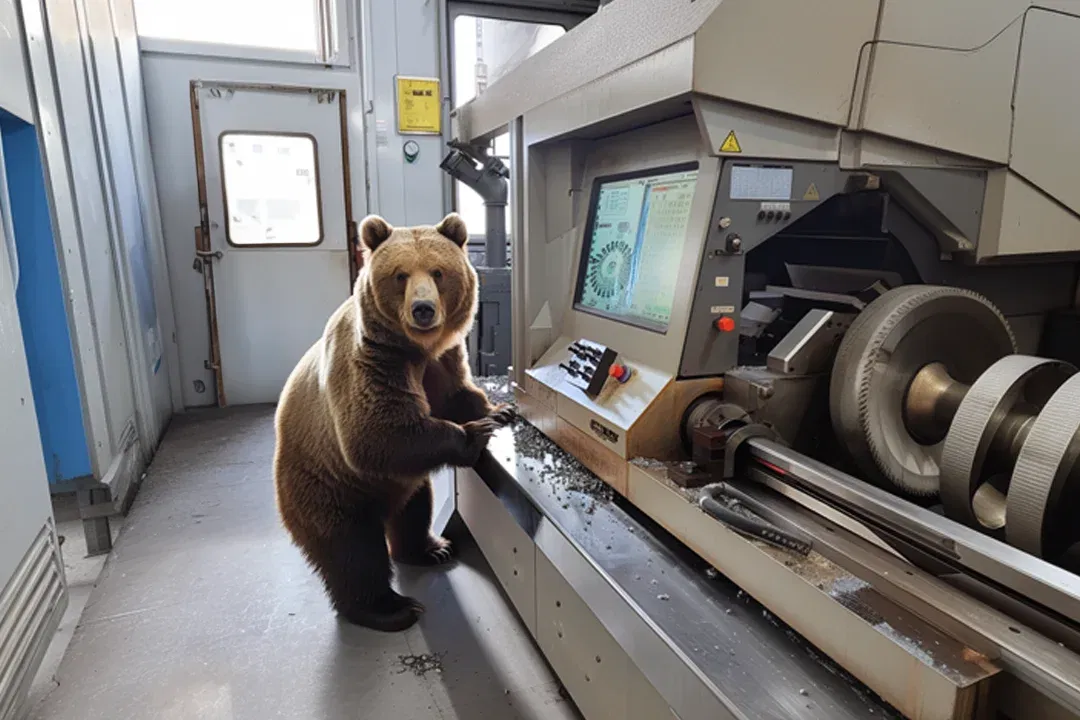
These thread production methods are available
Threads are irreplaceable in almost all areas of our lives and come in all conceivable shapes and dimensions. It is therefore logical that there is not just one single process for producing threads. You are probably most familiar with tapping, but did you know how many other methods can lead to the perfect thread? We have compiled an overview of all thread production methods and provide tips on which is best suited to your purpose.
Machining processes for thread production
Thread production processes can be divided into two groups and the larger of the two includes the machining processes for thread production. What all these methods have in common is the fact that they produce threads by removing material. This can be recognized by the fact that chips are produced during the work.
Tapping
When tapping, a core hole must first be prepared. A tap is then used, the shape and material of which must be matched to the respective cutting case. This cuts the desired thread into the material. Tapping is a flexible process for thread production and can be carried out both by hand and by machine. External threads are produced with the aid of a die.
Thread milling
A thread milling cutter has a milling part with profile grooves at the desired pitch. In a CNC machine, it is moved along the walls of the drilled hole in a helical motion, thus milling the thread into the material. In this way, the same thread milling cutter can produce both external and internal threads and also create flexible diameters. A thread milling cutter can also drill its own core hole.
Thread whirling
Thread whirling is a process for producing external threads that works in a very similar way to thread milling. Unlike milling, however, a ring is used here that rotates around a bolt and mills the thread into the material using inward-facing indexable inserts. This produces very precise and high-quality threads, such as those required in medical technology or for particularly small components.
Thread turning
Thread turning is a thread production process that can be carried out on a lathe. A profile tool with a suitable angle is used, which in the case of the metric standard thread is around 60°. For large threads, the process may have to be repeated several times to achieve the required thread depth. Thread milling is therefore a very flexible method, but requires good knowledge of how to use a lathe.
Thread grinding
Special grinding wheels with a profile are used for thread grinding in order to remove material in a targeted manner and thus produce the desired thread. The whole process takes place on cylindrical grinding machines, on which the bolt is mounted and then machined by the rotating grinding wheel. This process is often used for the production of threading tools.
Forming processes for thread production
In addition to the machining processes, there are also forming processes for thread production. In this process, the material is not removed but displaced. The material fibers are not severed in this way and no chips are produced.
Thread forming
This process is similar to tapping. First, a hole with the required diameter must be prepared, then the tool is screwed in. On its way, the tapping tool displaces material and thus presses the desired thread into the material. It has no cutting edges and as no chips are produced, a thread tap does not require deep grooves, but can have lubrication grooves for better distribution of the lubricant.
Thread rolling
The second method for chipless thread production is thread rolling. Rolling rolls with the desired profile are required for this process. The bolt either passes between these rollers or the rollers approach the stationary bolt from the side. In both cases, the profile is pressed into the workpiece by the rollers, creating the desired thread.
Eroding - an abrasive process for thread production
Finally, let's take a look at eroding as an option for thread production that cannot be categorized in either of the other two groups. EDM is the removal of material by means of electrical discharge processes. The workpiece is placed in a non-conductive liquid together with a live electrode. The workpiece and electrode do not touch each other, so sparks are created between the two, creating indentations. It sounds complicated, but in fact very complex shapes can be created in this way. However, eroding is also an expensive process that can only be carried out correctly with a great deal of experience.
Which thread production process is best for you?
So, now you know all the methods used to produce threads today. The question remains, which one is the best? Each of the methods presented has its advantages and disadvantages and, accordingly, also its own special areas in which it can play to its strengths. As you read on, you will have noticed that most of the methods require at least advanced workshop equipment and even expensive special machines that are only really worth buying on an industrial scale.
Of course, as big fans of tapping, we may be a little biased. But the truth is that tapping is the best solution for domestic use and for many hobby and craft applications, because you simply always remain flexible. Tapping even works by hand - try it with thread rolling or eroding. So as long as you don't want to go into series production, you are always well served with taps.
To find the right tool to make your project a perfect success, take a look at our BAER online store!