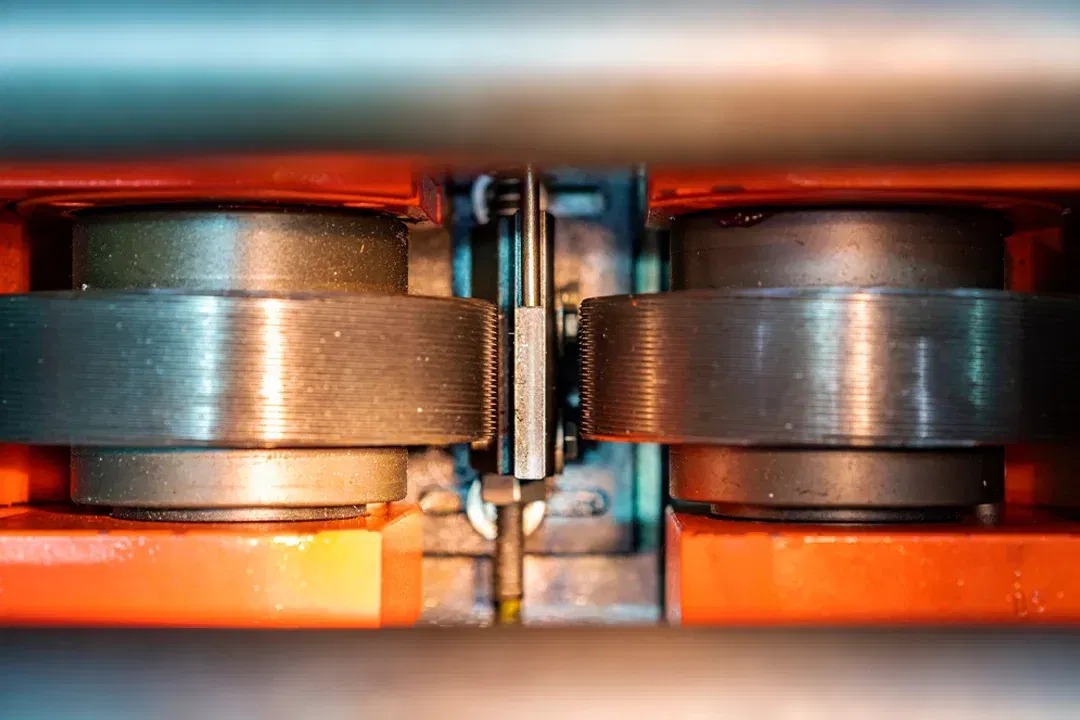
How are threaded spindles actually manufactured?
There are people who simply accept the existence of certain components as if they had fallen from the sky. And there are others who want to know everything in detail. Which of these two groups do you belong to? We're guessing the latter, otherwise you wouldn't be reading this article. Today we are looking at the question of how threaded spindles are manufactured.
External threads on bolts - a clear case for a die, you think? In this case, you are welcome to try it out and let us know your results. In most cases, threaded spindles are really long components. You won't get very far with a die or you will have to bring a lot of time with you. Other methods must therefore be used to provide the threaded spindle with its intended external thread. Which machines can cope with the oversize? And what are the advantages and disadvantages of the different ways of producing threaded spindles? Let's find out!
What threaded spindles are used for
Before we take a look at how they are made, let's briefly explain what a threaded spindle actually is. Basically, a threaded spindle is a threaded rod, i.e. a long rod with a thread along its entire length. However, a threaded spindle is a special category of threaded rod because its thread is a moving thread. The threaded spindle is used in machines of all kinds to transmit movements. The spindle rotates around its own axis and moves the spindle nut back and forth via the thread. Two different processes are used to manufacture such threaded spindles: thread rolling and thread whirling.
Producing threaded spindles using thread rolling
Thread rolling, also known as thread whirling, is a popular method of producing threaded spindles. The blank is pushed through the middle between two rotating rollers, which are provided with the desired profile. In this way, the thread is pressed into the material in a chipless process. The material fibers are not severed in this process, but only compressed.
Thread rolling can be used to produce threaded spindles of almost any length. However, the material must be suitable for cold forming and the thread must not have too complicated a profile. In addition, enormous frictional forces are generated during non-cutting machining, so it must always be properly lubricated and cooled.
Producing threaded spindles by thread whirling
A special tool called a whirling ring is used for thread whirling. It is equipped with sharp indexable inserts on the inside. The process itself is similar to thread milling. As the blank moves through the ring, it rotates at high speed and cuts the thread into the bar. This is a machining process for the production of threaded spindles that can be used for many different thread types and materials.
What are the differences between the two methods for manufacturing threaded spindles?
The two processes for manufacturing threaded spindles differ significantly from each other in a number of respects, and this is also reflected in the results. Three factors stand out in particular:
Machining or non-cutting threaded spindles
The biggest difference is that thread rolling is a non-cutting process, whereas thread whirling is a cutting process. In non-cutting production, no material is removed, which means that no chips are produced and the material fibers remain intact. Threaded spindles produced in this way have a high surface quality and are less susceptible to wear. The absence of chips also prevents frequently occurring chip problems and reduces the amount of cleaning required.
Efficiency in the production of threaded spindles
The chipless process for manufacturing threaded spindles also has another advantage, as the amount of material required is lower. Of course, this only really comes into play in mass production and not with a few individual threaded spindles. Thread rolling also scores highly in terms of speed, as large quantities of threaded spindles can be produced quickly using this process.
Stay flexible when producing threaded spindles
However, thread whirling has a lot to offer compared to efficient thread rolling. This process enables the production of particularly precise threads and can also be perfectly adapted to special requirements. The whirling rings are very flexible tools that produce special geometries and can machine a wide range of materials. This is why thread whirling is often used when thread rolling has reached its limits.
Which process is better suited to producing threaded spindles?
A clear picture emerges from the differences and influencing factors described above. Thread rolling is particularly suitable for standard applications in mass production. There it delivers fast and good results, ensures optimum efficiency and a high surface quality, which in turn has a positive effect on the service life of the threaded spindle. However, there are also applications where thread rolling cannot be used due to the material used or the desired thread geometry. These special cases can then be machined reliably and precisely using thread whirling.
Can you produce thread spindles yourself?
If you've got the urge to produce a threaded spindle yourself, you're in for a sobering experience. The manufacture of threaded spindles is something for professionals in the industry. Mainly because you need large machines and special tools to make a threaded spindle. For domestic use, it is better to use prefabricated components. And for smaller jobs where you need to produce an external thread, the good old tap will often do the trick.
You can also find dies, taps and more in our online store at BAER. Our customer service team is also always on hand to answer your questions and provide you with all the important information about threading tools.