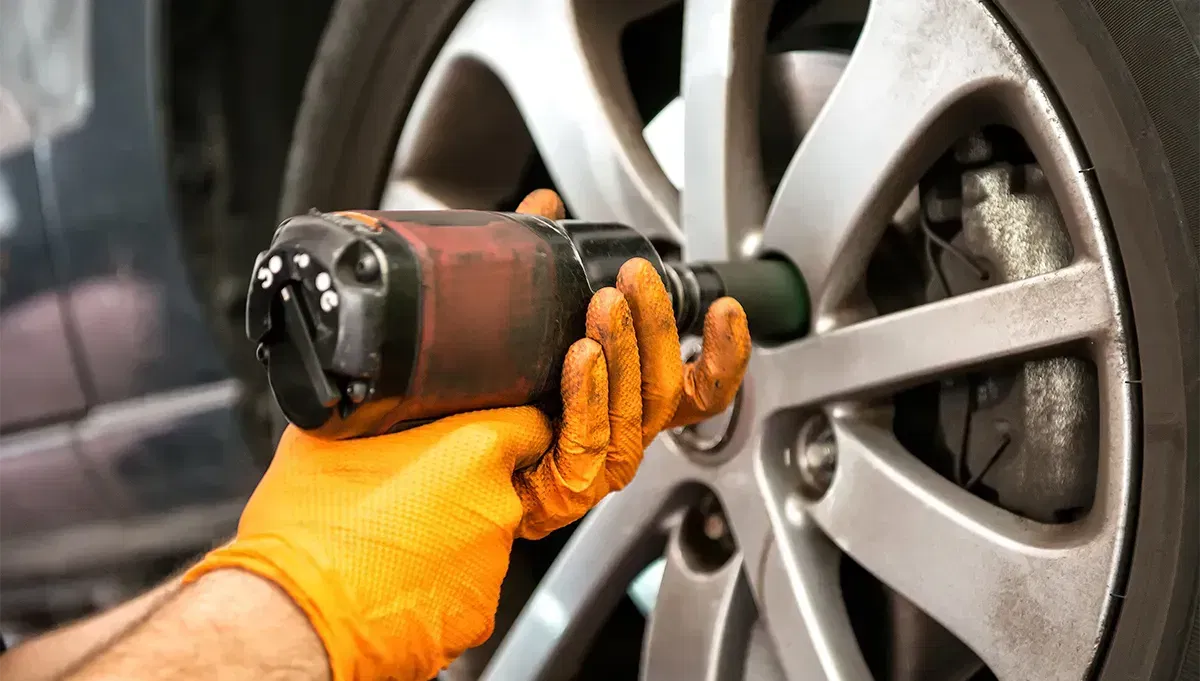
Fine Threads on the Wheel
In this high-vibration environment, fine threads are typically used because their self-locking feature prevents bolts from loosening unintentionally. On the other hand, fine threads are prone to rust and dirt, which often causes problems during tire changes. A good example of how specialty threads require balancing various factors.
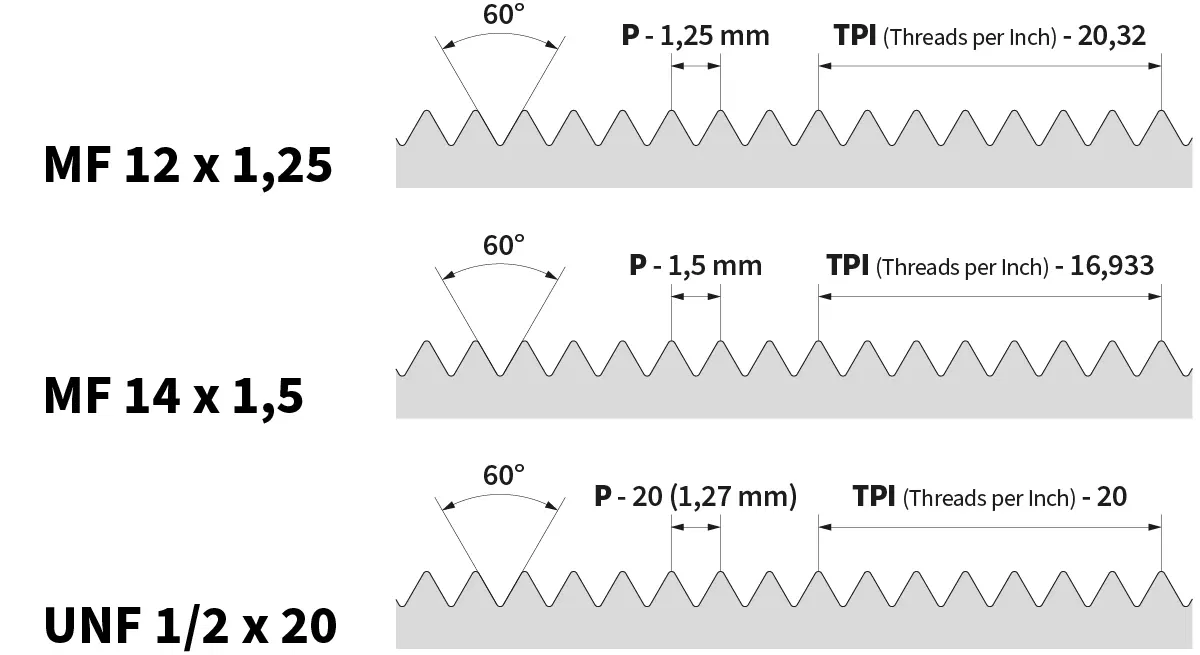
Other Threads on the Vehicle
Specialty threads are also used in other areas of the vehicle. For example, a spark plug thread is used to secure spark plugs in the cylinder head. The oil drain plug also features a special thread.
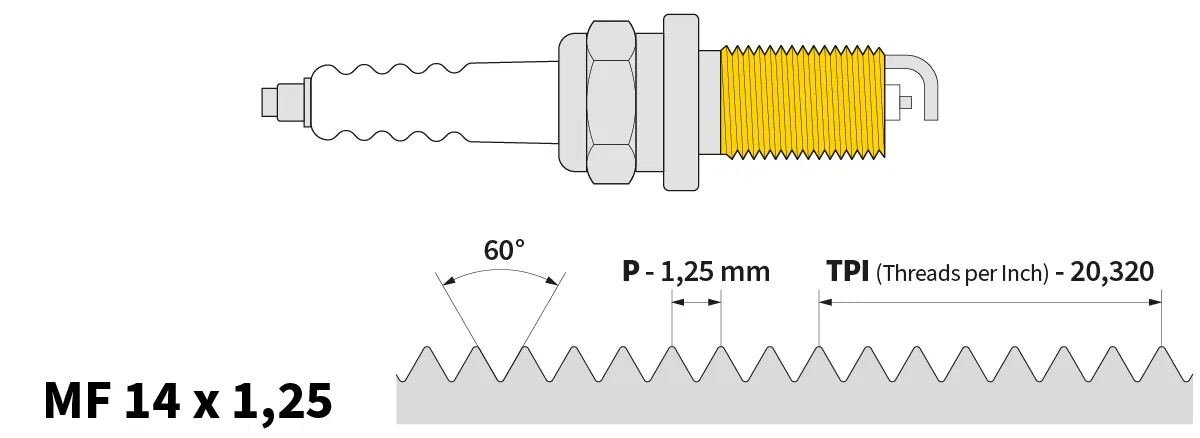
Life-Saving Precision: Threads in Medical Technology
Threads used in medical technology must meet a wide range of strict requirements. Screws in this field must be small and lightweight – yet still stable and durable. After all, every “repair” inside the human body involves significant effort.
Common Materials for Medical Threads
Materials used in medical technology also present a challenge. They must be biocompatible, non-allergenic, and robust. Titanium is often used for implants that remain permanently inside the human body.
Applications of Medical Threads
Threads are often used in dental implants. Thanks to modern techniques, new teeth can essentially be “screwed” into the jaw. In surgery, bone screws play an important role.
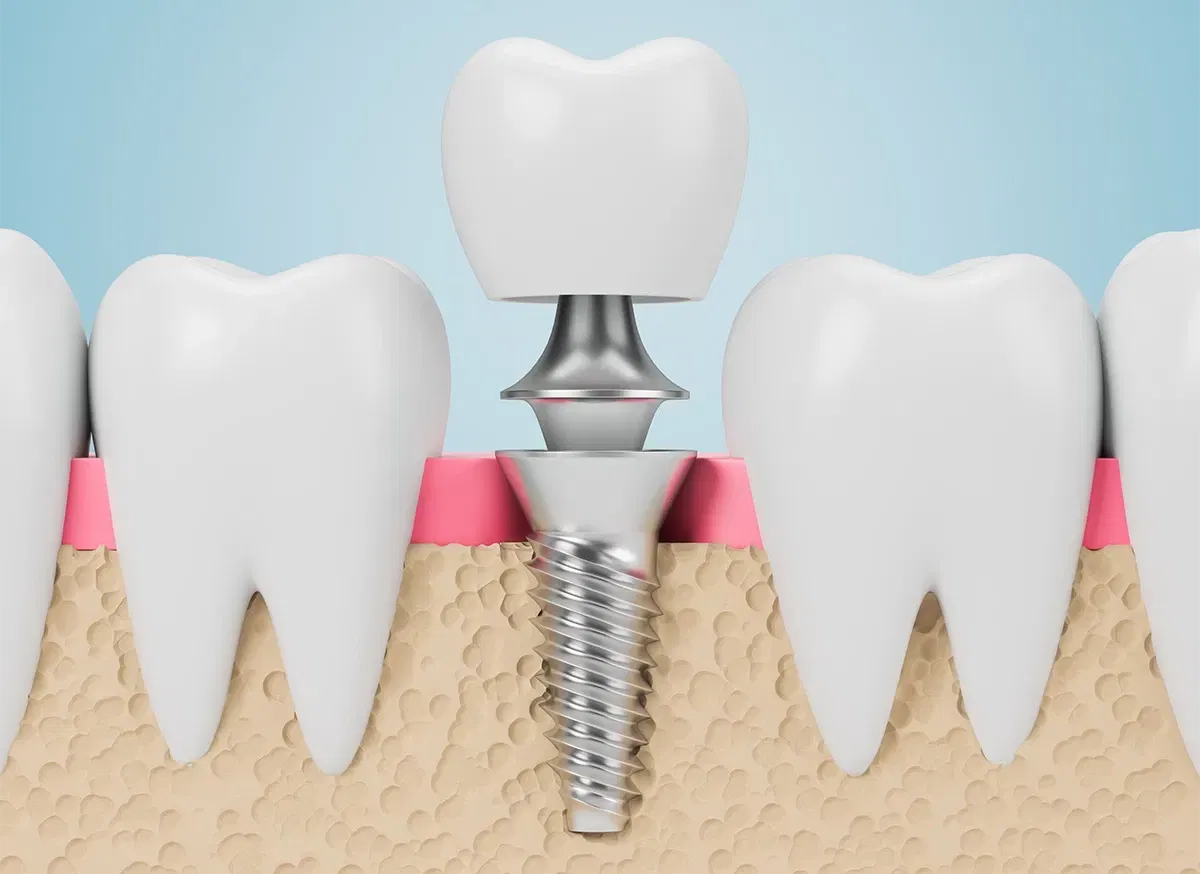
Aerospace: High-Strength Threaded Connections
In aerospace, when it comes to threads, there is absolutely no room for error. A single incorrectly installed screw could endanger dozens of lives. Moreover, the forces acting on threaded connections during takeoff and landing are far greater than those in an automobile.
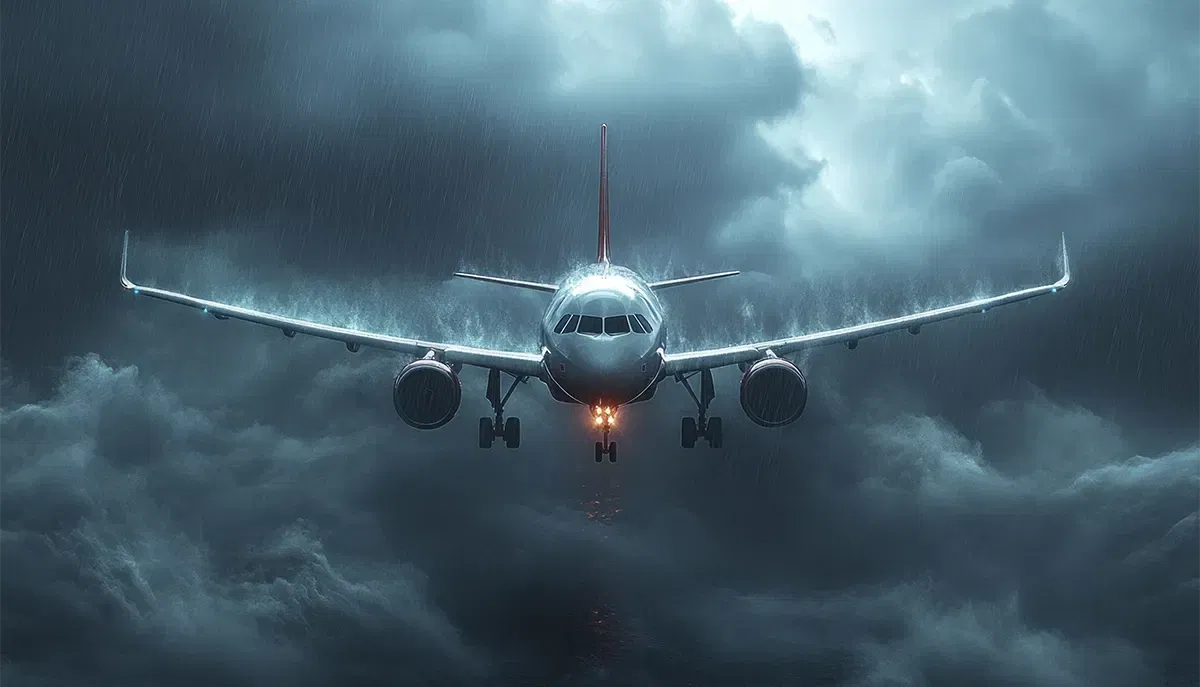
Thread Requirements in Aerospace
Additionally, rapidly changing environmental conditions must be considered. Between takeoff and reaching cruising altitude, threads must endure extreme temperature differences without losing stability.
Materials Used in Aircraft Construction
To save fuel, aircraft are often built using lightweight materials such as aluminum. However, these materials are often difficult to machine and generally lack high pull-out strength. All these factors must be taken into account when developing specialty threads for aerospace applications.
Thread Types Used
Aerospace has developed its own threading standards, known as J-threads: MJ, UNJC, and UNJF. These are variations of metric ISO threads (M) and American coarse and fine threads (UNC and UNF). The main difference is that J-threads are tighter in tolerance than the base versions. Other common thread types are also used in aerospace, such as the British Whitworth thread with a 55° flank angle or the metric trapezoidal thread.
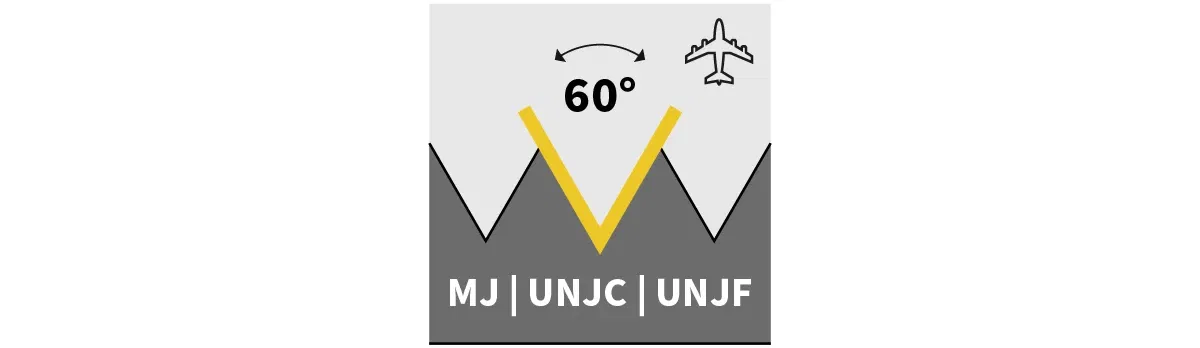
Whether you're looking for a versatile tool or a specialized solution – at BAER, you’ll find a wide range of taps, available individually or in sets, with excellent quality at unbeatable prices. Detailed usage information is provided in every product description. Our experienced customer service is also available to answer all your questions and concerns.