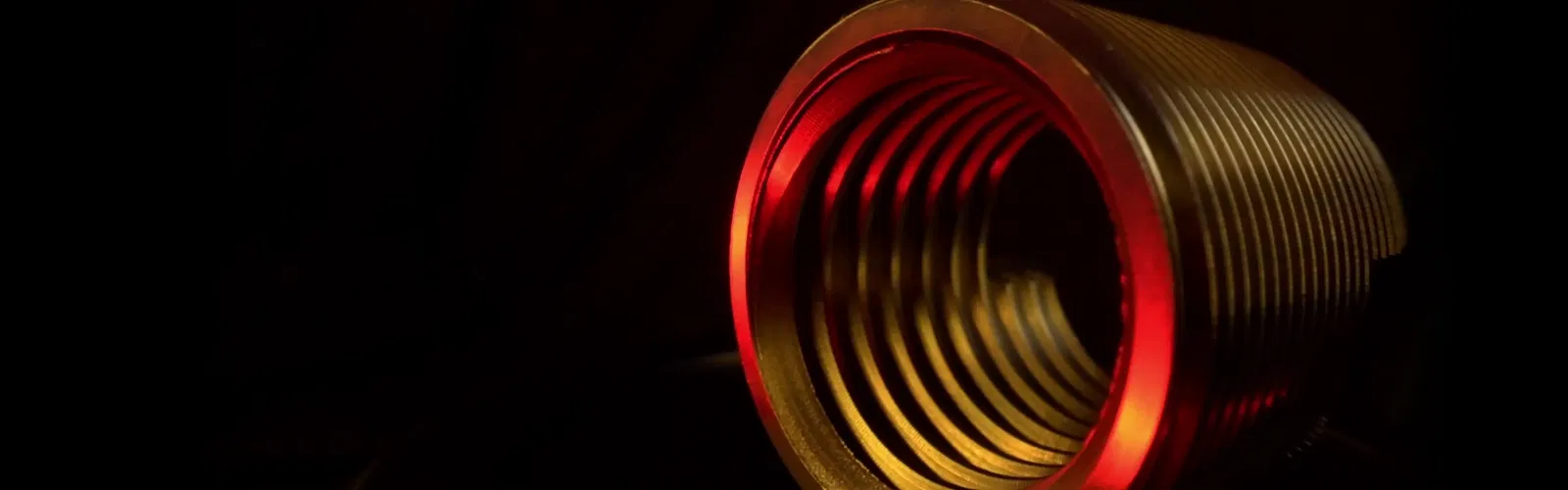
BaerCoil® and BaerFix®
Thread reinforcement and
thread repair
BaerCoil® and BaerFix® Thread reinforcement and thread repair
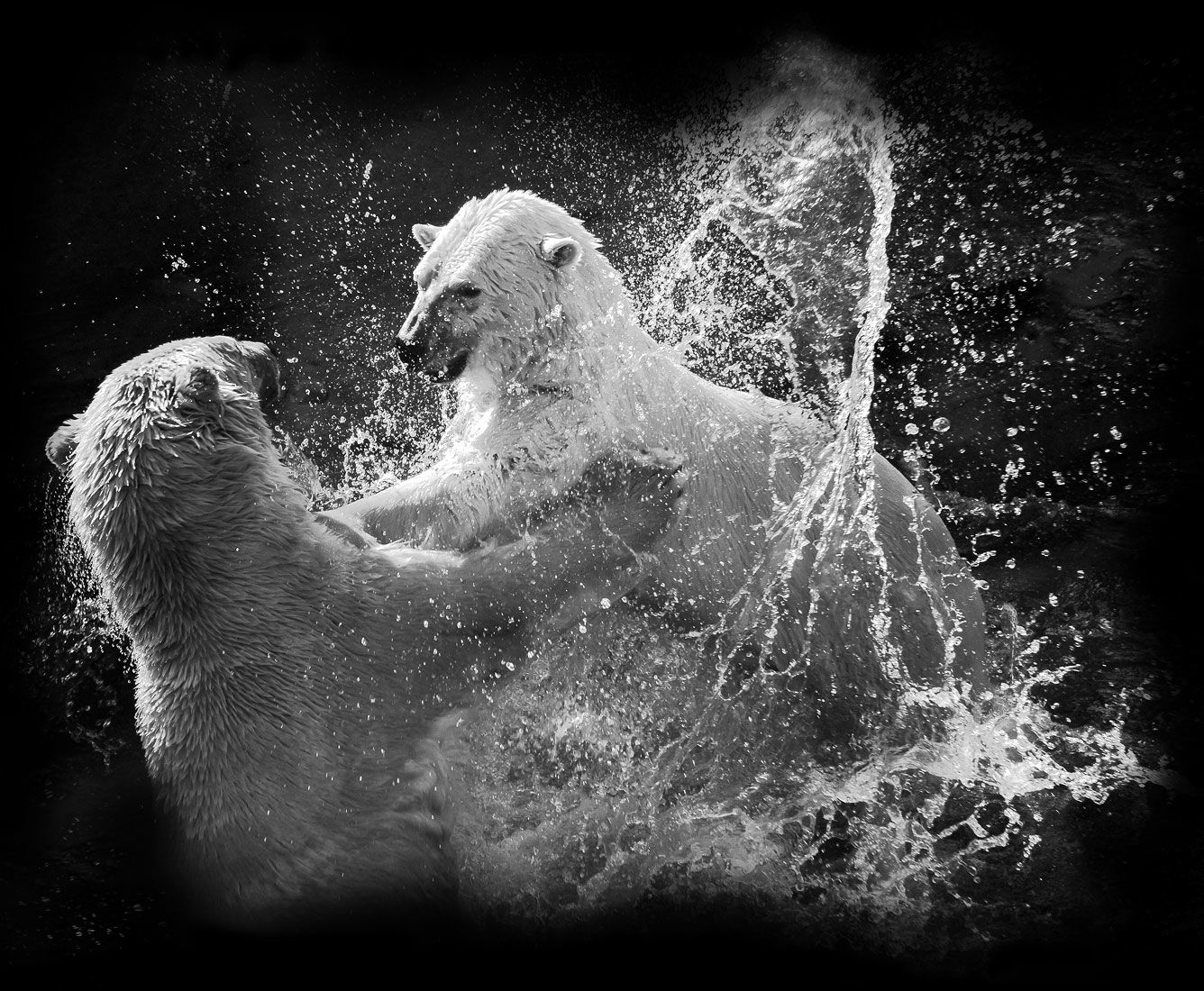
Baercoil and Baerfix
Thread repair and thread armouring. A strong team.
The use of thread inserts creates highly resilient and very wear-resistant threads even in materials with lower strength. They are therefore very popular for strengthening or repairing threaded connections. Of course, with the BAER claim to always offer the highest quality and precision at a fair price. In addition to thread inserts, thread repair sets & assortments, BaerCoil taps and assembly tools are available in a very wide range of dimensions.
Toolfinder
Topseller
Baercoil
Baerfix
Thread inserts made of wire BaerCoil® and self-tapping thread inserts BaerFix® - Bye-bye torn-out threads
There is the repair of external threads on the one hand and the repair of internal threads on the other. Whereas for external threads, i.e. on a screw or bolt, only "re-tapping" with a cutting round die or a hexagon die nut actually works, there are considerably more options for internal threads. We therefore deal mainly with the thread repair of internal threads by means of thread inserts. The principle is always the same: The old broken thread is drilled out and extended. The thread insert then reduces it to the original thread size. BAER offers two different thread repair solutions: The thread repair with BaerCoil® wire thread inserts and the repair of the thread with the BaerFix® self-tapping thread inserts.
Thread repair with wire thread inserts from BaerCoil®
For thread repair with BaerCoil® wire thread inserts, the old thread is first removed and drilled minimally larger. For example, with M 6 threads, 6.3 mm is drilled out, which is just 0.3 mm more than the original thread.
Then a special screw tap is then used to cut the receiving thread for the thread insert. This screw tap is also called STI screw tap for “Screw Thread Inserts”. The thread for the wire thread inserts is standardized according to DIN 8140-2, so all manufacturers adhere to it. The screw tap from other manufacturers are therefore compatible with the thread inserts and the thread repair from BAER.
After the thread has been cut, the thread insert is screwed in using a special inserting tool. We have different inserting tools to choose from, so you can choose whether you want to operate the tool by machine or by hand. Our wire thread insert for thread repair is made of work-hardened stainless steel 1.4301 and is therefore very wear-resistant and high-strength. This guarantees lasting repairs for your threads.
Most wire thread inserts have a tang, which has to be broken after installation - use the tang break tool for this.
At BAER you will find all the required thread repair sets , with which you can always repair one thread size each. For professionals and more ambitious hobby screwdrivers we also offer BaerCoil® thread repair assortments where several thread sizes are always in one assortment case.
The great advantage that comes with the BaerCoil® thread repair system is primarily the very even distribution of forces that can be delivered to many threads by the wire thread insert. This ensures that the repaired thread is significantly stronger and more wear-resistant than the original thread. Due to this thread reinforcement or thread armoring, thread inserts is used today in many lightweight constructions to make threaded connections more stable and to save weight.
The advantages of BaerCoil® at a glance:
- High surface quality of the repaired thread, as it is work-hardened stainless steel
- High corrosion resistance, as A2 stainless steel (material number 1.4301)
- Repairs thread not only, but makes it stronger à thread reinforcement
- Larger contact surface with the receiving material, as the receiving thread of the thread insert is larger than the original thread
- Withstands more forces, as the forces can be better transferred to the somewhat flexible wire
- Saves the environment and resources, as repairing components is often better than replacing them
- Compatible with tools and repair systems with wire thread inserts from other manufacturers, as they are based on the same standards (e.g. DIN 8140)
- Extremely small space requirement, as the thread insert is the smallest possible size and can therefore also be used when there is little carrier material available
- The only disadvantage is the somewhat more complex installation. 4 steps are needed to repair the thread and several special tools, such as the special screw tap and the inserting tool.
BaerFix® thread repair for thread inserts with self-tapping thread inserts
The BaerFix® system for thread repair has thicker-walled thread inserts compared to the BaerCoil® wire thread inserts. Therefore, this repair system is only suitable if sufficient carrier material is available. In addition, these thread inserts cut the holding thread itself when screwed in, so they can only be used in materials with a tensile strength of up to approx. 450 N/mm². All materials above this are too strong and can only be repaired if you pre-cut the holding thread of the thread insert so that the insert no longer has to remove the entire material.
When using thread repair with BaerFix® thread inserts, the core hole is also drilled first. However, this is considerably larger, so for an M 6 thread, the core hole is drilled out at 9.3 mm.
Then the self-tapping thread insert is turned onto a special inserting tool and locked with a lock nut. In addition to the manual inserting tool with lock nuts, there are also machine inserting tools that automatically release the locking and unlocking.
The thread insert is screwed into the hole with cutting slot or cutting hole facing downwards. The lock nuts are loosened and the inserting tool is unscrewed.
The advantages of the thread repair with BaerFix®:
- Saves resources and costs as the repaired thread can be reused
- The BaerFix® system is very easy to use, as only drilling is required and then the thread insert is screwed in.
- Due to the larger external thread of the thread insert, it has more contact surface with the carrier material. The result is wear-resistant threads that are stronger than the original thread.
- Thread inserts made of case-hardened steel, with zinc plating for high-strength threads
- Can also be used for thread reduction if an incorrect thread size has been used.
However, it should be distinguished that BaerFix® self-tapping thread inserts are only suitable for thread repair threads if sufficient material is available. They require a lot of space and the simple self-tapping installation is only possible for materials up to approx. 450 N/mm². For stronger threads, the mounting thread must be pre-cut.
Available are the BaerFix® thread repair kits in single sets per thread size and as BaerFix® thread repair workshop sets with different sizes in an assortment case.
Professional thread repair with BAER
With the high-quality thread repairs BaerCoil® and BaerFix® you can prolong the life of your threads in the long term. 40 years of experience and the continuous development of our products have contributed to the excellent quality of the BAER brand. If you have any questions about BAER or our product range, please feel free to contact us via our contact form - we will advise you with the utmost professionalism and years of expertise. Your enquiry is always welcome at BAER!
FAQ
Threaded inserts
A thread repair kit is a collection of tools and inserts for repairing and reinforcing threads. It is used for the following purposes:
- Repairing damaged threads: allows worn or damaged threads to be restored.
- Reinforcement of threads: Increases durability and stability, especially in soft materials such as aluminum.
- Increasing thread strength: Creates greater strength than without use, especially in susceptible materials.
- Flexibility in material selection: Allows the use of softer materials without compromising thread strength.
- Prevention of thread damage: Protects against stripping or excessive wear in highly stressed joints.
Thread repair kits and inserts are essential tools for mechanics, engineers and DIY enthusiasts looking to create or repair durable and resilient threaded connections.
A thread repair kit is a cost-effective alternative to replacing a component if:
- Only the thread is damaged, but the component itself remains intact.
- Replacement would be expensive or difficult.
- Saving time by repairing quickly on site is important.
- Parts that are difficult to replace are affected.
A thread repair kit helps to save costs, minimize downtime and extend the service life of components. Thread repair kits can also be used to strengthen a thread before damage occurs.
A professionally carried out thread repair:
- Lasts a very long time, often over the entire remaining service life of the component.
- Is just as stable as the original thread.
- In many cases, it can even be more stable than the original thread.
The high durability and stability make thread repairs a reliable and long-term solution for damaged threads.
Yes, a thread repair kit can also be used for severely damaged threads:
- Prerequisite: sufficient material must be available to cut the new thread.
- Effective: A complete repair can often be carried out even in the case of considerable damage.
- Limitations: If there is too much material loss or structural damage to the component, the repair may be impossible.
Thread repair kits offer a versatile solution for various degrees of thread damage as long as the basic structure of the component is intact.
The inserts are used once and are designed for a permanent repair solution:
- Firm anchoring: wire thread inserts are firmly anchored in the carrier material.
- Multiple use of tools: The tools in the repair kit can be used repeatedly.
- Sufficient quantity: A thread repair kit typically contains several inserts for different repairs.
This disposable design ensures reliable and durable thread repair for every application.
There are different sizes of thread inserts that require specific tools for each thread type. (BaerCoil® and BaerFix®)
For the assembly you need:
- Core drill: To drill out the old thread.
- Special tap (EG tap): For cutting the mounting thread. (BaerCoil® only)
- Insertion tool: For screwing in the thread insert.
These tools are available in various sizes to suit the different thread sizes. BaerCoil® offers both hand tools and machine tools, which should be selected according to the application and material.
There are two main types of thread repair kits:
Wire thread inserts (e.g. BaerCoil®):
- Consist of high-quality stainless steel wire with a rhombic cross-section.
- Are wound into a spring thread.
- Provide a permanent and wear-resistant thread.
- Often stronger than the original thread.
Self-tapping thread inserts (e.g. BaerFix®):
- Cut their own holding thread when screwed in.
- Guarantee secure and firm anchoring in the material.
- Made of case-hardened steel, stainless steel or brass.
- Offer high pull-out resistance and freedom from tolerances.
Both types are suitable for different materials and applications, whereby self-tapping inserts are particularly time-saving.
BaerFix® and BaerCoil® are two different thread repair and reinforcement systems from BAER:
BaerCoil®
- Wire thread inserts made from coiled stainless steel wire with a rhombic cross-section
- Slim and space-saving
- For precise thread repairs and reinforcements
- Distribute forces evenly across the threads
- Very high load limits, often higher than with normal threaded connections
- Suitable for various materials and applications
BaerFix®
- Solid, self-tapping threaded bushes
- Thicker-walled than BaerCoil® inserts
- Cut their own holding thread (in materials up to approx. 450 N/mm2 tensile strength)
- Require more carrier material
- Particularly suitable for materials with low shear strength
- Offer high pull-out strength and corrosion resistance
Main differences
- Shape: BaerCoil® are wire coils, BaerFix® are solid bushings.
- Installation method: BaerCoil® are inserted into pre-cut threads, BaerFix® are self-cutting.
- Material requirements: BaerFix® require more backing material than BaerCoil®.
- Area of application: BaerCoil® are more versatile, BaerFix® are particularly suitable for softer materials.
The choice between BaerFix® and BaerCoil® depends on the specific application, the material available and the load requirements. Both systems offer effective solutions for thread repairs and reinforcements, each with their own advantages and disadvantages.
BaerFix
BaerFix® is an innovative thread repair and reinforcement system with the following properties:
- Self-cutting threaded bushes: Solid inserts that cut their own holding thread.
- Material suitability: Ideal for materials with low shear strength and a tensile strength of up to approx. 450 N/mm2.
- Area of application: Repair of damaged or worn threads and reinforcement of existing threads.
- Components: Consists of special inserts and assembly tools.
Advantages:
- Produces heavy-duty and wear-resistant threads.
- Saves resources and costs by reusing repaired threads.
- Easy handling due to direct screwing in after drilling.
- Higher strength than the original thread.
BaerFix® is particularly suitable for materials such as aluminum, light metals, brass, cast iron and plastics. The system offers an effective solution for thread repair and reinforcement in various industrial and DIY applications.
Repairing a damaged thread with the BaerFix® thread repair system is done in three simple steps:
- The damaged thread is drilled out with a core drill.
- If necessary, the hole is countersunk with a countersink.
2. Preparation of the thread insert:
- The BaerFix® thread insert is turned onto the special installation tool.
- The cutting slots of the insert must point downwards.
- The insert is secured with a lock nut.
3. Screwing in the threaded insert:
- The prepared threaded insert is screwed into the hole.
- The BaerFix® insert cuts its own receiving thread.
- After screwing in, the lock nut is loosened and the installation tool is removed.
The result is a new, stable thread that is often more wear-resistant and resilient than the original.
BaerFix® is ideal for:
- Thread repair: Restoring damaged or worn threads.
- Thread reinforcement: Reinforcement of existing threads for higher load-bearing capacity.
- Materials with low shear strength: Ideal for materials such as aluminum, light metals, brass, cast iron and plastics.
- Tensile strength up to 450 N/mm2: Ideal for materials in this strength range.
- Weight-critical applications: Enables weight savings by using lighter materials.
- Space-critical constructions: Provides high strength with minimal space requirements.
- Vibration-intensive environments: Ensures durable, vibration-resistant anchoring.
- Corrosion-prone areas: High corrosion resistance for a wide range of environmental conditions.
BaerFix® is widely used in the automotive industry, in plant and equipment construction, in electrical and laboratory technology as well as in the military and household appliance sectors.
Cutting slots are features of BaerFix® thread inserts:
- Function: Enable independent cutting of the holding thread.
- Position: Located at the lower end of the inserts.
- Advantages: Guarantee firm anchoring, are easy to handle and ideal for thread repairs in materials with low shear strength.
These slots enable safe and efficient thread repair without special prior knowledge.
Cutting holes (i.e. holes in the thread insert) are important elements of BaerFix® thread inserts:
- Function: Enable independent cutting of the holding thread
- Advantages: Simplify installation, ensure a precise fit and increase the holding force in the material
- Special feature compared to cutting slots: The inserts are more stable and can also be used in materials that are difficult to machine.
These holes make BaerFix® an efficient solution for thread repairs, especially in softer materials, without requiring prior knowledge or special tools.
Yes, BaerFix® is ideal for repairing spark plug threads:
- Special design: BaerFix® thread inserts are available specifically for spark plug threads.
- Easy to use: The repair can be carried out without any special prior knowledge.
- Robust solution: Repaired threads withstand higher loads and guarantee optimum hold.
- Sealing: The thread insert is inserted in such a way that the spark plug sealing ring grips optimally.
- Reinforcement: The repaired thread is often more stable than the original thread.
Repair process:
- Drill core hole
- Mount BaerFix® thread insert on installation tool
- Screw in the thread insert
- Remove the installation tool
BaerFix® thread inserts offer an effective and permanent solution for damaged or worn spark plug threads without having to replace the cylinder head.
BaerCoil
BaerCoil® is an innovative thread repair and reinforcement system:
- Main component: Wire thread inserts made from work-hardened stainless steel
- Function: Repair and reinforcement of damaged or stressed threads
- Areas of application: Mechanical engineering, automotive industry, electrical engineering, medical technology, aerospace industry
Advantages:
- Higher load capacity than the original thread
- Improved wear resistance and corrosion resistance
- Even force distribution on thread turns
- Enables weight savings thanks to smaller thread diameters
Application: Particularly suitable for materials with low shear strength such as aluminum and plastic
Installation: Three-stage process – core hole drilling, thread cutting, insertion of the thread insert
BaerCoil® offers a sustainable and cost-effective solution for thread repair and reinforcement that extends component life and minimizes scrap.
Repairing a damaged thread with BaerCoil® is a four-step process:
- The damaged thread is drilled out slightly larger with a twist drill.
- Optionally, the hole can be countersunk with a countersink.
2. Thread cutting:
- A new holding thread (EG thread or STI thread) is cut using a special BaerCoil® tap.
- Cutting oil is recommended to improve the quality of the thread.
3. Install the thread insert:
- The wire thread insert is placed on the insertion tool and screwed into the new holding thread.
- The insert sits 1/4 to 1/2 turn below the surface.
4. Break the tang:
- The tang of the thread insert is broken off to ensure a clean threaded hole.
Advantages of BaerCoil®:
- The repaired thread is often stronger and more resilient than the original.
- Suitable for materials with low shear strength such as aluminum and plastic.
- High wear resistance and corrosion resistance due to stainless steel wire thread inserts.
BaerCoil® offers an efficient and durable solution for the repair and reinforcement of damaged threads in various industrial and technical applications.
The following tools are required to install a BaerCoil® thread insert:
- Twist drill: For drilling out the damaged thread.
- Tap (EG tap or STI tap): For cutting the receiving thread for the thread insert.
- Installation tool: A special tool for screwing in the thread insert.
- Tang breaker: Required for inserts with tang.
Additional helpful tools:
- Countersink: Optional for countersinking the hole.
- Cutting oil: Recommended for better quality thread cutting.
These BaerCoil® tools are required to prepare the thread precisely and insert the insert correctly. They ensure a professional installation that results in a stable and resilient repaired thread.
BaerCoil® thread inserts are particularly suitable for:
- Highly stressed applications: Improve the load-bearing capacity and wear resistance of threads.
- Materials with low shear strength: Ideal for metals such as aluminum, brass and magnesium alloys.
- Automotive, aerospace: Proven in demanding technical environments.
- Mechanical engineering: Provides solutions for precise and resilient threaded connections.
- Military equipment: Meets high demands for stability and reliability.
- Thermally stressed environments: Withstands high temperatures (up to 550°C in the InconelX750 version).
- Thread repair: Allows damaged threads to be restored, often stronger than the original.
- Weight-critical designs: Allows the use of lighter materials while maintaining strength.
- Corrosion prone areas: Provides excellent corrosion resistance through stainless steel construction.
- Precision applications: Ensures high surface finish and accurate fits.
BaerCoil® inserts reduce the risk of material failure and enable the optimization of threaded connections in a wide range of industrial applications.
BaerCoil® taps differ from standard taps in the following ways:
- Larger outside diameter: BaerCoil® taps have a larger outside diameter to cut the holding thread for the wire thread insert.
- More precise cutting pattern: They produce a more precise cutting pattern and burr-free cutting edges, which is important for the exact seating of the wire thread inserts.
- Special surface treatment: BaerCoil® taps have a specially treated surface that ensures clean chip evacuation.
- Adapted rake angles: They have suitable rake angles for the individual cutting behavior of different materials.
- High-quality steel: BaerCoil® taps are made of high-quality steel, which increases their durability.
- Special hardening process: A homogeneous hardening structure is achieved through special hardening processes and repeated tempering, which contributes to toughness and stability.
These properties make BaerCoil® taps particularly suitable for working with wire thread inserts and ensure a true-to-gauge thread with an excellent surface finish and long tool life.
The installation tool is an essential instrument for the correct installation of BaerCoil® thread inserts:
- Main function: Precise insertion of the thread insert into the prepared receiving thread.
- Exact positioning: Ensures the correct depth and alignment of the insert.
- Insert protection: Prevents damage during installation.
- Easy handling: Enables controlled and efficient installation.
Using the installation tool:
- Place the threaded insert on the installation tool.
- Carefully insert the insert into the prepared thread.
- Turn the tool clockwise until the insert is fully inserted.
- Remove the installation tool, leaving the insert in position.
The installation tool is essential for a professional and reliable installation of BaerCoil® thread inserts, which ensures optimum function and durability of the repaired threads.
The different types of tools for BaerCoil® thread inserts differ as follows:
- For manual insertion of the thread inserts
- With depth limitation by locking ring
- 7 mm square drive for use with tap wrench or tool ratchet
2. Machine tool:
- Designed for machine use
- Enables faster work with larger quantities
- Suitable for automated processes
3. NoTang tool:
- Specially developed for the NoTang tangless system
- Compatible with NoTang thread inserts that have small notches instead of tangs
- Simplifies the installation process as no tang breaking is required
Main differences:
- Application: Manual (installation tool) vs. machine (machine tool) vs. specifically for NoTang system (NoTang tool)
- Compatibility: NoTang tools can only be used with NoTang thread inserts
- Efficiency: Machine tools for higher quantities, NoTang for simplified process without tang breakage
All tool types serve the purpose of installing BaerCoil® thread inserts precisely and efficiently, but are optimized for different application scenarios and product lines.
Unscrewing tools are special instruments for removing stuck or defective threaded inserts. They are used to unscrew threaded inserts from materials without damaging the surrounding material.
Main functions:
- Removal of seized threaded inserts
- Suitable for metric (M3 to M10) and inch threads (3/16 to 3/8)
- Application: Insert into the threaded opening and turn counterclockwise
Advantages:
- Enables easy disassembly without damaging the material
- Suitable for manual and machine application
Unscrewing tools are indispensable for the maintenance and renewal of threaded connections, as they enable the quick and safe removal of threaded inserts.
BaerCoil® offers three main types of threaded inserts:
- Free-running inserts: Suitable for standard applications, ideal for frequently loosened connections.
- Screw grip inserts: Provide additional holding power through clamping turns, especially useful in high vibration environments.
- NoTang inserts: Spigotless design that leaves no spigots in the component, increasing safety and simplifying installation.
These variants allow flexible adaptation to different requirements and environments.
The BaerCoil® PRO repair set differs from standard sets in the following ways:
- Contains core hole drills and machine taps
- Provides additional tools for professional users
- Enables more efficient work with larger quantities
- Suitable for industrial use and workshops
- Contains higher quality and more durable components
The PRO set is therefore specially tailored to the needs of professionals and intensive users who frequently have to carry out thread repairs.
BaerCoil® thread inserts can be used in a variety of materials, e.g.:
- Metals: aluminum, magnesium, titanium, copper, steel and their alloys
- Plastics: Suitable for various types of plastic
They are also suitable for:
- Brass and bronze
- Cast iron
- Laminates
BaerCoil® thread inserts are particularly beneficial in materials with low shear strength, where they increase thread strength and load capacity. They offer protection against wear and corrosion, making them a versatile solution for various applications in different materials.
BaerCoil® thread inserts are particularly useful in the following industries and applications:
- Automotive: For engines, transmissions, radiators and body parts where heavy-duty threads are required.
- Mechanical engineering: For reinforcing and repairing threads in components subject to high loads.
- Aerospace: For engines and component fastenings, thanks to their high temperature and corrosion resistance.
- Electrical and laboratory technology: In medical devices and technical housings.
- Military equipment: For aircraft, tanks and weapons where maximum strength and reliability are required.
The inserts provide protection against wear, increase pull-out strength and minimize material consumption, making them ideal for demanding technical applications.
Threaded inserts can have a very long service life in heavy-duty applications:
- Durability: they last for years, even under heavy loads.
- Material dependency: Particularly durable when installed in hard materials such as steel or aluminum.
- Wear protection: Their stainless steel construction ensures high resistance to corrosion and abrasion.
The service life depends on the application and environmental conditions, but is extremely robust when installed and used correctly.