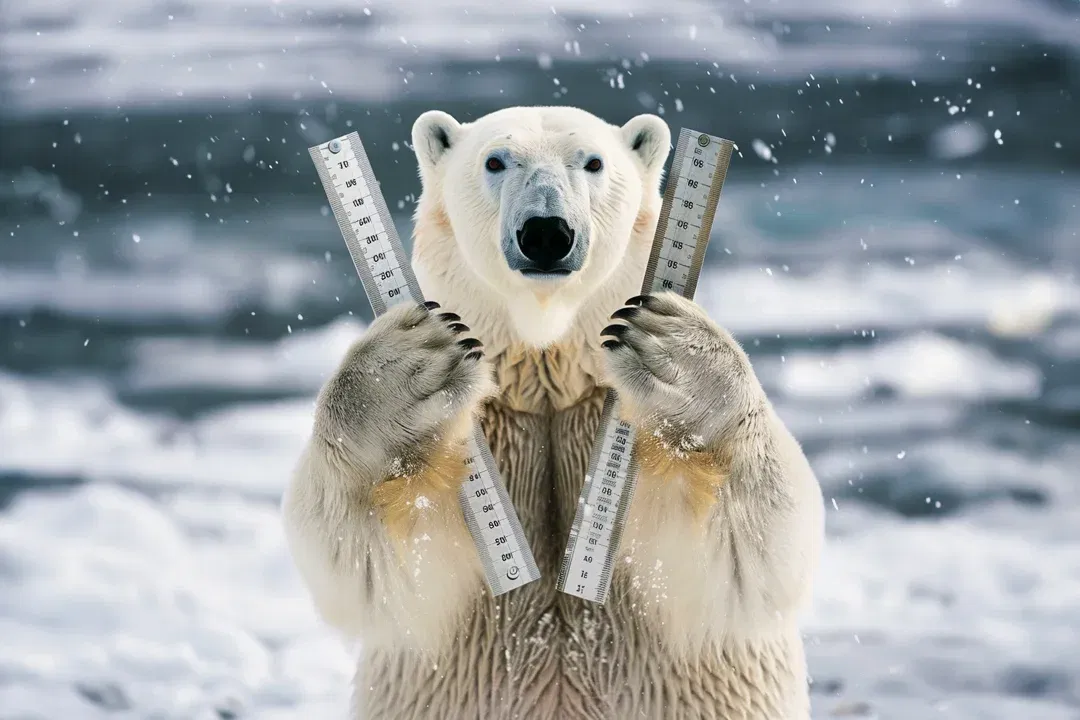
Everything you need to know about thread length
Imagine you have finally found the right tap for your cutting job, prepared the workpiece, carefully made all the settings on your machine and are ready to go. Ready to go, right? But wait, one variable may still be unclear. How far do you actually want to cut your thread into the hole? The question of thread length is often forgotten because - admittedly - it is not one of the most important in the DIY sector. However, this does not mean that you can simply ignore the thread length.
To understand exactly what forces act on a thread, what influences them and how this in turn is reflected in the required thread length, a degree in mechanical engineering is an advantage. But before you enrol at the nearest university, let's first try to break this complicated subject down into a few simple facts. This is sufficient for most private applications and provides an extra dose of stability and safety for your bolted joints. And you can never have enough of that, can you?
Thread length and usable thread length - what's the difference?
The section of the tap over which the threads are formed is referred to as the thread length. However, this is not the same as the thread length that you (can) produce with this tool. An important distinction must therefore be made at this point.
Let's start with the simpler case: You are cutting a thread in a through hole. Of course, there are many different possibilities here too, but in most situations the thread length will be determined by the thickness of the workpiece. After all, you cannot cut a thread where there is no material available. For through holes in sheet metal, metal plates and the like, the actual length of your thread in such cases is therefore smaller than the maximum thread length that the tap could produce.
Things get more complicated with a blind hole. As this ends in the material, the tap cannot exit at the other end. You therefore have to make a conscious decision regarding the thread length, which also determines the depth of your core hole. And this is where the difference between the thread length and the usable thread length becomes decisive. The usable thread length is always the smaller of the two values because you have to subtract the chamfer of the tap here. In this area, the threads are not fully developed and therefore do not count towards the length of the thread produced. The usable thread length for blind holes therefore corresponds to the thread length minus the chamfer.
What the screw-in depth has to do with the thread length
All well and good, but why is that so important? The thread length influences the minimum possible screw-in depth of a screw. And the screw-in depth is in turn an important value when it comes to the security of screw connections.
The screw-in depth describes the area in which the threads of the screw and nut threads overlap. It is usually specified as a multiple of the diameter. A screw-in depth of 1.5 d therefore corresponds to one and a half times the diameter. And this value must be large enough to be able to distribute the resulting stresses and loads sufficiently across all threads so that they do not tear out. Even if you still occasionally read that only the first three threads are load-bearing, it is actually the case that all threads have to bear a certain load. To prevent damage in these cases, sufficient threads must therefore be available.
In order to achieve the required screw-in depth, the thread length is of course a decisive factor. Where there are no threads, none can overlap and the screw connection may not be sufficiently tight. This can have far-reaching consequences, especially for safety-relevant connections.
This is what happens if the thread length is incorrect
And what is the correct thread length? This is where mechanical engineering studies come into play. In fact, the minimum screw-in depth and therefore the required thread length depends on several factors. These include the strength class, the thread diameter of the screw and the shear strength of the material into which the internal thread is cut. The intended use is of course also an important criterion, as the screw-in depth is particularly important under load.
Well, you might be thinking that the longer the thread, the better. But this is also a fallacy. In fact, the thread length should not be longer than necessary. If only because threads above a certain length are very difficult to produce and can cause problems when tapping. However, unnecessarily long thread lengths are also annoying during use, make assembly more difficult and promote negative effects such as jamming or seizing.
That's why the following applies when it comes to thread length: as much as necessary, as little as possible.
How to determine the required thread length
All right, and how much is needed? You can easily find screw-in depth tables on the Internet. Calculators are also available in which you can enter the dimensions and materials used and then receive a recommendation. Once again as a reminder: When working afterwards, pay attention to the actual usable thread length of your tap, especially for blind holes.
You should also be wary if the table or calculator shows you very high values for the screw-in depth. You should avoid thread lengths of more than three times the diameter. In such cases, it may make more sense to switch to other materials that provide reliable and stable screw connections even with a smaller thread length.
And once you have determined the correct thread length, take a look at our BAER online store and find the right tap for you. If you have any questions or problems, we are of course also there for you.